Introduction to PCB Tools
PCB (Printed Circuit Board) tools are essential for designing, programming, and testing electronic circuits. These tools help engineers and technicians create high-quality PCBs that meet the required specifications and performance standards. In this article, we will explore 11 crucial aspects of PCB programming and testing tools that every electronics enthusiast should know.
1. PCB Design Software
1.1. CAD Tools
Computer-Aided Design (CAD) tools are the foundation of PCB design. These software packages allow designers to create schematic diagrams, component layouts, and circuit board layouts. Popular CAD tools include:
– Altium Designer
– KiCad
– Eagle
– OrCAD
1.2. Simulation Tools
Simulation tools help designers test and optimize their PCB designs before fabrication. These tools can simulate various aspects of the circuit, such as signal integrity, power distribution, and electromagnetic compatibility. Some commonly used simulation tools are:
– LTspice
– PSpice
– Ansys HFSS
– Keysight ADS
2. PCB Fabrication Techniques
2.1. Traditional Etching
Traditional etching is a subtractive process that involves removing unwanted copper from a pre-laminated board. The process includes the following steps:
1. Applying a photoresist layer to the copper-clad board
2. Exposing the photoresist to UV light through a photo mask
3. Developing the photoresist to remove the exposed areas
4. Etching away the unwanted copper using a chemical solution
5. Removing the remaining photoresist
2.2. CNC Milling
CNC (Computer Numerical Control) milling is a subtractive process that uses a computer-controlled mill to remove unwanted copper from a PCB. This method is particularly useful for creating prototypes and small-batch productions. The advantages of CNC milling include:
– Faster turnaround times
– Ability to create complex shapes and cutouts
– No need for photo masks or chemicals
2.3. 3D Printing
3D printing is an additive manufacturing process that builds up the PCB layer by layer. This technique allows for the creation of complex 3D structures and embedded components. Some benefits of 3D printing PCBs include:
– Rapid prototyping
– Reduced waste
– Ability to create unique form factors
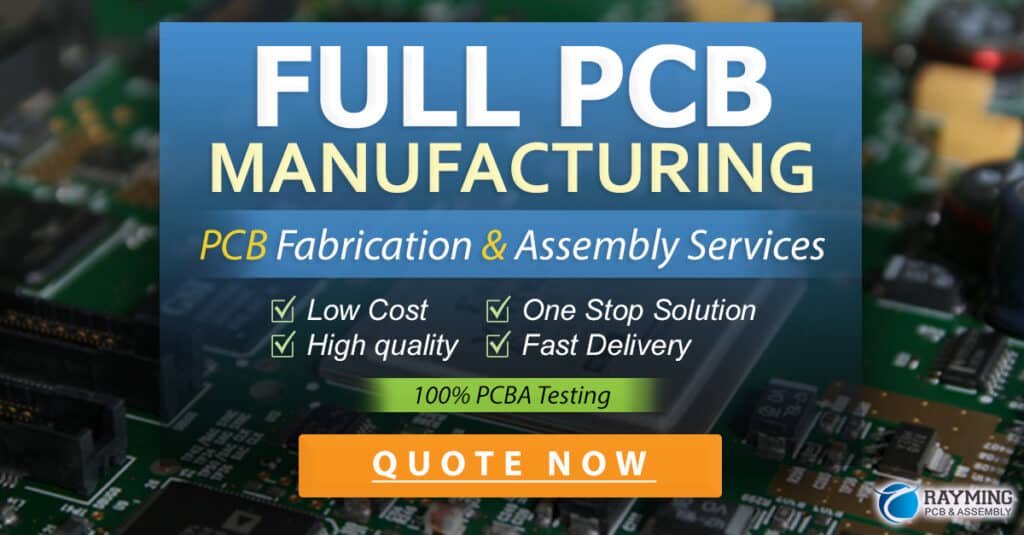
3. PCB Assembly Methods
3.1. Through-Hole Assembly
Through-hole assembly involves inserting component leads through drilled holes in the PCB and soldering them on the opposite side. This method is reliable and suitable for larger components, but it is slower and more labor-intensive than surface-mount assembly.
3.2. Surface-Mount Assembly
Surface-mount assembly involves placing components directly onto the PCB’s surface and soldering them in place. This method allows for smaller component sizes, higher component density, and faster assembly times compared to through-hole assembly.
3.3. Mixed Assembly
Mixed assembly combines both through-hole and surface-mount components on a single PCB. This approach is often used when certain components are not available in surface-mount packages or when additional mechanical strength is required.
4. Soldering Techniques
4.1. Hand Soldering
Hand soldering is a manual process that uses a soldering iron to melt solder and create electrical connections between components and the PCB. This method is suitable for small-scale projects, repairs, and prototypes.
4.2. Reflow Soldering
Reflow soldering is an automated process that involves applying solder paste to the PCB, placing components, and then heating the entire assembly in a reflow oven. The heat melts the solder, creating electrical connections between the components and the PCB. Reflow soldering is ideal for surface-mount components and large-scale production.
4.3. Wave Soldering
Wave soldering is an automated process that is primarily used for through-hole components. The PCB is passed over a molten solder wave, which creates electrical connections between the component leads and the PCB. Wave soldering is faster than hand soldering but requires more setup time and equipment.
5. PCB Inspection Methods
5.1. Visual Inspection
Visual inspection involves examining the PCB for defects, such as solder bridges, cold solder joints, and component misalignment, using the naked eye or magnification tools. This method is simple and quick but may not catch all defects.
5.2. Automated Optical Inspection (AOI)
AOI uses computer vision and image processing algorithms to detect PCB defects. The system compares the PCB images to a reference image and identifies any discrepancies. AOI is faster and more accurate than visual inspection but requires specialized equipment and software.
5.3. X-Ray Inspection
X-ray inspection uses X-rays to create images of the PCB’s internal structure, allowing for the detection of defects that are not visible on the surface, such as voids in solder joints and component placement issues. This method is particularly useful for inspecting high-density PCBs and ball grid array (BGA) packages.
6. PCB Testing Tools
6.1. Multimeters
Multimeters are essential tools for measuring voltage, current, and resistance in PCBs. They help troubleshoot and verify the proper functioning of circuits. Multimeters come in two main types:
– Analog multimeters: These have a moving needle display and are suitable for general-purpose measurements.
– Digital multimeters: These have a digital display and offer higher accuracy and additional features, such as capacitance and frequency measurements.
6.2. Oscilloscopes
Oscilloscopes are used to visualize and measure time-varying signals in PCBs. They display voltage waveforms as a function of time, allowing engineers to analyze signal integrity, timing, and noise issues. Oscilloscopes can be:
– Analog oscilloscopes: These use a cathode-ray tube (CRT) to display waveforms and are suitable for low-frequency signals.
– Digital oscilloscopes: These use digital signal processing and LCD or LED displays, offering higher bandwidth, storage capabilities, and advanced triggering options.
6.3. Logic Analyzers
Logic analyzers are used to capture and display digital signals in PCBs. They help diagnose issues in digital systems by monitoring multiple signals simultaneously and providing timing diagrams and state listings. Logic analyzers are particularly useful for debugging complex digital circuits, such as microprocessor-based systems.
7. PCB Programming Tools
7.1. In-System Programming (ISP)
ISP allows for the programming of microcontrollers and other programmable devices directly on the PCB, without the need for removal. This method uses a programming interface, such as JTAG or SPI, to communicate with the target device. ISP is convenient for firmware updates and debugging.
7.2. Universal Programmers
Universal programmers are standalone devices that can program a wide range of devices, including microcontrollers, EEPROMs, and flash memories. They offer more flexibility than ISP but require the removal of the target device from the PCB.
7.3. Debugging Interfaces
Debugging interfaces, such as JTAG and SWD, provide access to the internal registers and memory of microcontrollers and other programmable devices. They allow for real-time debugging, breakpoint setting, and variable inspection, making it easier to identify and fix firmware issues.
8. PCB Design Considerations
8.1. Component Placement
Proper component placement is crucial for ensuring the optimal performance and manufacturability of a PCB. Designers should consider factors such as:
– Signal integrity: Place components to minimize signal path lengths and crosstalk.
– Thermal management: Position heat-generating components away from sensitive devices and provide adequate cooling.
– Manufacturing constraints: Ensure adequate spacing between components for soldering and inspection.
8.2. Power Distribution
Efficient power distribution is essential for maintaining signal integrity and preventing voltage drops in PCBs. Designers should:
– Use appropriate trace widths and copper thicknesses for power traces.
– Implement proper power and ground planes to minimize impedance and provide shielding.
– Decouple power supplies using bypass capacitors near power-consuming components.
8.3. Signal Integrity
Signal integrity refers to the quality of electrical signals in a PCB. To maintain good signal integrity, designers should:
– Use controlled impedance traces for high-speed signals.
– Minimize crosstalk by providing adequate spacing between signal traces and using guard traces or ground planes.
– Terminate transmission lines properly to prevent reflections and ringing.
9. PCB Manufacturing Files
9.1. Gerber Files
Gerber files are the industry standard for describing PCB layouts. They contain information about the copper layers, solder mask, silkscreen, and drilling data. Gerber files are generated by CAD tools and are used by PCB manufacturers to fabricate the boards.
9.2. Drill Files
Drill files contain information about the location, size, and type of holes to be drilled in the PCB. They are typically provided in Excellon format and are used in conjunction with Gerber files to manufacture the PCB.
9.3. Bill of Materials (BOM)
The BOM is a list of all the components used in the PCB, including their reference designators, part numbers, and quantities. It is essential for procurement and assembly purposes and should be kept up-to-date throughout the design process.
10. PCB Design for Manufacturing (DFM)
10.1. Design Rules
Design rules are guidelines that ensure the manufacturability and reliability of PCBs. They specify parameters such as minimum trace widths, clearances, and hole sizes. Adhering to design rules helps avoid manufacturing issues and reduces the risk of defects.
10.2. Panelization
Panelization is the process of arranging multiple PCBs on a single panel for manufacturing efficiency. It allows for better utilization of materials and reduces handling time. Designers should consider panelization requirements, such as panel size and spacing between boards, when creating the PCB layout.
10.3. Testability
Designing for testability involves incorporating features that facilitate PCB testing and debugging. This includes providing test points, using boundary scan devices, and designing for automated optical inspection (AOI) compatibility. Improved testability reduces manufacturing costs and improves product quality.
11. PCB Design Collaboration
11.1. Version Control
Version control systems, such as Git and SVN, help manage changes to PCB design files and facilitate collaboration among team members. They allow for tracking revisions, branching, and merging of design changes, ensuring a consistent and organized workflow.
11.2. Design Reviews
Design reviews are formal meetings where stakeholders evaluate the PCB design for functionality, manufacturability, and compliance with requirements. They help identify and address issues early in the design process, reducing the risk of costly mistakes and delays.
11.3. Documentation
Proper documentation is essential for communicating design intent, manufacturing requirements, and maintenance procedures. Key documents include:
– Schematic diagrams: Provide a graphical representation of the circuit’s electrical connections and components.
– Assembly drawings: Show the physical placement of components on the PCB and include assembly instructions.
– Fabrication drawings: Detail the PCB’s physical dimensions, layer stackup, and manufacturing specifications.
Frequently Asked Questions (FAQ)
-
What is the difference between through-hole and surface-mount assembly?
Through-hole assembly involves inserting component leads through drilled holes in the PCB and soldering them on the opposite side, while surface-mount assembly involves placing components directly onto the PCB’s surface and soldering them in place. Surface-mount assembly allows for smaller component sizes, higher component density, and faster assembly times compared to through-hole assembly. -
What is the purpose of a bill of materials (BOM) in PCB design?
A bill of materials (BOM) is a list of all the components used in the PCB, including their reference designators, part numbers, and quantities. It is essential for procurement and assembly purposes and should be kept up-to-date throughout the design process. -
What are design rules in PCB design?
Design rules are guidelines that ensure the manufacturability and reliability of PCBs. They specify parameters such as minimum trace widths, clearances, and hole sizes. Adhering to design rules helps avoid manufacturing issues and reduces the risk of defects. -
What is the difference between analog and digital oscilloscopes?
Analog oscilloscopes use a cathode-ray tube (CRT) to display waveforms and are suitable for low-frequency signals, while digital oscilloscopes use digital signal processing and LCD or LED displays, offering higher bandwidth, storage capabilities, and advanced triggering options. -
Why is version control important in PCB design collaboration?
Version control systems, such as Git and SVN, help manage changes to PCB design files and facilitate collaboration among team members. They allow for tracking revisions, branching, and merging of design changes, ensuring a consistent and organized workflow. This helps reduce the risk of errors and miscommunication during the design process.
Conclusion
PCB programming and testing tools are essential for creating high-quality, reliable electronic products. Understanding the various aspects of PCB design, fabrication, assembly, and testing is crucial for engineers and technicians working in the electronics industry. By familiarizing themselves with the 11 key areas discussed in this article, including PCB design software, manufacturing techniques, testing tools, and design considerations, professionals can optimize their PCB development processes and ensure the success of their projects.
No responses yet