Introduction to HDI Materials
High Density Interconnect (HDI) materials are essential components in the production of advanced electronic devices. These materials enable the creation of compact, high-performance printed circuit boards (PCBs) that are crucial for modern consumer electronics, aerospace, and medical applications. As technology continues to advance, it is important to stay informed about the latest HDI materials and their properties. In this article, we will explore 11 essential HDI materials that you need to know.
1. Copper Foil
1.1 What is Copper Foil?
Copper foil is a thin layer of copper that is used as the conductive material in PCBs. It is laminated onto the dielectric substrate and etched to create the desired circuit pattern. Copper foil is available in various thicknesses, typically ranging from 9 to 70 microns (µm).
1.2 Types of Copper Foil
There are two main types of copper foil used in HDI materials:
- Electrodeposited (ED) copper foil
- Rolled annealed (RA) copper foil
ED copper foil is produced by electroplating copper onto a rotating drum, while RA copper foil is manufactured by rolling and annealing copper ingots. ED copper foil is more commonly used in HDI applications due to its better surface quality and improved adhesion to the dielectric substrate.
1.3 Copper Foil Properties
Property | Value |
---|---|
Electrical Conductivity | 5.8 × 10^7 S/m |
Thermal Conductivity | 401 W/(m·K) |
Coefficient of Thermal Expansion (CTE) | 17 ppm/°C |
Tensile Strength | 220-300 MPa |
Elongation | 10-20% |
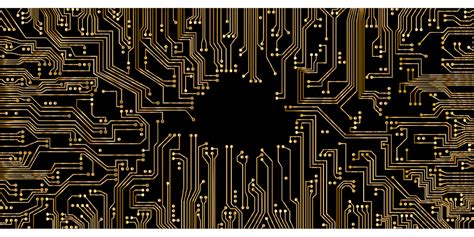
2. Dielectric Substrates
2.1 What are Dielectric Substrates?
Dielectric substrates are the insulating materials used in PCBs to support and separate the conductive layers. They provide electrical isolation, mechanical stability, and heat dissipation. The choice of dielectric substrate depends on the specific application requirements, such as signal speed, frequency, and environmental conditions.
2.2 Common Dielectric Substrates
Some common dielectric substrates used in HDI materials include:
- FR-4
- Polyimide
- Teflon
- Ceramic
FR-4 is the most widely used dielectric substrate due to its good mechanical properties, thermal stability, and low cost. Polyimide is preferred for flexible PCBs, while Teflon and ceramic substrates are used in high-frequency and high-temperature applications, respectively.
2.3 Dielectric Substrate Properties
Substrate | Dielectric Constant | Dissipation Factor | Tg (°C) | CTE (ppm/°C) |
---|---|---|---|---|
FR-4 | 4.2-4.5 | 0.02 | 130-140 | 14-16 |
Polyimide | 3.2-3.5 | 0.002-0.008 | 260-320 | 20-40 |
Teflon | 2.0-2.1 | 0.0002-0.0007 | 327 | 100-120 |
Ceramic | 6-10 | 0.001-0.005 | >1000 | 6-8 |
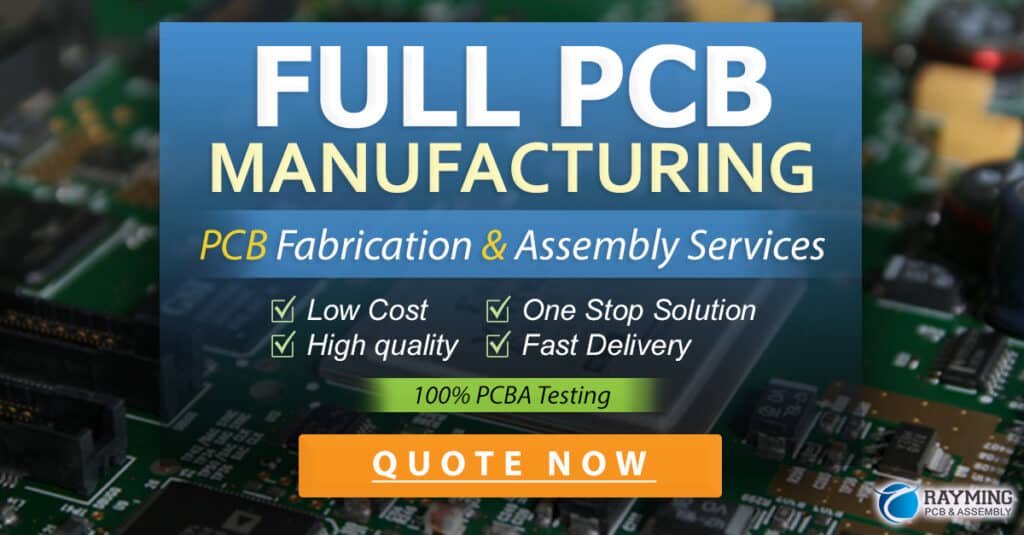
3. Solder Mask
3.1 What is Solder Mask?
Solder mask, also known as solder resist, is a thin polymer layer applied to the outer surfaces of a PCB. Its primary function is to protect the copper traces from oxidation, prevent solder bridges, and provide electrical insulation. Solder mask also helps to define the exposed copper areas for component soldering.
3.2 Types of Solder Mask
There are two main types of solder mask used in HDI materials:
- Liquid photoimageable solder mask (LPISM)
- Dry film solder mask (DFSM)
LPISM is applied as a liquid and then exposed to UV light through a photomask to create the desired pattern. DFSM is a solid film that is laminated onto the PCB surface and then exposed and developed to form the solder mask pattern. LPISM is more commonly used in HDI applications due to its better resolution and adhesion properties.
3.3 Solder Mask Properties
Property | Value |
---|---|
Dielectric Strength | >500 V/mil |
Insulation Resistance | >10^12 Ω |
Pencil Hardness | >6H |
Adhesion | >4B |
Flammability | UL 94 V-0 |

4. Prepregs
4.1 What are Prepregs?
Prepregs, short for pre-impregnated, are composite materials consisting of a reinforcement fabric (usually glass or aramid) impregnated with a partially cured resin system. They are used as insulating layers between the conductive layers in multi-layer PCBs. Prepregs provide mechanical strength, dimensional stability, and bonding between the layers during the lamination process.
4.2 Types of Prepregs
Prepregs are classified based on their resin system and reinforcement fabric. Some common types include:
- FR-4 prepregs (epoxy resin with glass fabric)
- Polyimide prepregs (polyimide resin with glass or aramid fabric)
- High-Tg prepregs (modified epoxy resin with glass fabric)
The choice of prepreg depends on the desired electrical, thermal, and mechanical properties of the PCB.
4.3 Prepreg Properties
Property | FR-4 | Polyimide | High-Tg |
---|---|---|---|
Dielectric Constant | 4.2-4.5 | 3.2-3.5 | 3.8-4.0 |
Dissipation Factor | 0.02 | 0.002-0.008 | 0.01-0.015 |
Tg (°C) | 130-140 | 260-320 | 170-180 |
CTE (ppm/°C) | 14-16 | 20-40 | 12-14 |
5. Bonding Films
5.1 What are Bonding Films?
Bonding films, also known as adhesive films or laminating films, are thin layers of adhesive material used to bond the layers of a multi-layer PCB together. They provide a strong, reliable, and void-free bond between the conductive layers and the dielectric substrates. Bonding films also help to distribute stress evenly across the PCB, improving its overall mechanical integrity.
5.2 Types of Bonding Films
There are two main types of bonding films used in HDI materials:
- Epoxy-based bonding films
- Acrylic-based bonding films
Epoxy-based bonding films offer better thermal and chemical resistance, while acrylic-based bonding films provide better flexibility and adhesion to a wide range of substrates.
5.3 Bonding Film Properties
Property | Epoxy-based | Acrylic-based |
---|---|---|
Peel Strength (N/cm) | >7 | >5 |
Tensile Strength (MPa) | >50 | >30 |
Elongation (%) | 5-10 | 20-50 |
Tg (°C) | 100-120 | 80-100 |
CTE (ppm/°C) | 50-60 | 60-70 |
6. Conductive Inks
6.1 What are Conductive Inks?
Conductive inks are specialized materials used for printing conductive patterns on various substrates, including flexible and rigid PCBs. They are composed of conductive particles (such as silver, copper, or carbon) suspended in a liquid vehicle. Conductive inks enable the creation of fine-pitch traces, interconnects, and other conductive features in HDI applications.
6.2 Types of Conductive Inks
There are several types of conductive inks used in HDI materials:
- Silver-based inks
- Copper-based inks
- Carbon-based inks
- Nanoparticle inks
Silver-based inks are the most widely used due to their high conductivity and stability. Copper-based inks offer a lower-cost alternative, while carbon-based inks are used for resistive elements. Nanoparticle inks enable the creation of ultra-fine features and are suitable for flexible substrates.
6.3 Conductive Ink Properties
Property | Silver | Copper | Carbon |
---|---|---|---|
Resistivity (µΩ·cm) | 1-5 | 5-10 | 50-100 |
Curing Temperature (°C) | 120-150 | 150-180 | 80-120 |
Adhesion | Good | Fair | Good |
Flexibility | Good | Fair | Excellent |
7. Flexible Substrates
7.1 What are Flexible Substrates?
Flexible substrates are thin, bendable materials used for creating flexible PCBs (FPCBs). They enable the production of lightweight, compact, and conformable electronic devices that can withstand bending, folding, and twisting. Flexible substrates are essential for applications such as wearable electronics, medical devices, and automotive components.
7.2 Common Flexible Substrates
Some common flexible substrates used in HDI materials include:
- Polyimide (PI)
- Polyethylene terephthalate (PET)
- Polyethylene naphthalate (PEN)
- Flexible copper clad laminate (FCCL)
Polyimide is the most widely used flexible substrate due to its excellent thermal stability, mechanical strength, and chemical resistance. PET and PEN are lower-cost alternatives with good optical clarity. FCCL is a composite material consisting of a thin copper foil bonded to a flexible dielectric substrate.
7.3 Flexible Substrate Properties
Substrate | Dielectric Constant | Dissipation Factor | Tensile Strength (MPa) | Elongation (%) |
---|---|---|---|---|
Polyimide | 3.2-3.5 | 0.002-0.008 | 150-300 | 20-50 |
PET | 3.0-3.2 | 0.002-0.005 | 50-70 | 50-150 |
PEN | 3.1-3.3 | 0.002-0.005 | 100-200 | 20-50 |
FCCL | 3.5-4.0 | 0.02-0.03 | 200-300 | 5-10 |
8. Solderable Finishes
8.1 What are Solderable Finishes?
Solderable finishes are thin metallic coatings applied to the exposed copper surfaces of a PCB to protect them from oxidation and enhance solderability. They ensure reliable and consistent solder joints during the component assembly process. Solderable finishes also help to prevent the formation of intermetallic compounds that can degrade the solder joint strength over time.
8.2 Common Solderable Finishes
Some common solderable finishes used in HDI materials include:
- Hot air solder leveling (HASL)
- Electroless nickel immersion gold (ENIG)
- Immersion tin (ImSn)
- Immersion silver (ImAg)
- Organic solderability preservative (OSP)
HASL is a traditional solderable finish that involves dipping the PCB in molten solder and then leveling the surface with hot air. ENIG, ImSn, and ImAg are immersion finishes that provide a flat, solderable surface without the need for leveling. OSP is a thin, organic coating that protects the copper surface and enhances solderability.
8.3 Solderable Finish Properties
Finish | Thickness (µm) | Shelf Life (months) | Solderability | Flatness |
---|---|---|---|---|
HASL | 1-20 | 12-24 | Good | Fair |
ENIG | 3-6 | 12-24 | Excellent | Excellent |
ImSn | 0.5-1.5 | 6-12 | Good | Excellent |
ImAg | 0.1-0.3 | 6-12 | Fair | Excellent |
OSP | 0.2-0.5 | 3-6 | Good | Excellent |
9. Underfill Materials
9.1 What are Underfill Materials?
Underfill materials are specialized polymeric compounds used to fill the gap between a chip (such as a flip chip or BGA) and the substrate. They provide mechanical support, stress relief, and protection against moisture and contaminants. Underfill materials help to improve the reliability and durability of chip-to-substrate interconnections, particularly in harsh environments or under thermal cycling conditions.
9.2 Types of Underfill Materials
There are two main types of underfill materials used in HDI applications:
- Capillary underfill (CUF)
- No-flow underfill (NUF)
CUF is applied after the chip is soldered to the substrate, and it flows into the gap by capillary action. NUF is applied before the chip is placed, and it cures during the solder reflow process. NUF eliminates the need for a separate underfill dispense and flow step, making it more suitable for high-volume production.
9.3 Underfill Material Properties
Property | CUF | NUF |
---|---|---|
Viscosity (Pa·s) | 1-10 | 10-100 |
Filler Content (wt%) | 50-70 | 30-50 |
Tg (°C) | 120-150 | 100-130 |
CTE (ppm/°C) | 20-30 | 30-40 |
Modulus (GPa) | 5-10 | 3-7 |
10. Thermal Interface Materials
10.1 What are Thermal Interface Materials?
Thermal interface materials (TIMs) are compounds used to enhance heat transfer between a heat-generating component (such as a chip or power module) and a heat sink or spreader. They fill the air gaps and microscopic irregularities between the mating surfaces, reducing thermal resistance and improving cooling efficiency. TIMs are essential for managing heat dissipation in high-performance electronic devices.
10.2 Types of Thermal Interface Materials
There are several types of TIMs used in HDI applications:
- Thermal greases
- Thermal pads
- Phase change materials (PCMs)
- Thermal adhesives
Thermal greases are paste-like materials that are applied between the component and heat sink. Thermal pads are pre-cut, conformable sheets that provide a clean and easy-to-use interface. PCMs are solid at room temperature but soften and flow at elevated temperatures to fill the gaps. Thermal adhesives provide both thermal conductivity and structural bonding.
10.3 Thermal Interface Material Properties
Property | Thermal Grease | Thermal Pad | PCM | Thermal Adhesive |
---|---|---|---|---|
Thermal Conductivity (W/m·K) | 1-10 | 1-5 | 1-5 | 1-2 |
Thermal Resistance (°C·cm²/W) | 0.1-0.5 | 0.5-1.0 | 0.2-0.5 | 0.5-1.0 |
Bond Line Thickness (µm) | 50-200 | 200-500 | 50-200 | 50-100 |
Dielectric Strength (kV/mm) | N/A | 10-20 | 10-20 | 10-20 |
11. Electromagnetic Shielding Materials
11.1 What are Electromagnetic Shielding Materials?
Electromagnetic shielding materials are used to protect electronic devices from electromagnetic interference (EMI) and radio
No responses yet