Introduction to Immersion Gold Plating
Immersion gold (ENIG) plating is a popular surface finish for printed circuit boards (PCBs) due to its numerous advantages over other finishes. This article will explore 13 key benefits of using immersion gold plating on PCBs, including improved solderability, enhanced durability, and superior electrical performance.
What is Immersion Gold Plating?
Immersion gold plating, also known as Electroless Nickel Immersion Gold (ENIG), is a chemical process that deposits a thin layer of gold over a nickel substrate on the surface of a PCB. The process involves several steps:
- Cleaning the PCB surface
- Applying a layer of electroless nickel
- Applying a thin layer of immersion gold
The resulting finish provides a flat, solderable surface that protects the underlying copper from oxidation and corrosion.
Advantages of Immersion Gold Plating
1. Excellent Solderability
One of the primary advantages of immersion gold plating is its excellent solderability. The gold surface provides a clean, oxide-free surface that allows for easy and reliable soldering of components to the PCB. This is particularly important for surface mount technology (SMT) components, which require precise and consistent solder joints.
2. Enhanced Durability
Immersion gold plating offers enhanced durability compared to other surface finishes. The nickel layer underneath the gold provides a strong, wear-resistant barrier that protects the copper from mechanical damage. Additionally, the gold layer itself is resistant to corrosion and oxidation, ensuring that the PCB remains solderable even after extended storage periods.
3. Superior Electrical Performance
The combination of nickel and gold in immersion gold plating provides superior electrical performance compared to other finishes. The nickel layer acts as a diffusion barrier, preventing the formation of brittle intermetallic compounds that can degrade electrical conductivity. The gold layer, being an excellent conductor, ensures reliable and consistent electrical connections between components and the PCB.
4. Compatibility with Wire Bonding
Immersion gold plating is compatible with wire bonding, a process commonly used in semiconductor packaging. The gold surface provides an ideal substrate for wire bonding, ensuring strong and reliable connections between the PCB and the semiconductor device.
5. Resistance to Corrosion
The gold layer in immersion gold plating is highly resistant to corrosion, even in harsh environmental conditions. This makes ENIG-plated PCBs suitable for use in a wide range of applications, including industrial, automotive, and aerospace electronics.
6. Improved Shelf Life
PCBs with immersion gold plating have an improved shelf life compared to those with other finishes. The gold layer prevents oxidation of the underlying copper, ensuring that the PCB remains solderable even after extended storage periods. This is particularly important for PCBs that may not be assembled immediately after manufacturing.
7. Compatibility with Multiple Soldering Processes
Immersion gold plating is compatible with multiple soldering processes, including reflow soldering, wave soldering, and hand soldering. This versatility makes ENIG-plated PCBs suitable for a wide range of assembly processes and applications.
8. Reduced Risk of Solder Mask Contamination
The electroless nickel layer in immersion gold plating acts as a barrier between the copper and the solder mask, reducing the risk of solder mask contamination. This helps to ensure reliable and consistent solder joints, particularly in fine-pitch applications.
9. Improved Aesthetics
Immersion gold plating provides an attractive, uniform gold finish that enhances the aesthetics of the PCB. This can be particularly important for high-end electronics or consumer products where visual appeal is a key consideration.
10. Compatibility with High-Frequency Applications
The superior electrical performance of immersion gold plating makes it well-suited for high-frequency applications, such as RF and microwave electronics. The nickel layer helps to maintain signal integrity, while the gold layer ensures reliable connections between components and the PCB.
11. Reduced Environmental Impact
Compared to other surface finishes, such as HASL (Hot Air Solder Leveling), immersion gold plating has a reduced environmental impact. The process does not require the use of lead, which is a hazardous substance, and generates less waste compared to other finishing methods.
12. Cost-Effectiveness
While immersion gold plating may have a higher initial cost compared to other finishes, it can be cost-effective in the long run. The enhanced durability, improved solderability, and extended shelf life of ENIG-plated PCBs can help to reduce repair and rework costs, as well as minimize production downtime.
13. Wide Industry Acceptance
Immersion gold plating is widely accepted and used across various industries, including consumer electronics, automotive, aerospace, and medical devices. This wide industry acceptance ensures that ENIG-plated PCBs are readily available from a variety of manufacturers and can be easily integrated into existing production processes.
Immersion Gold Plating vs. Other Surface Finishes
When compared to other common PCB surface finishes, immersion gold plating offers several advantages:
Surface Finish | Solderability | Durability | Shelf Life | Environmental Impact |
---|---|---|---|---|
Immersion Gold (ENIG) | Excellent | High | Extended | Low |
HASL (Hot Air Solder Leveling) | Good | Moderate | Limited | High (lead-based) |
OSP (Organic Solderability Preservative) | Moderate | Low | Short | Low |
Immersion Silver | Good | Moderate | Moderate | Low |
Immersion Tin | Good | Moderate | Moderate | Low |
As shown in the table, immersion gold plating offers the best combination of solderability, durability, shelf life, and environmental impact compared to other surface finishes.
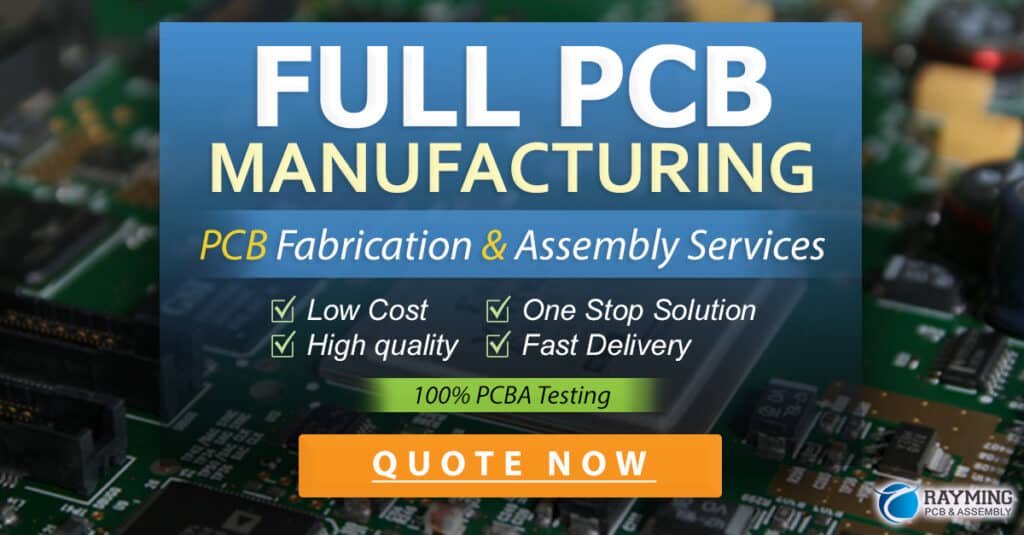
Frequently Asked Questions (FAQ)
-
Q: What is the typical thickness of the gold layer in immersion gold plating?
A: The typical thickness of the gold layer in immersion gold plating ranges from 0.05 to 0.2 microns (2 to 8 microinches). -
Q: Can immersion gold plating be used on flexible PCBs?
A: Yes, immersion gold plating can be used on flexible PCBs, providing the same benefits as on rigid PCBs. -
Q: How does the cost of immersion gold plating compare to other surface finishes?
A: Immersion gold plating typically has a higher initial cost compared to other finishes like HASL or OSP. However, the long-term benefits of ENIG can make it more cost-effective in the long run. -
Q: Is immersion gold plating suitable for high-temperature applications?
A: Yes, immersion gold plating is suitable for high-temperature applications. The nickel layer provides a stable substrate that can withstand elevated temperatures without degrading the electrical or mechanical properties of the PCB. -
Q: Can immersion gold plating be reworked or repaired?
A: Yes, immersion gold plating can be reworked or repaired using standard soldering techniques. However, care must be taken to avoid damaging the underlying nickel layer during the rework process.
Conclusion
Immersion gold plating offers numerous advantages for PCBs, including excellent solderability, enhanced durability, superior electrical performance, and compatibility with multiple soldering processes. These benefits, combined with its wide industry acceptance and reduced environmental impact, make immersion gold plating an attractive choice for a wide range of electronics applications.
When selecting a surface finish for your PCB, consider the specific requirements of your application, such as the expected operating environment, shelf life, and assembly processes. In many cases, immersion gold plating will provide the optimal combination of performance, reliability, and cost-effectiveness.
As the electronics industry continues to evolve, with increasingly complex and demanding applications, immersion gold plating is likely to remain a popular choice for PCB surface finishing. Its proven track record, combined with ongoing advancements in materials and processes, ensures that ENIG will continue to play a vital role in the production of high-quality, reliable electronic devices.
No responses yet