Introduction
Printed Circuit Board (PCB) assembly is a critical process in the manufacturing of electronic devices. To ensure the quality and reliability of the final product, it is essential to conduct thorough testing at various stages of the assembly process. In this article, we will discuss 13 effective test methods for PCB Assembly, highlighting their importance and application in the industry.
Understanding PCB Testing
PCB testing is a comprehensive process that involves various techniques to verify the functionality, reliability, and durability of the assembled board. The primary objectives of PCB testing are:
1. Identifying manufacturing defects
2. Ensuring proper component placement and soldering
3. Verifying electrical connectivity and signal integrity
4. Checking for potential short circuits or open connections
5. Validating the overall performance of the assembled board
By conducting rigorous testing, manufacturers can minimize the risk of product failures, reduce warranty claims, and maintain customer satisfaction.
PCB Testing Methods
1. Visual Inspection
Visual inspection is the most basic and essential test method in PCB assembly. It involves a manual or automated examination of the assembled board to identify any visible defects or anomalies. Some common issues that can be detected through visual inspection include:
– Incorrect component placement
– Solder bridging or insufficient solder
– Damaged or missing components
– PCB substrate defects (e.g., scratches, cracks, or discoloration)
Visual inspection can be performed using various tools, such as magnifying lenses, microscopes, or automated optical inspection (AOI) systems.
2. Automated Optical Inspection (AOI)
AOI is an advanced form of visual inspection that utilizes high-resolution cameras and image processing software to detect defects on the assembled PCB. The AOI system captures images of the board from multiple angles and compares them against a predefined set of criteria or a golden sample. Any deviations or anomalies are flagged for further investigation.
AOI offers several advantages over manual visual inspection:
– Faster inspection speed
– Higher accuracy and consistency
– Ability to detect subtle defects
– Reduced human error and fatigue
However, AOI systems can be expensive and may require specialized programming and setup.
3. X-Ray Inspection
X-ray inspection is a non-destructive testing method that uses X-rays to examine the internal structure of the assembled PCB. This technique is particularly useful for detecting defects in hidden or obscured areas, such as:
– Ball Grid Array (BGA) solder joints
– Vias and through-hole connections
– Solder voids or insufficient solder
– Component placement and alignment
X-ray inspection systems can provide both 2D and 3D images of the PCB, allowing for a comprehensive analysis of the assembly quality.
4. In-Circuit Testing (ICT)
In-circuit testing is a powerful test method that verifies the functionality of individual components on the assembled PCB. The ICT system uses a bed-of-nails fixture to make electrical contact with specific test points on the board. By applying test signals and measuring the response, the system can detect:
– Incorrect component values
– Open or short circuits
– Faulty or missing components
– Inadequate solder connections
ICT is highly effective in identifying manufacturing defects and ensuring the overall quality of the assembled board.
5. Flying Probe Testing
Flying probe testing is an alternative to ICT that uses movable probes to make electrical contact with test points on the PCB. The probes are controlled by a computer-aided design (CAD) program that guides them to the desired locations. Flying probe testing offers several advantages:
– Flexibility in testing different PCB designs
– No need for custom fixtures
– Ability to test both sides of the board
– Reduced setup time and cost
However, flying probe testing may be slower than ICT and may not be suitable for high-volume production.
6. Boundary Scan Testing
Boundary scan testing, also known as JTAG (Joint Test Action Group) testing, is a method that utilizes built-in test circuitry within the integrated circuits (ICs) on the PCB. The test circuitry allows access to the input and output pins of the ICs, enabling the testing of interconnections and the functionality of the components.
Boundary scan testing offers several benefits:
– Testing of complex, high-density PCBs
– Detection of hidden defects, such as open connections or short circuits
– Verification of the correct operation of ICs
– Reduced test time and cost compared to other methods
To implement boundary scan testing, the PCB design must include JTAG-compliant ICs and the necessary test access ports (TAPs).
7. Functional Testing
Functional testing is a critical test method that verifies the overall performance and functionality of the assembled PCB. This type of testing involves applying input signals to the board and measuring the output response to ensure that it meets the specified requirements. Functional testing can be performed at various levels, such as:
– Component level: Testing individual components or functional blocks
– Board level: Testing the entire assembled PCB
– System level: Testing the PCB as part of a complete system or device
Functional testing typically requires specialized test equipment, such as signal generators, oscilloscopes, and power supplies, as well as custom test software and fixtures.
8. Burn-In Testing
Burn-in testing is a method that subjects the assembled PCB to elevated temperatures and electrical stress for an extended period to identify potential early-life failures. During burn-in testing, the PCB is operated under controlled conditions that exceed its normal operating parameters. This process can reveal latent defects, such as:
– Weak solder joints
– Marginal components
– Temperature-sensitive failures
– Intermittent faults
Burn-in testing is particularly important for PCBs used in critical applications, such as aerospace, medical, or automotive industries, where reliability is paramount.
9. Environmental Testing
Environmental testing evaluates the ability of the assembled PCB to withstand various environmental conditions that it may encounter during its lifecycle. Some common environmental tests include:
– Temperature cycling: Exposing the PCB to alternating high and low temperatures
– Humidity testing: Subjecting the PCB to high humidity levels
– Vibration testing: Applying mechanical vibrations to the PCB
– Shock testing: Subjecting the PCB to sudden, high-acceleration forces
– Salt spray testing: Exposing the PCB to a corrosive salt atmosphere
Environmental testing helps ensure that the PCB can operate reliably in its intended environment and identifies any potential weaknesses in the design or assembly process.
10. Electromagnetic Compatibility (EMC) Testing
EMC testing assesses the ability of the assembled PCB to operate without causing or being affected by electromagnetic interference (EMI). This type of testing is critical for ensuring that the PCB complies with relevant EMC regulations and standards. EMC testing typically involves:
– Radiated emissions testing: Measuring the electromagnetic energy emitted by the PCB
– Conducted emissions testing: Measuring the electromagnetic energy conducted through the power supply and interconnects
– Radiated immunity testing: Evaluating the PCB’s ability to withstand external electromagnetic fields
– Conducted immunity testing: Evaluating the PCB’s ability to withstand electromagnetic disturbances conducted through the power supply and interconnects
EMC testing requires specialized equipment, such as anechoic chambers, spectrum analyzers, and signal generators, as well as expertise in EMC regulations and test methods.
11. Thermal Imaging
Thermal imaging is a non-contact test method that uses infrared cameras to visualize the temperature distribution on the assembled PCB. This technique can help identify potential thermal issues, such as:
– Hot spots caused by component overheating
– Insufficient heat dissipation
– Thermal stress on solder joints
– Uneven temperature distribution across the board
Thermal imaging can be performed during functional testing or under simulated operating conditions to evaluate the thermal performance of the PCB.
12. Continuity Testing
Continuity testing is a basic test method that verifies the electrical continuity between two points on the assembled PCB. This test is typically performed using a multimeter or a continuity tester to check for open circuits or high-resistance connections. Continuity testing is essential for ensuring that all the required electrical connections are present and properly formed.
13. Hipot Testing
Hipot (high potential) testing is a safety test method that applies a high voltage between the conductors on the PCB and the ground to detect any insulation breakdown or leakage currents. This test is particularly important for PCBs used in high-voltage applications or those requiring electrical safety certification. Hipot testing can reveal:
– Insulation defects
– Inadequate clearance or creepage distances
– Potential shock hazards
Hipot testing requires specialized high-voltage test equipment and must be performed by trained personnel following strict safety procedures.
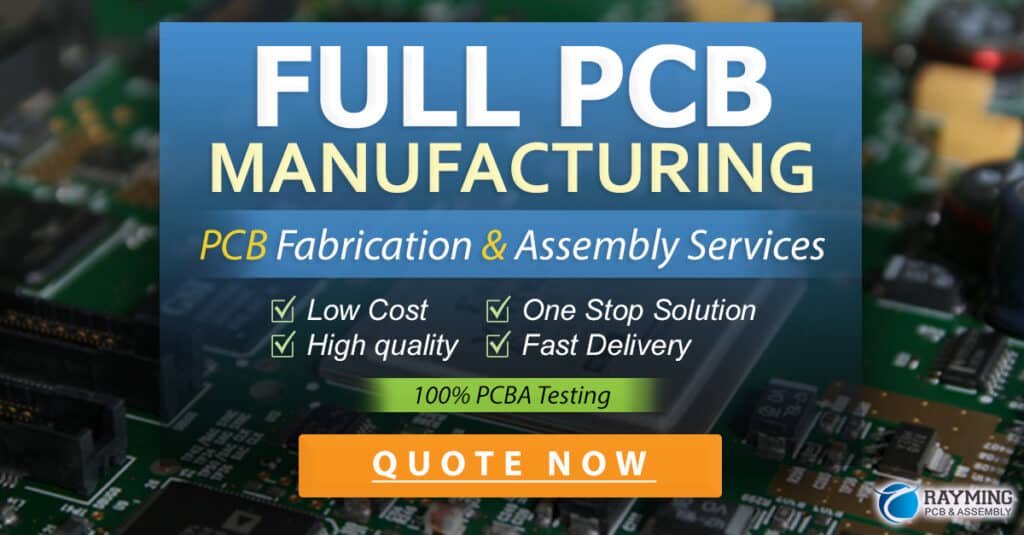
Implementing a Comprehensive PCB Testing Strategy
To ensure the quality and reliability of assembled PCBs, it is essential to implement a comprehensive testing strategy that incorporates multiple test methods. The choice of test methods depends on various factors, such as:
– PCB complexity and design
– Manufacturing process and volume
– End-use application and environment
– Regulatory and customer requirements
– Budget and resource constraints
A typical PCB testing strategy may include a combination of visual inspection, AOI, X-ray inspection, ICT, flying probe testing, functional testing, and environmental testing. By applying these test methods at appropriate stages of the assembly process, manufacturers can identify and address defects early, reducing rework costs and improving overall product quality.
Table: Comparison of PCB Testing Methods
Test Method | Defects Detected | Speed | Flexibility | Cost |
---|---|---|---|---|
Visual Inspection | Visible defects, component placement, solder quality | Slow | High | Low |
Automated Optical Inspection (AOI) | Visible defects, component placement, solder quality | Fast | Moderate | High |
X-Ray Inspection | Internal defects, BGA solder joints, vias | Slow | High | High |
In-Circuit Testing (ICT) | Component functionality, open/short circuits, solder quality | Fast | Low | High |
Flying Probe Testing | Component functionality, open/short circuits, solder quality | Moderate | High | Moderate |
Boundary Scan Testing | Interconnections, IC functionality | Fast | Moderate | Moderate |
Functional Testing | Overall performance and functionality | Slow | High | High |
Burn-In Testing | Early-life failures, latent defects | Slow | Low | High |
Environmental Testing | Reliability under environmental stress | Slow | Moderate | High |
EMC Testing | Electromagnetic compatibility | Slow | Low | High |
Thermal Imaging | Thermal performance, hot spots | Fast | High | Moderate |
Continuity Testing | Open circuits, high-resistance connections | Fast | High | Low |
Hipot Testing | Insulation breakdown, leakage currents | Slow | Low | Moderate |
Frequently Asked Questions (FAQ)
- What is the most important test method for PCB assembly?
-
There is no single most important test method, as each method serves a specific purpose and addresses different types of defects. A comprehensive testing strategy that incorporates multiple methods is essential for ensuring the overall quality and reliability of the assembled PCB.
-
Can all PCB testing be automated?
-
While many test methods, such as AOI, X-ray inspection, and ICT, can be automated, some tests, like visual inspection and functional testing, may require human intervention. Automation can improve test speed and consistency but may not completely replace the need for manual testing.
-
How do I choose the right test methods for my PCB assembly?
-
The choice of test methods depends on factors such as PCB complexity, manufacturing process, end-use application, regulatory requirements, and budget constraints. Consulting with experienced PCB testing professionals and conducting a thorough analysis of your specific needs can help determine the most appropriate test methods for your assembly.
-
What are the consequences of insufficient PCB testing?
-
Insufficient PCB testing can lead to a range of problems, including increased defect rates, higher rework costs, lower product reliability, and potential safety hazards. In some cases, it may also result in non-compliance with regulatory standards and damage to the manufacturer’s reputation.
-
How can I optimize my PCB testing process?
- To optimize your PCB testing process, consider the following:
- Implement a comprehensive testing strategy that covers all critical aspects of the assembly
- Invest in advanced test equipment and software to improve test speed and accuracy
- Regularly review and update your testing procedures to incorporate best practices and new technologies
- Provide adequate training to your testing personnel to ensure consistent and reliable results
- Collaborate with your PCB design and manufacturing teams to identify and address potential issues early in the process
Conclusion
PCB testing is a vital aspect of the assembly process, ensuring the quality, reliability, and functionality of the final product. By implementing a comprehensive testing strategy that incorporates various test methods, manufacturers can identify and address defects early, reduce rework costs, and improve overall product quality. As PCB complexity and performance requirements continue to increase, staying up-to-date with the latest testing technologies and best practices is essential for success in the competitive electronics industry.
No responses yet