Introduction to PCB Essentials
Printed Circuit Boards (PCBs) are the backbone of modern electronics. They provide a platform for electrical components to be mounted and connected, enabling the creation of complex circuits that power our devices. In this comprehensive article, we will dive into the essentials of 2 layer PCBs, exploring their design, manufacturing, and applications.
What is a 2 Layer PCB?
A 2 layer PCB, as the name suggests, consists of two conductive layers: a top layer and a bottom layer. These layers are typically made of copper and are separated by an insulating material called the substrate. The top layer is where the majority of components are placed and routed, while the bottom layer is primarily used for power and ground planes.
Advantages of 2 Layer PCBs
2 layer PCBs offer several advantages over single layer boards:
- Increased circuit density: With two layers, more components can be accommodated on the same board size.
- Improved signal integrity: The additional layer allows for better separation of signals, reducing crosstalk and interference.
- Enhanced power distribution: The bottom layer can be dedicated to power and ground planes, providing a stable and efficient power supply to the components.
- Cost-effective: 2 layer PCBs are more economical to manufacture compared to multi-layer boards, making them suitable for low to medium complexity projects.
Designing a 2 Layer PCB
Designing a 2 layer PCB involves several key steps:
Schematic Creation
The first step is to create a schematic diagram that represents the electrical connections between components. This is typically done using Electronic Design Automation (EDA) software. The schematic captures the logical design of the circuit and serves as a blueprint for the PCB layout.
Component Placement
Once the schematic is complete, the next step is to place the components on the PCB layout. This involves arranging the components in a way that minimizes the overall board size, reduces signal path lengths, and ensures proper spacing for manufacturing and assembly.
Routing
After component placement, the connections between the components are routed using copper traces. In a 2 layer PCB, the top layer is primarily used for signal routing, while the bottom layer is used for power and ground planes. The goal is to create efficient and reliable connections while adhering to design rules and constraints.
Design Rule Check (DRC)
Before finalizing the PCB layout, it is crucial to perform a Design Rule Check (DRC). DRC ensures that the design meets the manufacturing specifications and guidelines, such as minimum trace width, spacing, and hole sizes. It helps identify and resolve any potential issues that could lead to manufacturing defects or reliability problems.
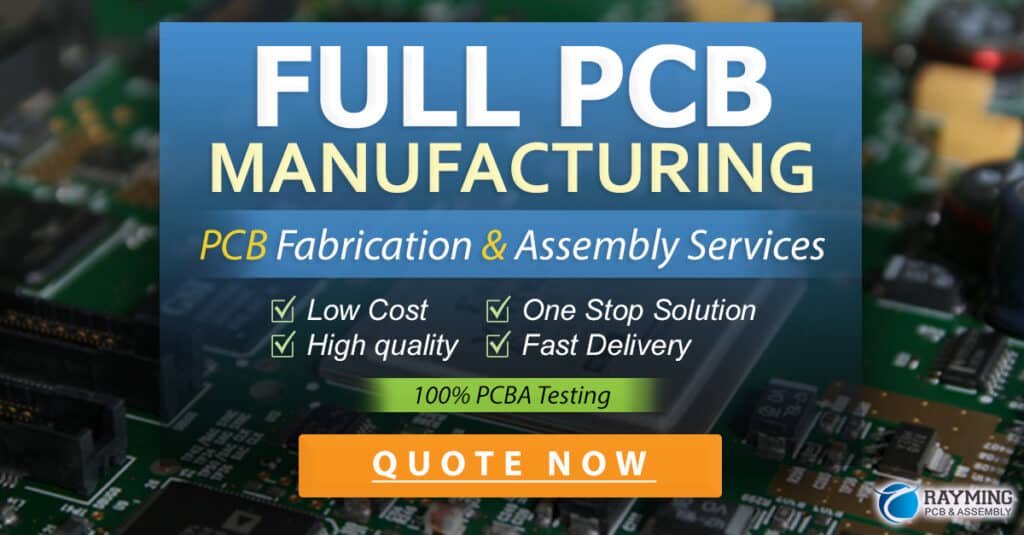
Manufacturing a 2 Layer PCB
The manufacturing process for a 2 layer PCB involves several steps:
- PCB Fabrication: The PCB design files are sent to a PCB fabrication house, where the copper layers are etched, drilled, and plated according to the design specifications.
- Solder Mask Application: A protective coating called solder mask is applied to the PCB surface, leaving only the exposed pads and connection points.
- Silkscreen Printing: Text, symbols, and component designators are printed on the PCB surface using silkscreen printing for easy identification and assembly.
- Surface Finish: A surface finish, such as HASL (Hot Air Solder Leveling) or ENIG (Electroless Nickel Immersion Gold), is applied to the exposed copper pads to protect them from oxidation and enhance solderability.
- Electrical Testing: The manufactured PCBs undergo electrical testing to ensure proper connectivity and functionality before being shipped to the customer.
Applications of 2 Layer PCBs
2 layer PCBs find applications in a wide range of industries and products, including:
- Consumer Electronics: Smartphones, tablets, laptops, and IoT devices often utilize 2 layer PCBs for their internal circuitry.
- Automotive Electronics: 2 layer PCBs are used in various automotive systems, such as infotainment, sensors, and control modules.
- Medical Devices: Medical equipment, such as patient monitors and diagnostic tools, rely on 2 layer PCBs for their electronic subsystems.
- Industrial Automation: 2 layer PCBs are employed in industrial control systems, sensors, and automation equipment.
- Aerospace and Defense: Avionics systems, communication devices, and military equipment often incorporate 2 layer PCBs for their reliability and performance.
Designing for Manufacturability (DFM)
To ensure a smooth and successful manufacturing process, it is important to follow Designing for Manufacturability (DFM) guidelines when creating a 2 layer PCB. Some key considerations include:
- Adhering to the manufacturer’s design rules and specifications.
- Providing adequate clearances and spacing between components and traces.
- Avoiding sharp angles and using rounded corners for traces to reduce stress and improve reliability.
- Minimizing the number of vias and ensuring proper via sizing and spacing.
- Incorporating testability features, such as test points and boundary scan, for easier debugging and quality control.
FAQs
Q1: What is the typical thickness of a 2 layer PCB?
A1: The typical thickness of a 2 layer PCB ranges from 0.8mm to 1.6mm, with 1.6mm being the most common. However, the exact thickness can vary depending on the specific requirements of the project and the chosen PCB manufacturer.
Q2: Can a 2 layer PCB have through-hole components?
A2: Yes, a 2 layer PCB can accommodate both surface mount (SMT) and through-hole (THT) components. Through-hole components are inserted into drilled holes on the PCB and soldered on the opposite side, while SMT components are mounted directly on the surface of the PCB.
Q3: What is the maximum number of components that can be placed on a 2 layer PCB?
A3: The maximum number of components that can be placed on a 2 layer PCB depends on several factors, such as the component sizes, spacing requirements, and overall board dimensions. Generally, a 2 layer PCB can accommodate a moderate number of components, but for more complex designs with a higher component count, multi-layer PCBs may be necessary.
Q4: How long does it take to manufacture a 2 layer PCB?
A4: The manufacturing lead time for a 2 layer PCB can vary depending on the PCB fabrication house and the specific requirements of the project. Typically, the lead time ranges from a few days to a couple of weeks. Expedited manufacturing options may be available for urgent projects, but they often come at a higher cost.
Q5: Can a 2 layer PCB be used for high-speed digital circuits?
A5: While 2 layer PCBs can be used for high-speed digital circuits, they may face limitations in terms of signal integrity and power distribution. For high-speed designs, it is important to carefully consider the layout, routing, and impedance control to minimize signal reflections, crosstalk, and electromagnetic interference (EMI). In some cases, multi-layer PCBs with dedicated power and ground planes may be more suitable for high-speed digital applications.
Conclusion
2 layer PCBs are a fundamental building block in the world of electronics. They offer a cost-effective and reliable solution for a wide range of applications, from consumer devices to industrial systems. By understanding the essentials of 2 layer PCB design, manufacturing, and best practices, engineers and designers can create robust and efficient electronic products.
As technology continues to advance, the demand for compact and high-performance electronics will drive the evolution of PCB design and manufacturing techniques. Staying up-to-date with the latest industry trends, design tools, and manufacturing capabilities is crucial for success in the ever-changing landscape of electronics.
Parameter | Value |
---|---|
Number of Layers | 2 |
Common Layer Thickness | 0.8mm – 1.6mm |
Typical Manufacturing Lead Time | Few days to a couple of weeks |
Suitable for High-Speed Digital Circuits | Limited, may require careful design considerations |
Accommodates SMT and THT Components | Yes |
By leveraging the power of 2 layer PCBs and following best design practices, engineers and designers can bring their innovative ideas to life and contribute to the advancement of technology in various industries. Whether you are a beginner or an experienced professional, understanding the essentials of 2 layer PCBs is a valuable skill that will serve you well in your electronic design endeavors.
No responses yet