Introduction to Stepper Motors
Stepper motors are a type of brushless DC electric motor that divides a full rotation into a number of equal steps. They provide precise positioning and speed control without requiring a closed-loop feedback control system. Unlike regular DC motors that rotate continuously when voltage is applied, stepper motors move in discrete steps, allowing them to achieve very precise positioning.
Stepper motors come in various types, sizes, and specifications to suit different applications. One of the most common and affordable stepper motors is the 28BYJ-48, a 5-wire, 5V unipolar stepper motor widely used in DIY projects, 3D printers, CNC machines, and robotics.
Stepper Motor Basics
Before diving into the specifics of the 28BYJ-48 stepper motor, let’s first understand some basic concepts and terminology related to stepper motors.
Step Angle
The step angle is the angle the motor shaft rotates for each step. It is determined by the number of teeth on the rotor and the number of phases in the motor. The step angle can be calculated using the following formula:
Step Angle = 360° / (Number of Teeth × Number of Phases)
For example, a stepper motor with 200 teeth and 4 phases will have a step angle of 1.8° (360° / (200 × 4)).
Steps per Revolution
The number of steps required for the motor shaft to complete one full rotation (360°) is called steps per revolution. It can be calculated by dividing 360° by the step angle.
Steps per Revolution = 360° / Step Angle
Using the previous example, a stepper motor with a step angle of 1.8° will have 200 steps per revolution (360° / 1.8°).
Holding Torque
Holding torque, also known as detent torque, is the maximum torque the stepper motor can generate to maintain its position when no current is applied to the windings. This torque is usually lower than the dynamic torque, which is the torque generated when the motor is in motion.
Stepper Motor Drivers
Stepper motors require a driver to control the current flow through the windings and generate the magnetic fields necessary for rotation. The driver receives step and direction signals from a microcontroller or a computer and translates them into the appropriate sequence of pulses to energize the motor windings.
Some common stepper motor drivers include:
- ULN2003: A Darlington transistor array IC that can drive up to 500 mA per channel
- A4988: A microstepping bipolar stepper motor driver capable of driving up to 2A per coil
- DRV8825: Another microstepping bipolar stepper motor driver with adjustable current limit up to 2.5A per coil
28BYJ-48 Stepper Motor Specifications
Now that we have covered some basic concepts let’s take a closer look at the specifications of the 28BYJ-48 stepper motor.
Specification | Value |
---|---|
Rated Voltage | 5V DC |
Number of Phases | 4 |
Stride Angle | 5.625° / 64 |
Frequency | 100 Hz |
DC Resistance | 50 Ω ± 7% (25°C) |
Idle In-traction Frequency | > 600 Hz |
Idle Out-traction Frequency | > 1000 Hz |
In-traction Torque | > 34.3 mN.m (120 Hz) |
Self-positioning Torque | > 34.3 mN.m |
Friction Torque | 600-1200 gf.cm |
Pull-in Torque | 300 gf.cm |
Insulated Resistance | > 10 MΩ (500V) |
Insulated Electricity Power | 600 VAC / 1 mA / 1 s |
Insulation Grade | A |
Rise in Temperature | < 40 K (120 Hz) |
Noise | < 35 dB (120 Hz, no load, 10 cm) |
The 28BYJ-48 is a unipolar stepper motor, meaning that it has five wires – one common wire and four coil wires. The common wire is typically connected to the positive voltage supply, while the coil wires are energized in a specific sequence to create the stepping motion.
Wiring
The color code for the wires may vary depending on the manufacturer, but a common configuration is as follows:
Wire Color | Function |
---|---|
Red | +5V (VCC) |
Blue | Coil 1 |
Pink | Coil 2 |
Yellow | Coil 3 |
Orange | Coil 4 |
To control the 28BYJ-48 stepper motor, you can use a driver board like the ULN2003. The driver board simplifies the wiring and provides the necessary current amplification to drive the motor coils.
Stepping Modes
The 28BYJ-48 stepper motor supports various stepping modes, which determine the sequence in which the coils are energized and the resulting step size.
Full-Step Mode
In full-step mode, only one coil is energized at a time. This mode provides the highest torque but the lowest resolution. The motor takes eight steps to complete one full rotation, resulting in a step angle of 45° (360° / 8).
Half-Step Mode
Half-step mode alternates between energizing one coil and two adjacent coils simultaneously. This mode doubles the resolution compared to full-step mode, resulting in a step angle of 22.5° (360° / 16). However, the torque is slightly reduced.
Microstepping Mode
Microstepping is a technique that further increases the resolution by controlling the current in the coils to create intermediate steps. Common microstepping modes for the 28BYJ-48 include 1/8, 1/16, and 1/32 steps. While microstepping improves the smoothness of motion, it comes at the cost of reduced torque.
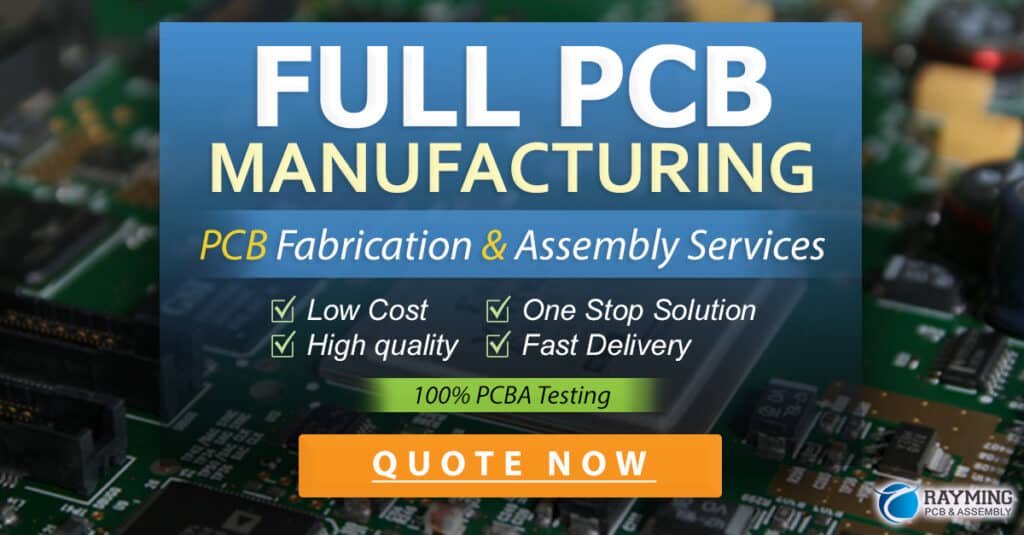
Controlling the 28BYJ-48 Stepper Motor
To control the 28BYJ-48 stepper motor, you’ll need a microcontroller, such as an Arduino, and a stepper motor driver, like the ULN2003. Here’s a basic example of how to control the motor using an Arduino and the ULN2003 driver board:
Wiring Diagram
[Insert wiring diagram image here]
Arduino Code
#include <Stepper.h>
const int stepsPerRevolution = 2048; // Change this to match your motor
const int motorSpeed = 15; // Adjust the speed as needed
// Initialize the stepper library
Stepper myStepper(stepsPerRevolution, 8, 9, 10, 11);
void setup() {
// Set the motor speed (RPM)
myStepper.setSpeed(motorSpeed);
}
void loop() {
// Step one revolution in one direction
myStepper.step(stepsPerRevolution);
delay(500);
// Step one revolution in the other direction
myStepper.step(-stepsPerRevolution);
delay(500);
}
This code uses the Arduino Stepper library to control the 28BYJ-48 motor. The stepsPerRevolution
variable is set to 2048, which is the number of steps required for a full rotation when using the ULN2003 driver in half-step mode. You can adjust the motorSpeed
variable to change the rotation speed of the motor.
In the loop()
function, the code steps the motor one full revolution in one direction, pauses for 500 milliseconds, and then steps one full revolution in the opposite direction.
Applications of the 28BYJ-48 Stepper Motor
The 28BYJ-48 stepper motor is widely used in various applications due to its low cost, precision, and ease of control. Some common applications include:
-
3D Printers: Stepper motors are used to control the movement of the extruder and the positioning of the print bed.
-
CNC Machines: Stepper motors enable precise control of the X, Y, and Z axes in CNC routers, mills, and lathes.
-
Robotics: Stepper motors are used in robotic arms, grippers, and mobile robots for precise positioning and movement control.
-
Automated Systems: Stepper motors are employed in automated dispensing systems, sorting machines, and conveyor belts.
-
Camera and Antenna Control: Stepper motors enable precise pointing and tracking of cameras and antennas.
Advantages and Disadvantages of the 28BYJ-48 Stepper Motor
Advantages
-
Low cost: The 28BYJ-48 is one of the most affordable stepper motors available, making it an attractive option for hobbyists and budget-conscious projects.
-
Precise positioning: Stepper motors provide accurate and repeatable positioning without the need for a closed-loop feedback system.
-
Easy to control: With the help of stepper motor drivers and libraries, controlling the 28BYJ-48 is relatively straightforward, even for beginners.
-
Wide availability: The 28BYJ-48 is widely available from various suppliers, making it easy to source for projects.
Disadvantages
-
Low torque: Compared to other stepper motors, the 28BYJ-48 has relatively low torque, limiting its use in applications that require high holding or dynamic torque.
-
Slow speed: The maximum speed of the 28BYJ-48 is limited, making it unsuitable for high-speed applications.
-
Noise: Stepper motors, including the 28BYJ-48, can generate audible noise during operation, which may be a concern in certain environments.
-
Limited power handling: The 28BYJ-48 is designed for low-voltage, low-current applications and may not be suitable for projects that require higher power handling capabilities.
Frequently Asked Questions (FAQ)
- What is the difference between a unipolar and bipolar stepper motor?
-
A unipolar stepper motor, like the 28BYJ-48, has five or six wires and a common center tap for each coil. This allows for simplified control using a single power supply. In contrast, a bipolar stepper motor has four wires (two for each coil) and requires a more complex driver to reverse the current direction in the coils.
-
Can I use the 28BYJ-48 stepper motor without a driver board?
-
While it is possible to control the 28BYJ-48 directly from a microcontroller, using a driver board like the ULN2003 is highly recommended. The driver board provides the necessary current amplification and protection for the motor coils and simplifies the wiring and control logic.
-
How do I increase the torque of the 28BYJ-48 stepper motor?
-
To increase the torque of the 28BYJ-48, you can try the following:
- Increase the current supplied to the motor (within the specified limits)
- Use a higher voltage power supply (up to 12V)
- Reduce the stepping speed
- Use a gearbox or pulley system to increase the mechanical advantage
-
What is the maximum speed I can achieve with the 28BYJ-48 stepper motor?
-
The maximum speed of the 28BYJ-48 depends on various factors, such as the driver, power supply, and load. In general, the motor can achieve speeds up to 15-20 RPM (revolutions per minute) without significant loss of torque. Higher speeds are possible but may result in reduced torque and increased vibration.
-
Can I use the 28BYJ-48 stepper motor in a 3D printer?
- Yes, the 28BYJ-48 can be used in small, low-cost 3D printers for controlling the extruder and print bed movement. However, due to its limited torque and speed, it may not be suitable for larger or high-performance 3D printers, which typically require more powerful stepper motors like the NEMA 17.
Conclusion
The 28BYJ-48 is a versatile and affordable 5-wire, 5V unipolar stepper motor that is widely used in various DIY projects, robotics, and automated systems. Despite its limitations in torque and speed, the 28BYJ-48 offers precise positioning and easy control, making it an attractive choice for hobbyists and beginners.
By understanding the basic concepts of stepper motors, the specifications of the 28BYJ-48, and how to control it using a microcontroller and driver board, you can successfully integrate this motor into your projects and explore a wide range of applications.
As you gain experience working with the 28BYJ-48 and other stepper motors, you’ll be able to create more advanced and sophisticated systems that leverage the precision and reliability of these essential components in the world of electronics and automation.
No responses yet