Introduction
When it comes to protecting printed circuit boards (PCBs) from harsh environments, conformal coatings are a popular choice. PCB Conformal Coating is a thin protective film that is applied to the surface of a PCB to shield it from moisture, dust, chemicals, and other contaminants. Choosing the right conformal coating for your PCB is crucial to ensure optimal performance and longevity. In this article, we will provide you with 12 guides to help you select the most suitable PCB conformal coating for your application.
What is PCB Conformal Coating?
PCB conformal coating is a protective layer that conforms to the contours of a PCB, covering the components and exposed surfaces. It acts as a barrier against environmental factors that can damage or degrade the performance of the PCB over time. Conformal coatings are typically applied as a liquid and then cured to form a solid, durable film.
Benefits of PCB Conformal Coating
- Protection against moisture, humidity, and corrosion
- Insulation against electrical interference and short circuits
- Resistance to chemicals, solvents, and other harsh substances
- Improved mechanical strength and durability
- Enhanced thermal and UV stability
Types of PCB Conformal Coatings
There are several types of conformal coatings available, each with its own unique properties and advantages. Here are the most common types of PCB conformal coatings:
1. Acrylic Resin (AR)
Acrylic resin coatings are known for their excellent clarity, fast drying time, and ease of application. They provide good moisture and fungal resistance but have limited chemical resistance.
2. Silicone Resin (SR)
Silicone resin coatings offer excellent thermal stability, flexibility, and moisture resistance. They are ideal for high-temperature applications but can be difficult to remove for repairs.
3. Polyurethane (UR)
Polyurethane coatings provide excellent abrasion and chemical resistance. They have good dielectric properties and are suitable for harsh environments. However, they may require a primer for better adhesion.
4. Epoxy (ER)
Epoxy coatings are known for their superior chemical and abrasion resistance. They have excellent adhesion properties and provide good thermal stability. Epoxy coatings are often used in high-reliability applications.
5. Parylene (XY)
Parylene coatings are ultra-thin, pinhole-free, and highly conformal. They offer excellent dielectric properties, chemical resistance, and biocompatibility. Parylene coatings are applied through a vapor deposition process and are suitable for sensitive applications.
Coating Type | Moisture Resistance | Chemical Resistance | Thermal Stability | Ease of Application | Reworkability |
---|---|---|---|---|---|
Acrylic | Good | Limited | Moderate | Easy | Easy |
Silicone | Excellent | Good | Excellent | Moderate | Difficult |
Polyurethane | Good | Excellent | Good | Moderate | Moderate |
Epoxy | Good | Excellent | Excellent | Moderate | Difficult |
Parylene | Excellent | Excellent | Good | Difficult | Difficult |
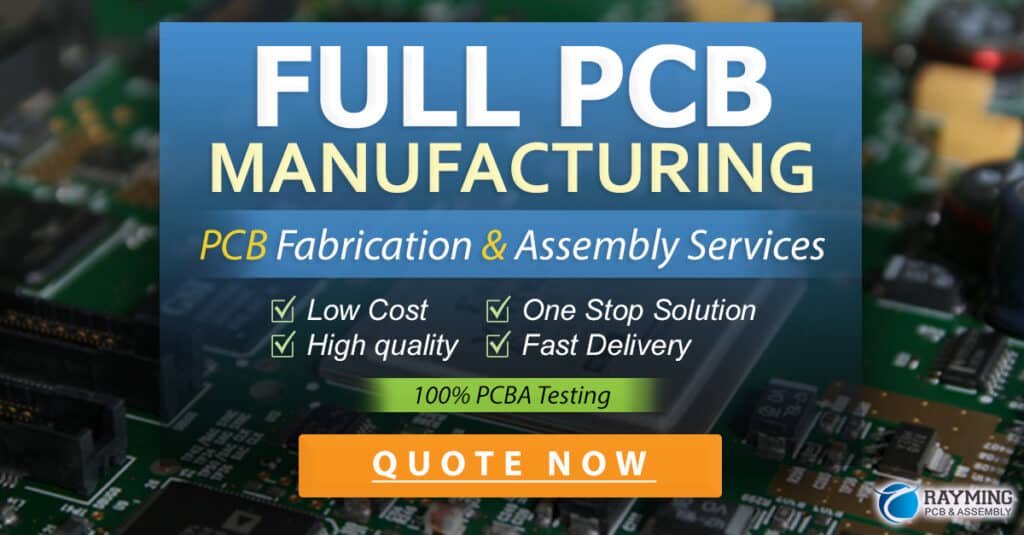
Factors to Consider When Choosing a PCB Conformal Coating
When selecting a conformal coating for your PCB, there are several key factors to consider:
1. Environmental Conditions
Consider the environmental conditions your PCB will be exposed to, such as temperature, humidity, chemicals, and mechanical stress. Choose a coating that can withstand these conditions and provide adequate protection.
2. Dielectric Properties
Evaluate the dielectric properties of the coating, such as dielectric strength, insulation resistance, and dissipation factor. Ensure that the coating can provide sufficient electrical insulation for your application.
3. Thickness and Coverage
Determine the required coating thickness and coverage for your PCB. Some coatings may require multiple layers to achieve the desired protection, while others can provide adequate coverage in a single layer.
4. Curing and Drying Time
Consider the curing and drying time of the coating, as this can affect your production schedule. Some coatings may require longer curing times or specific curing conditions, such as UV or thermal curing.
5. Reworkability and Repairability
Assess the ease of reworking or repairing the coated PCB. Some coatings, such as silicone and epoxy, can be difficult to remove for repairs, while others, like acrylic, are more easily reworkable.
6. Compatibility with Components
Ensure that the coating is compatible with the components on your PCB. Some coatings may interact with certain materials or cause issues with component functionality.
7. Application Method
Consider the application method for the coating, such as spray, dip, or brush coating. Each method has its own advantages and limitations, and the choice may depend on your PCB design and production setup.
8. Cost and Availability
Evaluate the cost and availability of the coating, as well as any associated equipment or materials required for application. Consider the long-term cost-effectiveness of the coating in relation to the protection it provides.
PCB Conformal Coating Application Process
The application process for PCB conformal coating typically involves the following steps:
- Clean the PCB to remove any contaminants or residues.
- Mask any areas that should not be coated, such as connectors or test points.
- Apply the coating using the chosen method (spray, dip, brush, etc.).
- Allow the coating to cure or dry according to the manufacturer’s instructions.
- Inspect the coated PCB for any defects or inconsistencies.
- Remove any masking materials and perform final testing.
Common PCB Conformal Coating Defects
During the application process, several defects may occur that can affect the performance of the coating. Here are some common PCB conformal coating defects to watch out for:
- Pinholes or voids in the coating
- Uneven or inconsistent coverage
- Bubbles or blisters in the coating
- Cracks or delamination
- Contamination or foreign particles in the coating
To minimize the occurrence of these defects, it is essential to follow proper application procedures, maintain a clean working environment, and perform regular inspections and quality control checks.
Testing and Qualification of PCB Conformal Coatings
After applying the conformal coating, it is crucial to test and qualify the coated PCB to ensure that it meets the required performance and reliability standards. Some common tests for PCB conformal coatings include:
- Adhesion testing
- Dielectric strength testing
- Insulation resistance testing
- Thermal cycling and shock testing
- Humidity and salt spray testing
- Chemical resistance testing
These tests help to validate the effectiveness of the coating and identify any potential issues or weaknesses that may affect the long-term performance of the PCB.
Maintenance and Repair of Coated PCBs
Even with the protection provided by conformal coatings, PCBs may still require maintenance or repair over their lifetime. When working with coated PCBs, consider the following:
- Use appropriate solvents or strippers to remove the coating for repairs.
- Take care not to damage the PCB or components during the removal process.
- Reapply the coating after repairs, ensuring proper coverage and adhesion.
- Follow the manufacturer’s guidelines for handling and storing coated PCBs.
FAQ
1. How do I choose the right thickness for my PCB conformal coating?
The thickness of the conformal coating depends on the level of protection required and the specific application. Generally, a thickness of 25-75 microns is sufficient for most applications. Consult with the coating manufacturer or a qualified expert to determine the optimal thickness for your PCB.
2. Can I apply multiple types of conformal coatings to the same PCB?
While it is possible to apply multiple types of coatings to the same PCB, it is generally not recommended. Different coatings may have different properties and curing requirements, which can lead to compatibility issues or reduced effectiveness. It is best to choose a single coating that meets all of your requirements.
3. How do I remove conformal coating for PCB repairs?
To remove conformal coating for repairs, use an appropriate solvent or stripper that is compatible with the coating material. Apply the solvent carefully to the area that needs to be removed, and use a soft brush or swab to gently remove the coating. Be cautious not to damage the PCB or components during the removal process.
4. Can I apply conformal coating selectively to specific areas of the PCB?
Yes, selective coating is possible using masking techniques or specialized application equipment. This allows you to protect critical areas of the PCB while leaving other areas uncoated for connectors, test points, or other purposes.
5. How often should I inspect and test my coated PCBs?
The frequency of inspection and testing depends on the specific application and the environment in which the PCB operates. As a general guideline, it is recommended to perform visual inspections and basic functionality tests on a regular basis, such as every 6-12 months. More comprehensive testing, such as environmental or durability tests, can be conducted less frequently or as required by industry standards or customer specifications.
Conclusion
Choosing the right PCB conformal coating is essential for protecting your PCBs from environmental factors and ensuring reliable performance. By considering the factors discussed in this article, such as environmental conditions, dielectric properties, thickness, curing time, reworkability, compatibility, application method, and cost, you can make an informed decision when selecting a conformal coating for your PCB.
Remember to follow proper application procedures, test and qualify the coated PCBs, and perform regular maintenance and inspections to ensure the long-term effectiveness of the coating. By taking these steps, you can maximize the protection and durability of your PCBs, ultimately leading to improved product reliability and customer satisfaction.
No responses yet