Introduction
Printed circuit board (PCB) design is a complex process that requires careful attention to detail and adherence to best practices to ensure optimal performance, reliability, and manufacturability. One critical aspect of PCB Design is managing and utilizing data effectively. Poor data management can lead to numerous issues, such as design errors, manufacturing delays, and increased costs. In this article, we will discuss ten essential rules for better data management in PCB design to help you avoid common pitfalls and streamline your design process.
Rule 1: Establish a Consistent Naming Convention
Why Consistent Naming Matters
A consistent naming convention is crucial for organizing and managing your PCB design data efficiently. It helps you quickly identify and locate files, components, and other design elements, saving time and reducing the likelihood of errors. Additionally, a well-defined naming convention makes it easier for team members to collaborate and understand each other’s work.
Tips for Implementing a Naming Convention
- Use descriptive names that clearly indicate the purpose or function of each file or component.
- Include relevant information such as version numbers, dates, or project codes in file names.
- Avoid using special characters or spaces in file names, as they can cause issues with some software tools.
- Document your naming convention and ensure that all team members follow it consistently.
Rule 2: Maintain Accurate and Up-to-Date Libraries
The Importance of Libraries in PCB Design
Component libraries play a vital role in PCB design, as they contain essential information about the physical and electrical properties of components used in your design. Accurate and up-to-date libraries ensure that your design is based on correct data, reducing the risk of errors and incompatibilities.
Best Practices for Library Management
- Regularly update your libraries with the latest component information from manufacturers.
- Verify the accuracy of component footprints, pinouts, and other critical data.
- Create custom libraries for frequently used components or specialized parts.
- Implement a version control system to track changes and maintain a history of library updates.
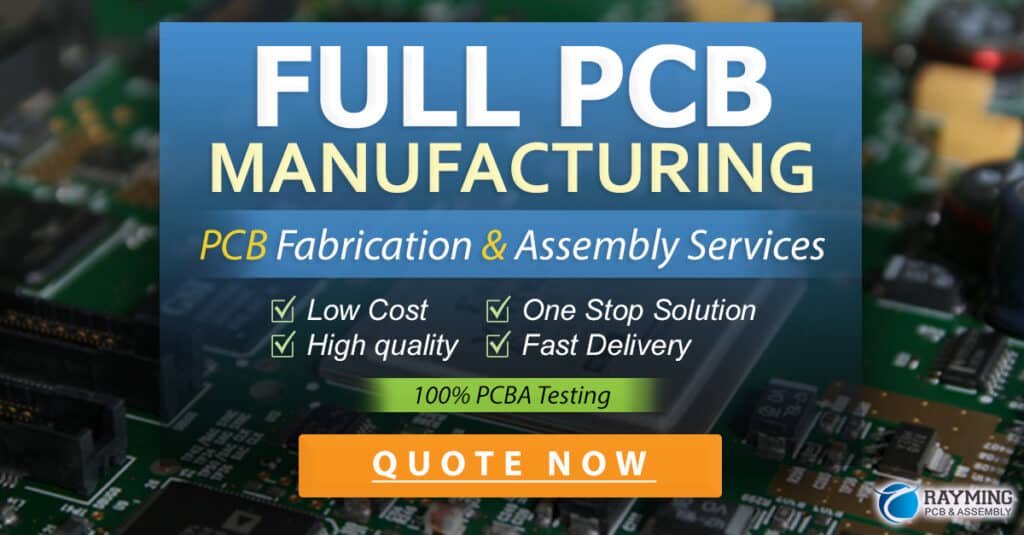
Rule 3: Use a Version Control System
Benefits of Version Control in PCB Design
Version control systems, such as Git or Subversion, allow you to track changes to your design files over time, collaborate with team members, and revert to previous versions if necessary. By using a version control system, you can:
- Easily identify and resolve conflicts between different versions of your design.
- Maintain a complete history of your design changes, making it easier to troubleshoot issues.
- Collaborate with team members without the risk of overwriting each other’s work.
Implementing Version Control in Your Design Workflow
- Choose a version control system that integrates well with your PCB design software.
- Establish a branching and merging strategy that suits your team’s needs and project requirements.
- Regularly commit changes to the version control system, providing clear and concise descriptions of each commit.
- Use version control to manage not only your design files but also related documentation and project data.
Rule 4: Implement a Robust Backup Strategy
Protecting Your Design Data
A robust backup strategy is essential for protecting your PCB design data from loss due to hardware failures, software issues, or human error. By regularly backing up your data, you can minimize the impact of data loss and ensure that you can quickly recover and continue working on your design.
Elements of a Robust Backup Strategy
- Perform regular backups of your design files, libraries, and related data.
- Use a combination of local and cloud-based backup solutions for added protection.
- Test your backups periodically to ensure that they are functioning correctly and can be restored if needed.
- Establish a backup schedule that aligns with your project’s needs and the frequency of design changes.
Rule 5: Utilize a Centralized Data Management System
Benefits of Centralized Data Management
A centralized data management system, such as a product data management (PDM) or product lifecycle management (PLM) solution, can help streamline your PCB design process by providing a single source of truth for all your design data. By using a centralized system, you can:
- Ensure that all team members have access to the latest version of design files and related data.
- Improve collaboration and communication among team members.
- Automate workflows and approval processes, reducing the risk of errors and delays.
Implementing a Centralized Data Management System
- Evaluate your team’s needs and choose a data management solution that aligns with your requirements and budget.
- Establish clear roles, permissions, and workflows within the system to ensure data integrity and security.
- Train your team members on how to use the system effectively and efficiently.
- Regularly review and optimize your data management processes to identify areas for improvement.
Rule 6: Define and Adhere to Design Standards
The Importance of Design Standards
Design standards ensure consistency, compatibility, and quality across your PCB designs. By defining and adhering to a set of standards, you can:
- Reduce the risk of errors and incompatibilities in your designs.
- Improve the manufacturability and reliability of your PCBs.
- Streamline the design process by providing clear guidelines for team members to follow.
Establishing and Implementing Design Standards
- Research and adopt industry-standard design guidelines, such as IPC Standards, where applicable.
- Develop custom design standards specific to your organization’s needs and requirements.
- Document your design standards clearly and make them easily accessible to all team members.
- Regularly review and update your standards to keep pace with changing technologies and best practices.
Rule 7: Implement Design Rule Checks (DRC)
The Role of DRC in PCB Design
Design Rule Checks (DRC) are automated checks that verify your PCB design against a set of predefined rules to identify potential issues or violations. By implementing DRC in your design process, you can:
- Catch design errors early in the process, reducing the need for costly revisions later on.
- Ensure that your design adheres to manufacturing constraints and industry standards.
- Improve the overall quality and reliability of your PCBs.
Best Practices for Implementing DRC
- Define a comprehensive set of design rules that cover all aspects of your PCB design, including electrical, mechanical, and manufacturing constraints.
- Integrate DRC into your design workflow, running checks at regular intervals and before finalizing your design.
- Review and address all DRC violations promptly, documenting any necessary changes or exceptions.
- Continuously update and refine your design rules based on feedback from manufacturing partners and real-world performance data.
Rule 8: Foster Effective Communication and Collaboration
The Benefits of Effective Communication and Collaboration
Effective communication and collaboration among team members are essential for successful PCB design projects. By fostering a culture of open communication and collaboration, you can:
- Ensure that all team members are aligned on project goals, timelines, and deliverables.
- Identify and resolve design issues more quickly and efficiently.
- Leverage the collective knowledge and expertise of your team to make better design decisions.
Strategies for Improving Communication and Collaboration
- Use collaborative tools, such as project management software or online communication platforms, to facilitate seamless information sharing and discussion.
- Schedule regular team meetings to discuss project progress, challenges, and opportunities for improvement.
- Encourage a culture of openness and transparency, where team members feel comfortable sharing ideas, concerns, and feedback.
- Foster cross-functional collaboration among design, engineering, manufacturing, and other relevant departments to ensure a holistic approach to PCB design.
Rule 9: Conduct Regular Design Reviews
The Importance of Design Reviews
Regular design reviews are crucial for catching errors, identifying areas for improvement, and ensuring that your PCB design meets all requirements and specifications. By conducting design reviews at key milestones throughout the design process, you can:
- Identify and address potential issues early on, reducing the risk of costly rework later in the project.
- Gather valuable feedback from stakeholders and subject matter experts to improve the quality and functionality of your design.
- Ensure that your design aligns with project goals, timelines, and budgetary constraints.
Best Practices for Conducting Design Reviews
- Establish a clear schedule and agenda for design reviews, ensuring that all relevant stakeholders are involved.
- Prepare and distribute design documentation, such as schematics, layouts, and Bill of Materials (BOM), in advance of the review to allow participants to familiarize themselves with the design.
- Encourage open and constructive feedback during the review, focusing on identifying areas for improvement rather than assigning blame.
- Document all feedback, action items, and decisions made during the review, and follow up to ensure that all necessary changes are implemented.
Rule 10: Continuously Improve Your Design Process
The Benefits of Continuous Improvement
Continuously improving your PCB design process is essential for staying competitive, adapting to new technologies, and delivering high-quality products. By embracing a culture of continuous improvement, you can:
- Identify and eliminate inefficiencies and bottlenecks in your design workflow.
- Adopt new tools, techniques, and best practices to streamline your design process and improve quality.
- Foster a culture of innovation and learning within your organization.
Strategies for Continuous Improvement
- Regularly assess your design process to identify areas for improvement, using metrics such as design cycle time, error rates, and manufacturing yield.
- Encourage team members to share ideas and suggestions for process improvements, and implement the most promising ideas on a trial basis.
- Invest in training and professional development opportunities for your team members to keep their skills and knowledge up-to-date.
- Benchmark your design process against industry best practices and learn from the successes and failures of other organizations.
Frequently Asked Questions (FAQ)
1. What is the most important rule for better data management in PCB design?
While all ten rules discussed in this article are important for effective data management in PCB design, establishing a consistent naming convention (Rule 1) is perhaps the most critical. A well-defined and consistently applied naming convention forms the foundation for organizing and managing your design data efficiently, reducing the risk of errors and confusion.
2. How often should I update my component libraries?
It is recommended to update your component libraries regularly, ideally as soon as new information becomes available from manufacturers. The frequency of updates may vary depending on the components you use and the pace of technological advancements in your industry. At a minimum, aim to review and update your libraries at least once per quarter to ensure that you are working with accurate and up-to-date data.
3. What are the benefits of using a version control system in PCB design?
Using a version control system in PCB design offers several key benefits, including:
- Tracking changes to your design files over time, making it easier to identify and resolve issues.
- Enabling collaboration among team members without the risk of overwriting each other’s work.
- Maintaining a complete history of your design changes, which can be invaluable for troubleshooting and auditing purposes.
4. How can I ensure that my team members adhere to design standards?
To ensure that your team members adhere to design standards, consider the following strategies:
- Clearly document your design standards and make them easily accessible to all team members.
- Provide training and support to help team members understand and apply the standards consistently.
- Implement automated design rule checks (DRC) to verify compliance with standards and identify potential issues early in the design process.
- Regularly review and audit designs to ensure that standards are being followed and address any deviations promptly.
5. What are some common pitfalls to avoid when implementing a centralized data management system?
When implementing a centralized data management system, be aware of the following common pitfalls:
- Failing to clearly define roles, permissions, and workflows within the system, leading to confusion and potential data integrity issues.
- Not providing adequate training and support for team members, resulting in low adoption rates and inefficient use of the system.
- Choosing a system that does not align with your organization’s specific needs and requirements, leading to suboptimal performance and user frustration.
- Neglecting to regularly review and optimize your data management processes, causing the system to become outdated and less effective over time.
Conclusion
Effective data management is crucial for success in PCB design, as it directly impacts the quality, reliability, and efficiency of your design process. By following the ten rules outlined in this article – from establishing a consistent naming convention to continuously improving your design process – you can avoid common pitfalls and ensure that your design data is accurate, organized, and easily accessible to all team members.
Remember that implementing these rules is an ongoing process that requires commitment, collaboration, and continuous improvement. By fostering a culture of data management excellence within your organization, you can streamline your PCB design process, reduce errors and delays, and ultimately deliver better products to your customers.
Rule | Key Benefit |
---|---|
1. Establish a Consistent Naming Convention | Enables efficient organization and management of design data |
2. Maintain Accurate and Up-to-Date Libraries | Ensures design is based on correct component data |
3. Use a Version Control System | Facilitates collaboration and tracks design changes |
4. Implement a Robust Backup Strategy | Protects against data loss and ensures quick recovery |
5. Utilize a Centralized Data Management System | Provides a single source of truth and streamlines workflows |
6. Define and Adhere to Design Standards | Ensures consistency, compatibility, and quality across designs |
7. Implement Design Rule Checks (DRC) | Catches design errors early and ensures manufacturability |
8. Foster Effective Communication and Collaboration | Leverages collective knowledge and expertise to make better decisions |
9. Conduct Regular Design Reviews | Identifies issues early and ensures alignment with project goals |
10. Continuously Improve Your Design Process | Adapts to new technologies and delivers high-quality products |
By embracing these ten rules for better data management in PCB design, you can create a strong foundation for success in your design projects, ensuring that your team has the tools, processes, and mindset needed to navigate the complexities of modern PCB design with confidence and efficiency.
No responses yet