Introduction
Flex PCB Soldering is a crucial process in the manufacturing of electronic devices. It involves attaching surface mount devices (SMDs) to a flexible printed circuit board (Flex PCB) using solder. Flex PCBs are increasingly popular due to their ability to conform to various shapes and sizes, making them ideal for compact and portable devices. However, soldering SMDs onto Flex PCBs requires careful attention to detail and proper technique to ensure a reliable and durable connection.
In this article, we will discuss five essential things you need to pay attention to when Flex PCB soldering SMD components. By following these guidelines, you can achieve high-quality solder joints and minimize the risk of defects or failures in your electronic assemblies.
1. Choosing the Right Solder and Flux
Solder Alloy Selection
When it comes to Flex PCB soldering, selecting the appropriate solder alloy is crucial. The most commonly used solder alloys for SMD soldering are tin-lead (SnPb) and lead-free (Pb-free) alloys. Lead-free solders, such as Sn99.3Cu0.7 (SAC307) or Sn96.5Ag3.0Cu0.5 (SAC305), have become the standard due to environmental regulations like RoHS.
Consider the following factors when choosing a solder alloy:
- Melting temperature
- Wetting properties
- Mechanical strength
- Compatibility with the SMD components and Flex PCB materials
Solder Alloy | Composition | Melting Point (°C) | Features |
---|---|---|---|
Sn63Pb37 | 63% Tin, 37% Lead | 183 | Excellent wetting, easy to use |
SAC305 | 96.5% Tin, 3% Silver, 0.5% Copper | 217-220 | Good mechanical strength, RoHS compliant |
SAC307 | 99.3% Tin, 0.7% Copper | 227-229 | Better thermal cycling performance, RoHS compliant |
Flux Selection
Flux is an essential component in the soldering process that helps remove oxides, improve wetting, and promote the formation of a strong solder joint. There are three main types of flux:
- Rosin-based (RMA, RA, and no-clean)
- Water-soluble
- No-clean
For Flex PCB soldering, no-clean flux is often preferred due to its minimal residue and the difficulty in cleaning Flex PCBs after soldering. When selecting a flux, consider its activity level, compatibility with the solder alloy, and the specific requirements of your application.
2. Surface Preparation and Cleanliness
Cleaning the Flex PCB and SMD Components
Before soldering, it is essential to ensure that the Flex PCB and SMD component surfaces are clean and free from contaminants. Contaminants such as dirt, grease, or oxidation can hinder the formation of a proper solder joint, leading to defects or failures.
To clean the surfaces:
- Use isopropyl alcohol (IPA) or a specialized PCB cleaner to remove any dirt or grease.
- If the surfaces are heavily oxidized, consider using a mild abrasive or chemical cleaner designed for PCB cleaning.
- After cleaning, allow the surfaces to dry completely before proceeding with soldering.
Handling and Storage
Proper handling and storage of Flex PCBs and SMD components are crucial to maintain their cleanliness and prevent damage. Follow these guidelines:
- Wear clean, lint-free gloves when handling Flex PCBs and SMD components to avoid transferring oils and contaminants from your skin.
- Store Flex PCBs and SMD components in a clean, dry, and temperature-controlled environment to prevent oxidation and moisture absorption.
- Use anti-static packaging or containers to protect components from electrostatic discharge (ESD) damage.
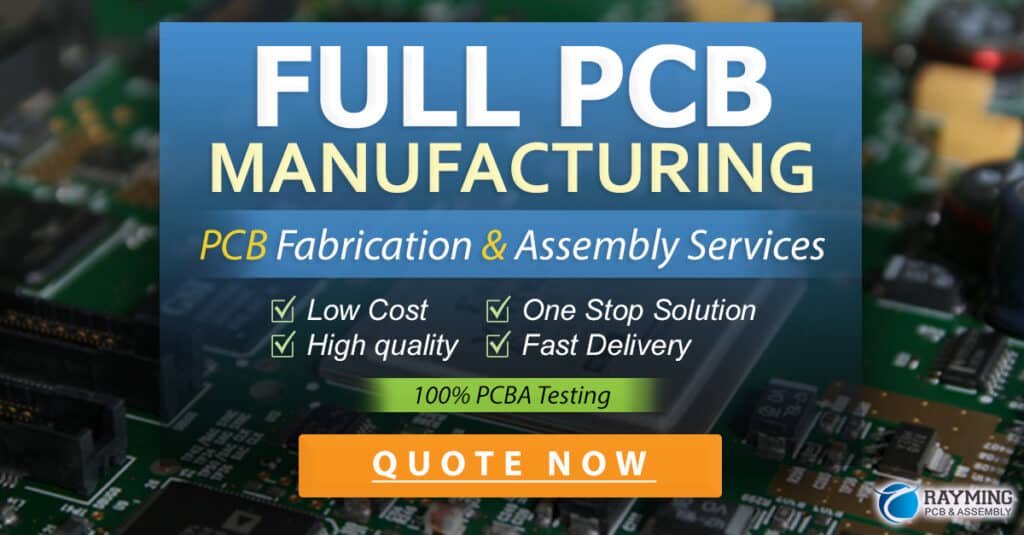
3. Solder Paste Application and Component Placement
Solder Paste Selection
Solder paste is a mixture of solder alloy particles and flux that is used to form the solder joint between the SMD component and the Flex PCB. When selecting a solder paste, consider the following factors:
- Compatibility with the chosen solder alloy and flux
- Particle size and distribution
- Viscosity and printing properties
- Shelf life and storage requirements
Solder Paste Application Methods
There are two primary methods for applying solder paste onto Flex PCBs:
- Stencil Printing
- A stencil with apertures corresponding to the SMD pad locations is placed over the Flex PCB.
- Solder paste is applied over the stencil and spread using a squeegee, depositing the paste onto the pads.
-
Stencil printing provides precise and consistent solder paste deposits.
-
Dispensing
- Solder paste is applied directly onto the SMD pads using a pneumatic or positive displacement dispenser.
- Dispensing is suitable for low-volume production or prototyping, where stencil printing may not be practical.
Component Placement
After applying the solder paste, SMD components must be placed accurately onto the Flex PCB pads. This can be done manually using tweezers for low-volume production or prototyping. For high-volume production, automated pick-and-place machines are used to achieve faster and more precise component placement.
When placing SMD components, ensure that:
- The component is aligned correctly with the pads.
- The component is centered on the solder paste deposit.
- There is sufficient solder paste between the component and the pad for a reliable joint.
4. Reflow Soldering Process
Reflow Oven Setup
Reflow soldering is the process of heating the solder paste to melt the solder alloy particles and form a permanent connection between the SMD component and the Flex PCB. A reflow oven is used to control the temperature profile during the soldering process.
When setting up the reflow oven, consider the following:
- Set the temperature profile according to the solder paste manufacturer’s recommendations, taking into account the specific requirements of the Flex PCB and SMD components.
- Ensure that the oven is calibrated and the temperature sensors are functioning accurately.
- Adjust the conveyor speed to ensure that the Flex PCB spends the appropriate amount of time in each temperature zone.
Reflow Temperature Profile
A typical reflow temperature profile consists of four stages:
- Preheat: The Flex PCB is gradually heated to activate the flux and evaporate any solvents.
- Thermal Soak: The temperature is maintained to allow the components and PCB to reach a uniform temperature.
- Reflow: The temperature is increased above the solder alloy’s melting point, allowing the solder to melt and form the joint.
- Cooling: The PCB is cooled gradually to allow the solder joints to solidify and prevent thermal shock.
Reflow Stage | Temperature Range (°C) | Time (seconds) |
---|---|---|
Preheat | 25-150 | 60-120 |
Thermal Soak | 150-180 | 60-120 |
Reflow | 220-250 | 30-60 |
Cooling | 250-25 | 30-60 |
Ensure that the reflow temperature profile is optimized for your specific solder paste, Flex PCB, and SMD components to achieve the best soldering results.
5. Inspection and Quality Control
Visual Inspection
After the reflow soldering process, it is essential to visually inspect the solder joints to identify any defects or issues. Common solder joint defects include:
- Bridging: Solder connecting adjacent pads or components
- Insufficient solder: Lack of solder, resulting in a weak or open connection
- Tombstoning: One end of the component lifting off the pad due to uneven heating or solder paste application
- Solder balls: Small spheres of solder that can cause short circuits
Visual inspection can be performed using a magnifying lens or microscope, depending on the size of the components and the level of detail required.
Automated Optical Inspection (AOI)
For high-volume production, automated optical inspection (AOI) systems can be used to quickly and accurately detect solder joint defects. AOI systems use cameras and image processing algorithms to compare the soldered PCB to a reference image, identifying any deviations or anomalies.
AOI systems can detect a wide range of defects, including:
- Component presence and placement
- Solder joint quality
- Solder paste alignment and volume
- Polarity and orientation of components
Electrical Testing
In addition to visual inspection, electrical testing is essential to ensure that the soldered Flex PCB functions as intended. Electrical testing can be performed using various methods, such as:
- In-circuit testing (ICT): Probes are used to test individual components and circuits on the PCB.
- Flying probe testing: Movable probes test specific points on the PCB without the need for a custom test fixture.
- Functional testing: The assembled PCB is tested in its final application to ensure proper operation and performance.
Electrical testing helps identify any functional issues or defects that may not be visible during visual inspection, ensuring the overall quality and reliability of the soldered Flex PCB.
Frequently Asked Questions (FAQ)
- What is the difference between Flex PCBs and rigid PCBs?
-
Flex PCBs are made from flexible materials, such as polyimide, which allows them to bend and conform to various shapes. Rigid PCBs, on the other hand, are made from a rigid substrate, such as FR-4, and maintain a fixed, planar shape.
-
Can I use the same soldering techniques for Flex PCBs as I do for rigid PCBs?
-
While many of the soldering techniques used for rigid PCBs can be applied to Flex PCBs, there are some key differences to consider. Flex PCBs require more careful handling, as they are more susceptible to damage from heat and mechanical stress. It is essential to use the appropriate temperature profiles, solder alloys, and flux to ensure reliable solder joints on Flex PCBs.
-
How do I prevent damage to Flex PCBs during the soldering process?
-
To prevent damage to Flex PCBs during soldering, follow these guidelines:
- Use a controlled temperature profile to avoid overheating the PCB.
- Support the Flex PCB to prevent excessive bending or flexing during soldering.
- Handle the Flex PCB with care, avoiding sharp bends or creases.
- Use a low-stress solder alloy and no-clean flux to minimize the need for post-soldering cleaning.
-
What are some common challenges when soldering SMDs on Flex PCBs?
-
Some common challenges when soldering SMDs on Flex PCBs include:
- Maintaining the correct alignment and placement of components on the flexible substrate.
- Ensuring even heating and cooling of the PCB to prevent warping or damage.
- Achieving reliable solder joints despite the increased thermal expansion and contraction of the flexible materials.
- Handling and cleaning the Flex PCB without causing damage or contamination.
-
How can I ensure the long-term reliability of solder joints on Flex PCBs?
- To ensure the long-term reliability of solder joints on Flex PCBs, consider the following:
- Use a solder alloy with good mechanical strength and thermal cycling performance, such as SAC305 or SAC307.
- Ensure proper surface preparation and cleanliness to promote good solder wetting and adhesion.
- Optimize the reflow temperature profile for the specific solder paste, Flex PCB, and SMD components.
- Perform thorough visual inspection and electrical testing to identify any defects or issues early in the production process.
- Use strain relief techniques, such as adhesives or stiffeners, to minimize stress on the solder joints during flexing.
Conclusion
Soldering SMDs on Flex PCBs requires careful attention to detail and the use of appropriate techniques and materials. By following the five key aspects discussed in this article – choosing the right solder and flux, ensuring proper surface preparation and cleanliness, applying solder paste and placing components correctly, optimizing the reflow soldering process, and performing thorough inspection and quality control – you can achieve high-quality, reliable solder joints on your Flex PCB assemblies.
Remember to handle Flex PCBs with care, use the appropriate tools and equipment, and stay up-to-date with the latest industry best practices and guidelines. With the proper knowledge and techniques, you can successfully solder SMDs on Flex PCBs and create innovative, reliable electronic devices that meet the demands of today’s market.
No responses yet