Introduction to PCB Stack-up
Printed Circuit Boards (PCBs) are essential components in modern electronic devices. They provide a platform for mounting and interconnecting various electronic components, such as integrated circuits, resistors, capacitors, and connectors. As electronic designs become more complex and demand higher performance, the need for multi-layer PCBs has grown significantly. In this article, we will focus on the 12 layer PCB stack-up and its associated thickness considerations.
What is a PCB Stack-Up?
A PCB stack-up refers to the arrangement of copper layers and insulating materials that make up a printed circuit board. It defines the number of layers, their order, and the thickness of each layer. The stack-up also specifies the type of material used for the insulating layers, known as the substrate or dielectric.
Importance of PCB Stack-Up Design
The stack-up design plays a crucial role in determining the performance, reliability, and manufacturability of a PCB. It affects signal integrity, power distribution, electromagnetic compatibility (EMC), and thermal management. A well-designed stack-up ensures that the PCB meets the electrical and mechanical requirements of the intended application while minimizing manufacturing costs and complexities.
12 Layer PCB Stack-Up
A 12 layer PCB is a complex multilayer board that offers a high degree of functionality and flexibility for advanced electronic systems. It consists of 12 conductive layers separated by insulating layers. The arrangement of these layers depends on the specific design requirements, such as signal integrity, power distribution, and routing density.
Typical 12 Layer PCB Stack-Up Arrangement
Here is a common stack-up arrangement for a 12 layer PCB:
Layer | Layer Name | Material | Thickness (mm) |
---|---|---|---|
1 | Top Layer | Copper | 0.035 |
2 | Ground Plane | Copper | 0.035 |
3 | Signal Layer 1 | Copper | 0.018 |
4 | Signal Layer 2 | Copper | 0.018 |
5 | Power Plane | Copper | 0.035 |
6 | Signal Layer 3 | Copper | 0.018 |
7 | Signal Layer 4 | Copper | 0.018 |
8 | Ground Plane | Copper | 0.035 |
9 | Signal Layer 5 | Copper | 0.018 |
10 | Signal Layer 6 | Copper | 0.018 |
11 | Power Plane | Copper | 0.035 |
12 | Bottom Layer | Copper | 0.035 |
Dielectric Layers | FR-4 | 0.2 (each) |
In this arrangement, the top and bottom layers are used for component placement and external connections. The inner layers are divided into signal layers, ground planes, and power planes. The signal layers are used for routing signals between components, while the ground and power planes provide stable reference voltages and distribute power throughout the board.
Signal Integrity Considerations
Signal integrity is a critical aspect of high-speed PCB design. It refers to the ability of a signal to maintain its intended characteristics as it propagates through the board. In a 12 layer PCB, signal integrity is influenced by factors such as trace width, trace spacing, dielectric material, and the presence of ground and power planes.
To ensure good signal integrity, designers must carefully choose the dielectric material and its thickness. FR-4 is a commonly used dielectric material known for its good electrical and mechanical properties. The thickness of the dielectric layers affects the characteristic impedance of the traces, which should be controlled to match the impedance of the connected components.
Ground and power planes play a vital role in maintaining signal integrity. They provide a low-impedance return path for high-speed signals and help reduce crosstalk between adjacent traces. By strategically placing ground and power planes near signal layers, designers can minimize electromagnetic interference (EMI) and ensure clean signal transmission.
Power Distribution Network (PDN)
The power distribution network (PDN) is responsible for delivering stable and clean power to all the components on the PCB. In a 12 layer PCB, dedicated power planes are used to distribute power efficiently. The number and placement of power planes depend on the power requirements of the components and the desired noise performance.
Designers must consider the current carrying capacity of the power planes and ensure that they are thick enough to handle the required current without excessive voltage drop or thermal issues. The use of multiple power planes helps reduce the impedance of the PDN and provides a low-inductance path for high-frequency currents.
Decoupling capacitors are essential components in the PDN. They are placed close to the power pins of integrated circuits to provide a local reservoir of charge and suppress high-frequency noise. The placement and selection of decoupling capacitors should be carefully considered to ensure effective power distribution and noise suppression.
Thermal Management
Thermal management is another crucial aspect of 12 layer PCB design. As the number of layers increases, so does the potential for heat generation and thermal challenges. The high component density and increased power consumption in complex designs can lead to temperature rise, which can impact the reliability and performance of the PCB.
To mitigate thermal issues, designers can incorporate thermal management techniques into the stack-up. This includes the use of thermal vias, which are dedicated vias that transfer heat from the components to the outer layers or dedicated heatsinks. The placement of thermal vias near high-power components helps dissipate heat efficiently.
The choice of dielectric material also affects thermal management. Some high-performance dielectric materials, such as polyimide or ceramic-filled laminates, offer better thermal conductivity compared to standard FR-4. These materials help spread heat more effectively and reduce thermal hotspots on the board.
PCB Thickness Considerations
The thickness of a 12 layer PCB is an important consideration that affects its mechanical stability, manufacturing process, and overall cost. The thickness is determined by the number of layers, the thickness of each layer, and the thickness of the dielectric materials used.
Typical Thickness of a 12 Layer PCB
The typical thickness of a 12 layer PCB can range from 1.6mm to 2.4mm, depending on the specific requirements of the design. The thickness of each copper layer is usually around 0.035mm (1 oz. copper), while the thickness of the dielectric layers can vary based on the chosen material and the desired electrical properties.
Here’s an example of how the thickness of a 12 layer PCB can be calculated:
Layer | Thickness (mm) |
---|---|
Copper Layers | 0.420 (12 * 0.035) |
Dielectric Layers | 2.200 (11 * 0.2) |
Total Thickness | 2.620 |
In this example, the total thickness of the 12 layer PCB is approximately 2.6mm, assuming a copper thickness of 0.035mm and a dielectric thickness of 0.2mm between each layer.
Manufacturing Considerations
The thickness of a 12 layer PCB has implications for the manufacturing process. Thicker boards require special handling and may have longer manufacturing times compared to thinner boards. The drilling of vias becomes more challenging as the thickness increases, and the aspect ratio of the vias (the ratio of depth to diameter) should be carefully considered to ensure reliable plating and connectivity.
Additionally, thicker boards may be more susceptible to warping and bowing during the manufacturing process, especially if there are uneven copper distributions or significant temperature gradients. Proper design techniques, such as balanced copper distribution and the use of symmetrical stack-ups, can help minimize these issues.
Cost Implications
The cost of a 12 layer PCB is generally higher compared to boards with fewer layers. The increased complexity, material usage, and manufacturing challenges contribute to the higher cost. However, the cost should be balanced against the benefits of using a 12 layer PCB, such as improved functionality, better signal integrity, and reduced overall system size.
Designers should consider the cost implications early in the design process and optimize the stack-up to achieve the required performance while minimizing unnecessary layers and materials. Working closely with the PCB manufacturer and understanding their capabilities and constraints can help optimize the design for cost-effective manufacturing.
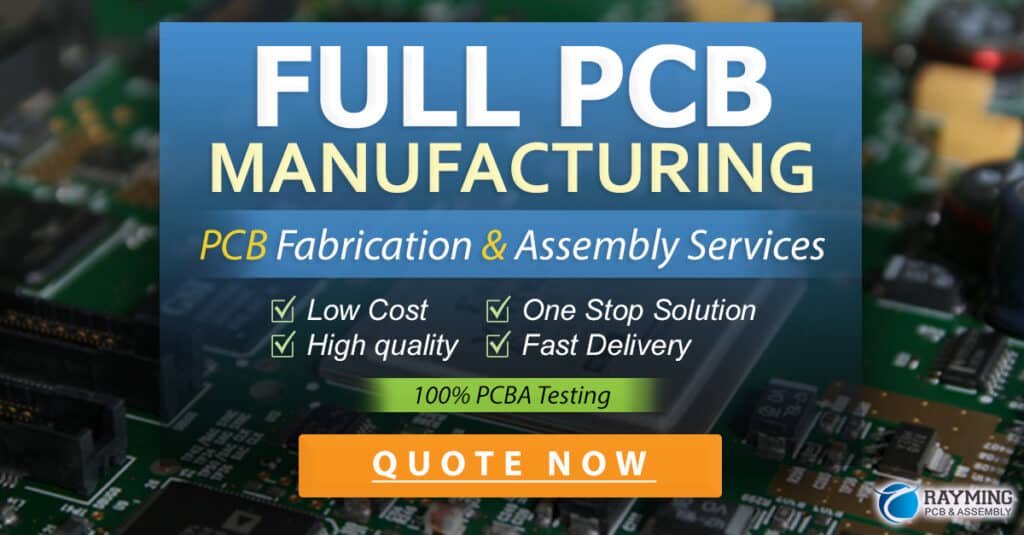
Frequently Asked Questions (FAQ)
-
Q: What is the purpose of using a 12 layer PCB?
A: A 12 layer PCB is used when the design requires a high degree of functionality, signal integrity, and routing density. It allows for the integration of complex circuitry, multiple power planes, and dedicated signal layers, making it suitable for advanced electronic systems. -
Q: How does the number of layers affect the cost of a PCB?
A: Generally, the cost of a PCB increases with the number of layers. A 12 layer PCB is more expensive compared to boards with fewer layers due to the increased complexity, material usage, and manufacturing challenges. However, the cost should be balanced against the benefits and requirements of the specific application. -
Q: What is the typical thickness of a 12 layer PCB?
A: The typical thickness of a 12 layer PCB can range from 1.6mm to 2.4mm, depending on the specific design requirements. The thickness is determined by the number of layers, the thickness of each copper layer (usually 0.035mm or 1 oz. copper), and the thickness of the dielectric materials used between the layers. -
Q: What are the signal integrity considerations in a 12 layer PCB?
A: Signal integrity is a critical aspect of 12 layer PCB design. To ensure good signal integrity, designers must carefully choose the dielectric material and its thickness, control the characteristic impedance of traces, and strategically place ground and power planes to minimize electromagnetic interference (EMI) and crosstalk between adjacent traces. -
Q: How does thermal management affect the design of a 12 layer PCB?
A: Thermal management is crucial in 12 layer PCB design due to the high component density and increased power consumption. Designers can incorporate thermal management techniques such as the use of thermal vias, selection of high-performance dielectric materials with better thermal conductivity, and proper placement of components to dissipate heat effectively and avoid thermal hotspots on the board.
Conclusion
The 12 layer PCB stack-up and thickness are critical aspects of advanced electronic design. Understanding the arrangement of layers, the importance of signal integrity, power distribution, and thermal management is essential for designing high-performance and reliable PCBs. By carefully considering the stack-up, dielectric materials, and manufacturing constraints, designers can optimize their 12 layer PCB designs to meet the specific requirements of their applications while balancing cost and performance. As electronic systems continue to evolve and demand higher functionality, the use of 12 layer PCBs will remain prevalent in industries such as telecommunications, aerospace, defense, and high-performance computing.
No responses yet