Introduction to Impedance Control
Impedance control is a crucial aspect of designing and manufacturing high-speed electronic systems. It involves managing the impedance of transmission lines to ensure that signals maintain their integrity as they propagate through the system. Proper impedance control minimizes signal reflections, crosstalk, and electromagnetic interference (EMI), which can cause signal distortion, data errors, and system malfunctions.
In this article, we will explore ten effective ways to avoid signal integrity problems by implementing impedance control techniques. By understanding and applying these methods, designers and engineers can create robust, reliable, and high-performance electronic systems.
1. Understand the Basics of Impedance Matching
To effectively control impedance, it is essential to understand the fundamentals of impedance matching. Impedance matching ensures that the impedance of the source, transmission line, and load are equal, minimizing signal reflections and power loss. The characteristic impedance (Z0) of a transmission line is determined by its physical properties, such as the conductor width, thickness, and the dielectric constant of the substrate material.
The most common characteristic impedance values for PCB designs are:
Impedance (Ω) | Application |
---|---|
50 | RF and microwave circuits |
75 | Video and coaxial cable applications |
90-120 | High-speed digital systems |
By matching the impedance of the source and load to the characteristic impedance of the transmission line, designers can minimize signal reflections and ensure optimal signal transfer.
2. Choose the Right PCB Materials
Selecting the appropriate PCB materials is crucial for achieving effective impedance control. The dielectric constant (Dk) and dissipation factor (Df) of the substrate material significantly influence the characteristic impedance of the transmission lines. Materials with a consistent Dk and low Df, such as Rogers RO4000 series or Isola IS410, are preferred for high-speed designs.
Additionally, the copper weight and roughness of the PCB laminate affect the conductor losses and impedance. Choosing a laminate with a suitable copper weight and smooth surface finish helps maintain the desired impedance and reduces signal attenuation.
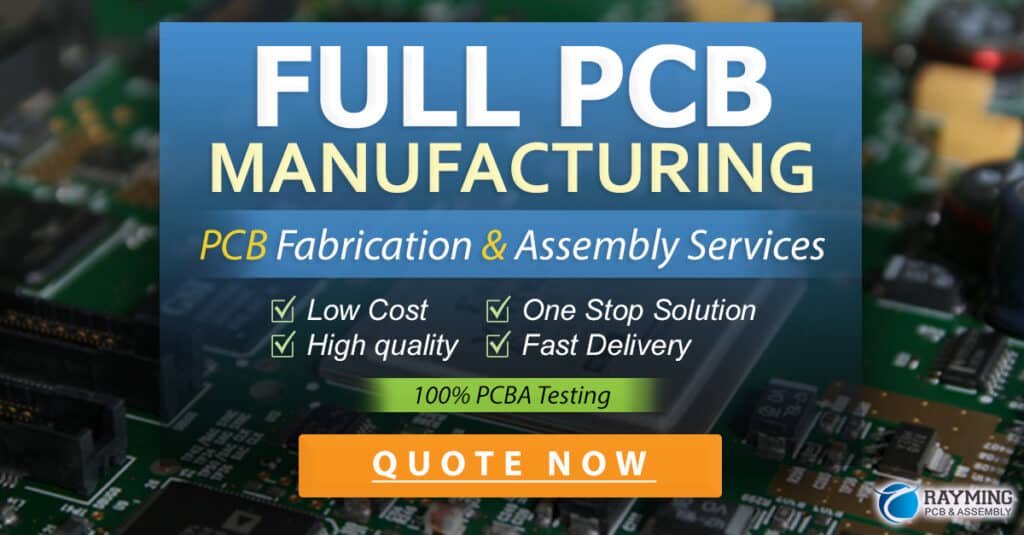
3. Control Trace Geometry
The geometry of the PCB traces plays a vital role in impedance control. The width, thickness, and spacing of the traces determine their characteristic impedance. To achieve the desired impedance, designers must carefully calculate and adjust these parameters based on the chosen PCB material and layer stack-up.
Some common trace geometries for impedance control include:
- Microstrip: A single conductor trace on the top or bottom layer of the PCB, with a reference plane beneath it.
- Stripline: A conductor trace sandwiched between two reference planes, typically used for inner layers.
- Coplanar waveguide: A trace with ground planes on either side, on the same layer.
By using PCB design tools with built-in impedance calculators, designers can accurately determine the required trace dimensions to achieve the target impedance.
4. Implement Proper Grounding Techniques
Effective grounding is essential for maintaining signal integrity and controlling impedance. A well-designed ground plane provides a low-impedance return path for high-speed signals, minimizing ground bounce and EMI. Some grounding techniques to consider include:
- Uninterrupted ground planes: Use solid, uninterrupted ground planes whenever possible to provide a stable reference for signals.
- Via stitching: Place ground vias at regular intervals along the signal traces to minimize the inductance of the return path.
- Partitioned ground planes: In mixed-signal designs, use separate ground planes for analog and digital sections to minimize noise coupling.
5. Optimize Via Design
Vias are essential for connecting traces across different layers of a PCB, but they can also introduce impedance discontinuities and signal integrity issues. To minimize the impact of vias on impedance control, consider the following:
- Via size: Use the smallest via size that is feasible for manufacturing and reliability to minimize the capacitance and inductance of the via.
- Via placement: Place vias as close to the signal trace as possible to minimize the stub length and reflections.
- Back-drilling: Remove the unused portion of the via barrel to reduce the stub effect and improve impedance matching.
6. Employ Termination Techniques
Termination techniques are used to match the impedance of the load to the characteristic impedance of the transmission line, minimizing signal reflections. The most common termination methods include:
- Series termination: A resistor is placed in series with the source, matching the source impedance to the line impedance.
- Parallel termination: A resistor is placed in parallel with the load, matching the load impedance to the line impedance.
- AC termination: A combination of resistors and capacitors is used to provide frequency-dependent termination.
The choice of termination technique depends on factors such as the signal frequency, rise time, and the characteristics of the source and load.
7. Implement Differential Signaling
Differential signaling is a technique that uses two complementary signals to transmit data, providing better noise immunity and reducing EMI compared to single-ended signaling. Differential pairs also have a well-defined impedance, making impedance control easier. When implementing differential signaling, consider the following:
- Pair routing: Route differential pairs closely together to maintain a constant spacing and minimize any impedance mismatch.
- Length matching: Ensure that the lengths of the positive and negative traces within a differential pair are closely matched to avoid skew and maintain signal integrity.
- Coupling: Control the coupling between differential pairs to minimize crosstalk and maintain the desired differential impedance.
8. Perform Signal Integrity Simulations
Signal integrity simulations are essential for verifying the impedance control strategies and identifying potential issues before fabricating the PCB. These simulations help designers analyze the behavior of high-speed signals, including reflections, crosstalk, and EMI. Some popular signal integrity simulation tools include:
- Mentor Graphics HyperLynx
- Cadence Sigrity
- Ansys HFSS
By performing pre-layout and post-layout simulations, designers can optimize the PCB design for impedance control and ensure that the system meets the required performance specifications.
9. Conduct Impedance Measurements
After fabricating the PCB, it is crucial to perform impedance measurements to verify that the actual impedance matches the designed values. Impedance measurements can be done using techniques such as:
- Time Domain Reflectometry (TDR): Measures the impedance of a transmission line by sending a fast rise time pulse and analyzing the reflections.
- Vector Network Analyzer (VNA): Measures the S-parameters of a transmission line, providing information about its impedance, loss, and phase response.
By conducting impedance measurements, designers can identify any discrepancies between the designed and actual impedance values and take corrective actions if necessary.
10. Follow PCB Manufacturing Guidelines
To ensure that the PCB fabrication process maintains the desired impedance control, it is essential to follow the manufacturing guidelines provided by the PCB manufacturer. These guidelines include:
- Layer stack-up: Provide a detailed layer stack-up diagram specifying the material types, thicknesses, and copper weights for each layer.
- Impedance tolerances: Specify the acceptable impedance tolerances for the controlled impedance traces, typically ±10% or tighter.
- Trace width and spacing: Provide the exact trace width and spacing requirements for the controlled impedance traces.
- Test coupons: Include impedance test coupons on the PCB panel to allow the manufacturer to verify the impedance values before shipping the boards.
By adhering to the manufacturing guidelines and maintaining open communication with the PCB manufacturer, designers can ensure that the fabricated boards meet the impedance control requirements.
Frequently Asked Questions (FAQ)
- What is the purpose of impedance control in PCB design?
-
Impedance control ensures that the impedance of the transmission lines matches the impedance of the source and load, minimizing signal reflections, crosstalk, and EMI. This helps maintain signal integrity and ensures reliable high-speed data transmission.
-
What factors affect the characteristic impedance of a transmission line?
-
The characteristic impedance of a transmission line is determined by factors such as the conductor width, thickness, spacing, and the dielectric constant of the substrate material. The copper weight and roughness of the PCB laminate also influence the impedance.
-
What are the most common impedance values for PCB designs?
-
The most common characteristic impedance values for PCB designs are 50 Ω for RF and microwave circuits, 75 Ω for video and coaxial cable applications, and 90-120 Ω for high-speed digital systems.
-
How can signal integrity simulations help with impedance control?
-
Signal integrity simulations allow designers to analyze the behavior of high-speed signals, including reflections, crosstalk, and EMI. By performing pre-layout and post-layout simulations, designers can optimize the PCB design for impedance control and ensure that the system meets the required performance specifications.
-
What should be included in the PCB manufacturing guidelines for impedance control?
- The PCB manufacturing guidelines for impedance control should include a detailed layer stack-up diagram, impedance tolerances, trace width and spacing requirements, and impedance test coupons. By providing this information to the PCB manufacturer and maintaining open communication, designers can ensure that the fabricated boards meet the impedance control requirements.
Conclusion
Impedance control is a critical aspect of designing and manufacturing high-speed electronic systems. By understanding and implementing the ten ways to avoid signal integrity problems discussed in this article, designers and engineers can create robust, reliable, and high-performance systems. From understanding the basics of impedance matching to selecting the right PCB materials, controlling trace geometry, and following manufacturing guidelines, each step plays a crucial role in achieving effective impedance control.
As technology advances and data rates continue to increase, the importance of impedance control will only grow. By staying up-to-date with the latest techniques and tools for managing impedance, designers can tackle the challenges of high-speed design and ensure the success of their projects.
No responses yet