Understanding PCB Current Capacity
The current carrying capacity of PCB traces is a critical design consideration that affects the reliability, performance, and safety of electronic devices. PCB current capacity refers to the maximum amount of current that a copper trace on a printed circuit board can safely carry without overheating or suffering damage.
Several factors influence a PCB trace’s current capacity:
– Trace width
– Copper thickness (weight)
– Ambient temperature
– Allowed temperature rise
– Via size and number of vias
– Presence of thermal relief or heat sinks
Accurately calculating the current capacity and optimizing the PCB layout accordingly helps prevent issues like excessive voltage drop, damaged traces, component failure, and even fire hazards. Let’s explore 10 effective methods to achieve high-quality PCB trace current capacity.
Method 1: Increase Trace Width
One of the most straightforward ways to boost current capacity is by increasing the width of the copper traces. Wider traces have lower resistance and can handle higher currents without overheating.
The relationship between trace width and current capacity is not linear. Doubling the trace width does not double the current capacity. The following table provides a rough guideline for the current capacity of 1 oz copper traces at various widths, assuming a 10°C temperature rise:
Trace Width (mm) | Current Capacity (A) |
---|---|
0.25 | 0.5 |
0.5 | 1.0 |
1.0 | 1.7 |
2.0 | 2.8 |
3.0 | 3.7 |
However, increasing trace width comes with trade-offs. Wider traces occupy more board space, which can impact routing and component placement. It’s essential to find the right balance between current capacity and layout efficiency.
Method 2: Increase Copper Thickness
Another way to improve current capacity is by using thicker copper layers. PCB copper thickness is typically measured in ounces per square foot (oz/ft²). Standard copper weights are 0.5 oz, 1 oz, and 2 oz, with 1 oz being the most common.
Thicker copper provides more cross-sectional area for current flow, thus increasing current capacity. Here’s a comparison of current capacities for different copper weights, assuming a 10°C temperature rise and a trace width of 1 mm:
Copper Weight (oz) | Current Capacity (A) |
---|---|
0.5 | 1.2 |
1.0 | 1.7 |
2.0 | 2.4 |
Using thicker copper does have some drawbacks. It increases the overall board thickness, which may not be desirable for compact designs. Thicker copper is also more expensive and can be more challenging to etch during the PCB manufacturing process.
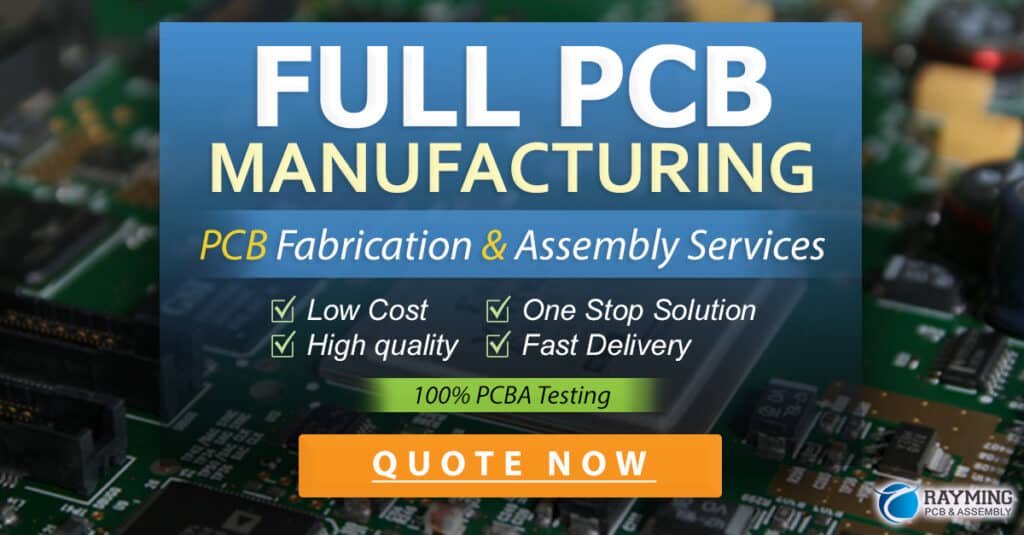
Method 3: Use Multiple Layers
For high-current applications, using multiple copper layers can significantly enhance current capacity. By distributing the current across multiple layers connected through vias, the effective cross-sectional area increases, allowing for higher current handling.
For example, using two 1 oz copper layers in parallel can provide a current capacity equivalent to a single 2 oz layer. This approach offers more flexibility in routing and can help maintain a thinner board profile compared to using a single thick copper layer.
Method 4: Optimize Ambient Temperature
The ambient temperature significantly affects a PCB trace’s current capacity. As the surrounding temperature increases, the trace’s ability to dissipate heat decreases, thus reducing its current carrying capacity.
Designers must consider the expected operating temperature range of the device and adjust the PCB layout accordingly. If the ambient temperature is expected to be high, wider traces or thicker copper may be necessary to compensate for the reduced heat dissipation.
The following table shows how the current capacity of a 1 oz, 1 mm wide trace decreases with increasing ambient temperature:
Ambient Temperature (°C) | Current Capacity (A) |
---|---|
25 | 1.7 |
50 | 1.4 |
75 | 1.1 |
100 | 0.8 |
To optimize current capacity, it’s crucial to ensure adequate ventilation and cooling in the device enclosure. Using thermal management techniques like heat sinks, fans, or thermal vias can help dissipate heat and maintain a lower ambient temperature around the PCB.
Method 5: Allow for Temperature Rise
When designing for current capacity, it’s essential to consider the acceptable temperature rise in the PCB traces. The temperature rise is the difference between the trace’s maximum temperature and the ambient temperature.
A higher allowed temperature rise enables traces to carry more current without exceeding thermal limits. However, it’s crucial to keep the temperature rise within safe limits to avoid damaging the PCB, components, or surrounding materials.
Industry standards and guidelines, such as IPC-2221, provide recommendations for maximum allowed temperature rises based on various factors, including the PCB material, component specifications, and application requirements.
Here’s an example of how the current capacity of a 1 oz, 1 mm wide trace increases with a higher allowed temperature rise:
Allowed Temperature Rise (°C) | Current Capacity (A) |
---|---|
10 | 1.7 |
20 | 2.4 |
30 | 3.0 |
40 | 3.4 |
Designers must carefully balance the allowed temperature rise with other design constraints and reliability considerations.
Method 6: Utilize Thermal Relief Pads
Thermal relief pads, also known as thermal spokes, are a design technique used to improve heat dissipation and increase current capacity in PCB traces connected to high-current components, such as power connectors or voltage regulators.
A thermal relief pad consists of a larger copper area surrounding the component pad, with several thin traces (spokes) connecting the pad to the larger copper area. This design allows for better heat dissipation by increasing the surface area for heat transfer while maintaining a reliable electrical connection.
Thermal relief pads are particularly useful in situations where a component is expected to generate significant heat or handle high currents. By dissipating heat more effectively, thermal relief pads help reduce the temperature rise in the connected traces, allowing for higher current capacity.
When designing thermal relief pads, consider factors such as the size of the copper area, the number and width of the spokes, and the spacing between the pad and the copper area. Simulation tools and thermal analysis can help optimize the design for maximum heat dissipation and current capacity.
Method 7: Use Vias for Heat Dissipation
Vias, the conductive paths that connect different layers of a PCB, can be used strategically to enhance heat dissipation and increase current capacity in high-current traces.
By placing vias along the length of a high-current trace, designers can create additional paths for heat to transfer between layers and spread out across the PCB. This technique is known as via stitching or via shielding.
When using vias for heat dissipation, consider the following factors:
- Via size: Larger vias have lower thermal resistance and can transfer heat more effectively.
- Via placement: Place vias at regular intervals along the trace to distribute heat evenly.
- Via plating: Ensure vias are plated with sufficient copper thickness to minimize thermal resistance.
- Via fill: Filling vias with a conductive material, such as copper or solder, can further improve heat transfer.
Using vias for heat dissipation can help reduce the temperature rise in high-current traces, allowing for higher current capacity without increasing trace width or copper thickness.
Method 8: Implement Heat Sinks
In some cases, passive heat dissipation techniques like wider traces or thermal relief pads may not be sufficient to manage the heat generated by high-current components. In such situations, implementing heat sinks can be an effective solution to increase current capacity.
Heat sinks are metal structures designed to absorb and dissipate heat from components or PCB traces. They typically have a large surface area with fins or protrusions to maximize heat transfer to the surrounding air.
To use heat sinks for increasing PCB trace current capacity:
- Identify the high-current traces or components that require additional cooling.
- Select an appropriate heat sink based on the expected heat generation and available space.
- Attach the heat sink to the PCB using thermal adhesive, mechanical fasteners, or soldering.
- Ensure proper thermal contact between the heat sink and the PCB trace or component.
- Consider using thermal interface materials (TIMs) like thermal pads or paste to enhance heat transfer.
By effectively dissipating heat away from the PCB, heat sinks help maintain lower trace temperatures, allowing for higher current capacity without compromising reliability.
Method 9: Optimize Trace Routing
Proper trace routing is essential for achieving high current capacity and minimizing electromagnetic interference (EMI) in PCB designs. When routing high-current traces, consider the following guidelines:
- Minimize trace length: Shorter traces have lower resistance and generate less heat, allowing for higher current capacity.
- Avoid sharp angles: Use gentle curves or 45-degree angles instead of 90-degree angles to reduce current crowding and heat concentration.
- Provide adequate spacing: Maintain sufficient spacing between high-current traces and other signals to minimize crosstalk and thermal interference.
- Use ground planes: Place high-current traces over a solid ground plane to provide a low-impedance return path and improve heat dissipation.
- Separate sensitive signals: Route high-current traces away from sensitive analog or high-speed digital signals to avoid interference.
By optimizing trace routing, designers can ensure efficient current flow, minimize heat generation, and improve overall PCB performance.
Method 10: Conduct Thorough Analysis and Testing
To ensure the PCB design meets the required current capacity and reliability standards, it is crucial to conduct thorough analysis and testing throughout the design process.
Some key steps in analyzing and testing PCB current capacity include:
-
Use PCB design software with built-in current capacity calculators to estimate trace widths and copper thicknesses required for the expected current levels.
-
Perform thermal simulations to predict the temperature distribution across the PCB and identify potential hot spots.
-
Conduct power integrity analysis to ensure adequate voltage delivery to components and minimize voltage drop along high-current traces.
-
Perform prototype testing under realistic operating conditions to validate the design’s current capacity and thermal performance.
-
Use thermal imaging cameras or thermocouples to measure actual temperatures on the PCB during testing.
-
Conduct accelerated life testing or stress testing to assess the long-term reliability of the PCB under high-current conditions.
By thoroughly analyzing and testing the PCB design, designers can identify and address any current capacity issues before finalizing the design, ensuring a robust and reliable product.
FAQ
Q1: What is PCB current capacity, and why is it important?
A1: PCB current capacity refers to the maximum amount of current that a copper trace on a printed circuit board can safely carry without overheating or suffering damage. It is important because insufficient current capacity can lead to issues like excessive voltage drop, damaged traces, component failure, and even fire hazards.
Q2: What factors affect PCB trace current capacity?
A2: Several factors influence a PCB trace’s current capacity, including trace width, copper thickness (weight), ambient temperature, allowed temperature rise, via size and number of vias, and the presence of thermal relief or heat sinks.
Q3: How can I increase the current capacity of PCB traces?
A3: There are several methods to increase PCB trace current capacity, such as increasing trace width, using thicker copper layers, utilizing multiple layers, optimizing ambient temperature, allowing for temperature rise, using thermal relief pads, implementing heat sinks, optimizing trace routing, and using vias for heat dissipation.
Q4: What are thermal relief pads, and how do they help with current capacity?
A4: Thermal relief pads, also known as thermal spokes, are a design technique used to improve heat dissipation and increase current capacity in PCB traces connected to high-current components. They consist of a larger copper area surrounding the component pad, with several thin traces (spokes) connecting the pad to the larger copper area, allowing for better heat dissipation.
Q5: Why is thorough analysis and testing important for ensuring PCB current capacity?
A5: Thorough analysis and testing are crucial for ensuring that the PCB design meets the required current capacity and reliability standards. This includes using design software with current capacity calculators, performing thermal simulations and power integrity analysis, conducting prototype testing under realistic conditions, and using thermal imaging or thermocouples to measure actual temperatures. By identifying and addressing any current capacity issues before finalizing the design, designers can ensure a robust and reliable product.
No responses yet