Introduction
Printed Circuit Board (PCB) assembly is a crucial process in electronics manufacturing. However, it can also be one of the most expensive aspects of the process. As a result, many manufacturers are always looking for ways to reduce PCB Assembly Costs without compromising on quality. In this article, we will discuss 11 effective ways to cut PCB assembly costs while maintaining high quality standards.
1. Design for Manufacturability (DFM)
What is DFM?
Design for Manufacturability (DFM) is a design approach that takes into account the manufacturing process during the design phase. The goal of DFM is to design products that are easy to manufacture, which can help reduce costs and improve quality.
How DFM Can Help Cut PCB Assembly Costs
By designing PCBs with manufacturability in mind, you can reduce the number of manufacturing steps required, minimize the risk of defects, and improve yields. This can help reduce overall assembly costs without sacrificing quality.
Some key DFM considerations for PCB design include:
- Choosing standard component sizes and packages
- Using generous spacing between components
- Avoiding tight tolerances and small features
- Using consistent hole sizes and pad shapes
- Minimizing the number of layers in the PCB
2. Use Standard Components
Benefits of Using Standard Components
Using standard components instead of custom or specialized parts can help reduce PCB assembly costs in several ways:
- Standard components are widely available and typically less expensive than custom parts
- Standard components are easier to source and replace if needed
- Standard components have proven reliability and performance
How to Identify Standard Components
To identify standard components for your PCB design, consider the following:
- Check with your component suppliers for their standard product offerings
- Look for components that are widely used in the industry and have multiple sources
- Avoid using components that are near the end of their lifecycle or have limited availability
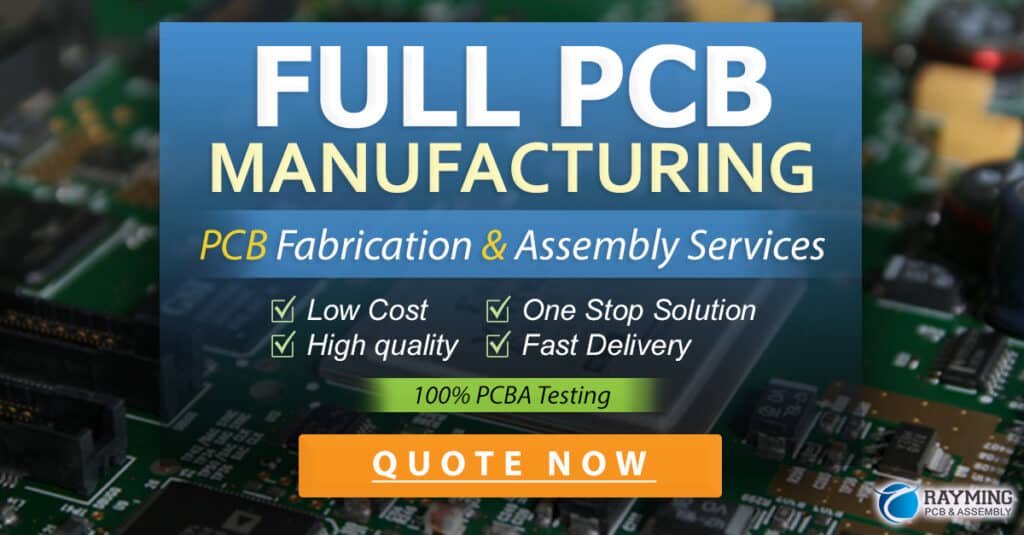
3. Optimize Panel Utilization
What is Panel Utilization?
Panel utilization refers to the arrangement of PCBs on a manufacturing panel to maximize the number of boards that can be produced in a single run. Optimizing panel utilization can help reduce PCB assembly costs by minimizing waste and increasing throughput.
Tips for Optimizing Panel Utilization
To optimize panel utilization, consider the following tips:
- Work with your PCB fabricator to determine the optimal panel size for your design
- Arrange PCBs on the panel to maximize the number of boards that can fit
- Consider using a panel layout that allows for easy depanelization, such as V-scoring or tab routing
- Minimize the amount of unused space on the panel to reduce waste
4. Reduce Layer Count
Impact of Layer Count on PCB Assembly Cost
The number of layers in a PCB can have a significant impact on assembly costs. In general, the more layers a PCB has, the more expensive it will be to manufacture. This is because each additional layer requires more materials, processing steps, and time to produce.
How to Reduce Layer Count
To reduce the number of layers in your PCB design, consider the following strategies:
- Use smaller components and narrower traces to minimize the amount of routing required
- Optimize component placement to minimize the need for vias and layer transitions
- Consider using a hybrid design that combines surface mount and through-hole components on the same side of the board
5. Use Automated Assembly Processes
Benefits of Automated Assembly
Automated assembly processes, such as pick-and-place machines and reflow ovens, can help reduce PCB assembly costs in several ways:
- Automated processes are faster and more efficient than manual assembly
- Automated processes can handle smaller components and tighter tolerances than manual assembly
- Automated processes are more consistent and repeatable, which can help improve quality and reduce defects
Key Considerations for Automated Assembly
To take full advantage of automated assembly processes, consider the following:
- Design your PCBs with automation in mind, using standard component sizes and packages
- Work with your assembly partner to determine the optimal machine settings and process parameters for your design
- Consider using a stencil for solder paste application to improve consistency and reduce defects
6. Minimize Tooling Costs
What are Tooling Costs?
Tooling costs refer to the one-time expenses associated with creating custom tools, fixtures, and stencils for PCB assembly. These costs can add up quickly, especially for low-volume production runs.
Strategies for Minimizing Tooling Costs
To minimize tooling costs, consider the following strategies:
- Use standard component sizes and packages to avoid the need for custom tooling
- Work with your assembly partner to determine the minimum tooling requirements for your design
- Consider using a panelized design to amortize tooling costs across multiple boards
- Reuse existing tooling whenever possible to avoid unnecessary expenses
7. Optimize Testing and Inspection
Importance of Testing and Inspection
Testing and inspection are critical steps in the PCB assembly process to ensure quality and reliability. However, excessive testing and inspection can also add unnecessary costs and delays to the process.
Strategies for Optimizing Testing and Inspection
To optimize testing and inspection, consider the following strategies:
- Use automated optical inspection (AOI) to quickly identify defects and reduce manual inspection time
- Consider using boundary scan testing to verify the functionality of complex components and circuits
- Work with your assembly partner to develop a testing and inspection plan that balances cost and quality requirements
- Use statistical process control (SPC) techniques to monitor and optimize the assembly process over time
8. Leverage Volume Discounts
How Volume Discounts Work
Volume discounts are price reductions offered by suppliers and assembly partners for larger order quantities. By leveraging volume discounts, you can reduce the unit cost of your PCBs and improve your overall profitability.
Tips for Leveraging Volume Discounts
To leverage volume discounts effectively, consider the following tips:
- Work with your suppliers and assembly partners to negotiate volume discounts based on your projected order quantities
- Consider consolidating orders across multiple products or projects to increase volume and qualify for higher discounts
- Use long-term contracts or blanket purchase orders to lock in volume discounts over an extended period
- Be aware of minimum order quantities (MOQs) and lead times associated with volume orders
9. Use Offshore Manufacturing
Benefits of Offshore Manufacturing
Offshore manufacturing, or outsourcing PCB assembly to lower-cost regions such as China or India, can help reduce assembly costs significantly. Some benefits of offshore manufacturing include:
- Lower labor costs compared to domestic manufacturing
- Access to a wider range of suppliers and manufacturing capabilities
- Potential for faster turnaround times due to time zone differences
Risks and Considerations for Offshore Manufacturing
While offshore manufacturing can offer significant cost savings, it also comes with some risks and considerations, such as:
- Longer shipping times and potential delays due to customs and logistics
- Language and cultural barriers that can impact communication and quality control
- Intellectual property and security concerns, especially for sensitive or proprietary designs
- Potential for quality issues due to differences in manufacturing standards and practices
10. Consider Alternative Materials
Benefits of Alternative Materials
Using alternative materials, such as cheaper substrates or surface finishes, can help reduce PCB assembly costs without sacrificing quality. Some benefits of alternative materials include:
- Lower material costs compared to traditional options
- Improved performance characteristics, such as better thermal or electrical properties
- Easier manufacturability and faster processing times
Key Considerations for Alternative Materials
When considering alternative materials for your PCB design, keep the following in mind:
- Ensure that the alternative material meets your performance and reliability requirements
- Work with your suppliers and assembly partners to validate the compatibility and processability of the alternative material
- Consider the long-term availability and cost stability of the alternative material
- Be aware of any regulatory or environmental concerns associated with the alternative material
11. Partner with a Reliable PCB Assembly Provider
Benefits of Partnering with a Reliable Provider
Partnering with a reliable PCB assembly provider can help reduce costs and improve quality in several ways:
- Access to a wider range of manufacturing capabilities and expertise
- Improved purchasing power and volume discounts through the provider’s supplier network
- Faster turnaround times and more flexible production schedules
- Consistent quality and reliability through the provider’s established processes and quality control measures
How to Choose a Reliable PCB Assembly Provider
To choose a reliable PCB assembly provider, consider the following factors:
- Look for a provider with a proven track record of quality and on-time delivery
- Evaluate the provider’s manufacturing capabilities and capacity to ensure they can meet your needs
- Consider the provider’s location and logistics capabilities to minimize shipping times and costs
- Look for a provider with strong communication and customer support to ensure smooth project management
- Evaluate the provider’s quality control and testing processes to ensure they meet your standards
Conclusion
In conclusion, there are many effective ways to cut PCB assembly costs without sacrificing quality. By designing for manufacturability, using standard components, optimizing panel utilization, reducing layer count, using automated assembly processes, minimizing tooling costs, optimizing testing and inspection, leveraging volume discounts, considering offshore manufacturing, using alternative materials, and partnering with a reliable PCB assembly provider, you can reduce your overall assembly costs while maintaining high quality standards. However, it’s important to carefully evaluate each strategy and consider the specific needs and requirements of your project to ensure the best possible outcome.
FAQs
1. What is the most effective way to reduce PCB assembly costs?
There is no single “most effective” way to reduce PCB assembly costs, as the best approach will depend on the specific needs and requirements of your project. However, some of the most impactful strategies include designing for manufacturability, using standard components, optimizing panel utilization, and leveraging volume discounts.
2. How much can I expect to save by using offshore manufacturing for PCB assembly?
The cost savings from offshore manufacturing can vary widely depending on factors such as the specific location, manufacturing capabilities, and shipping and logistics costs. In general, offshore manufacturing can offer cost savings of 20-50% compared to domestic manufacturing, but it’s important to carefully evaluate the potential risks and considerations before making a decision.
3. What are some common mistakes to avoid when trying to reduce PCB assembly costs?
Some common mistakes to avoid when trying to reduce PCB assembly costs include:
– Sacrificing quality for cost savings
– Failing to consider the long-term implications of cost-cutting measures
– Neglecting to communicate effectively with suppliers and assembly partners
– Underestimating the importance of testing and inspection in ensuring quality and reliability
– Focusing too narrowly on one cost-cutting strategy without considering the bigger picture
4. How can I ensure that cost-cutting measures don’t negatively impact the quality of my PCBs?
To ensure that cost-cutting measures don’t negatively impact the quality of your PCBs, consider the following:
– Prioritize design for manufacturability and use standard components to minimize defects and improve yields
– Work closely with your suppliers and assembly partners to establish clear quality standards and expectations
– Use automated inspection and testing processes to catch defects early and minimize rework
– Monitor and analyze quality metrics over time to identify areas for improvement and optimization
5. What are some long-term benefits of reducing PCB assembly costs?
Some long-term benefits of reducing PCB assembly costs include:
– Improved profitability and competitiveness in the market
– Increased flexibility and agility to respond to changing customer needs and market conditions
– Stronger relationships with suppliers and assembly partners based on trust and mutual benefit
– Greater ability to invest in innovation and growth opportunities
– Enhanced reputation and brand value based on delivering high-quality products at competitive prices
By taking a strategic and holistic approach to reducing PCB assembly costs, you can achieve significant savings and benefits over the long term while maintaining the highest standards of quality and reliability.
No responses yet