What is a 10 Layer PCB?
A 10 layer PCB is a printed circuit board that consists of ten conductive layers laminated together with insulating material. These layers are interconnected using vias, which are small holes drilled through the board and plated with conductive material. The increased number of layers allows for more complex designs, higher component density, and improved signal integrity compared to simpler PCBs.
Advantages of Using a 10 Layer PCB
- Higher component density
- Improved signal integrity
- Better thermal management
- Reduced electromagnetic interference (EMI)
- Increased design flexibility
Factors to Consider When Choosing a 10 Layer PCB Manufacturer
1. Technical Capabilities
When selecting a 10 layer PCB manufacturer, it is essential to assess their technical capabilities. Look for a manufacturer that has experience in producing complex, multi-layer PCBs and has the necessary equipment and expertise to handle your project. Some key technical aspects to consider include:
- Minimum trace width and spacing
- Via size and type (blind, buried, or through-hole)
- Material selection (FR-4, high-frequency laminates, etc.)
- Surface finish options (HASL, ENIG, OSP, etc.)
- Impedance control
- Blind and buried via capabilities
2. Quality Control and Certifications
Quality control is critical in PCB manufacturing, especially for complex designs like 10 layer PCBs. Ensure that the manufacturer you choose has a robust quality control process in place and holds relevant certifications, such as:
- ISO 9001 (Quality Management System)
- ISO 14001 (Environmental Management System)
- UL (Underwriters Laboratories)
- IPC (Association Connecting Electronics Industries) standards
3. Turnaround Time and Flexibility
In today’s fast-paced market, turnaround time is a crucial factor in choosing a PCB manufacturer. Look for a manufacturer that can provide quick turnaround times without compromising on quality. Additionally, consider their flexibility in accommodating changes or revisions to your design, as well as their ability to handle both prototyping and large-scale production.
4. Cost and Shipping
Cost is always a consideration when choosing a PCB manufacturer. However, it is essential to balance cost with quality and reliability. Compare quotes from multiple manufacturers and consider factors such as shipping costs, duties, and taxes, especially if you are working with an overseas supplier.
5. Customer Support and Communication
Effective communication is key to a successful partnership with your PCB manufacturer. Look for a manufacturer that offers excellent customer support, with knowledgeable staff who can answer your questions and provide guidance throughout the manufacturing process. Clear communication channels, such as email, phone, or a dedicated project manager, can help ensure that your project runs smoothly.
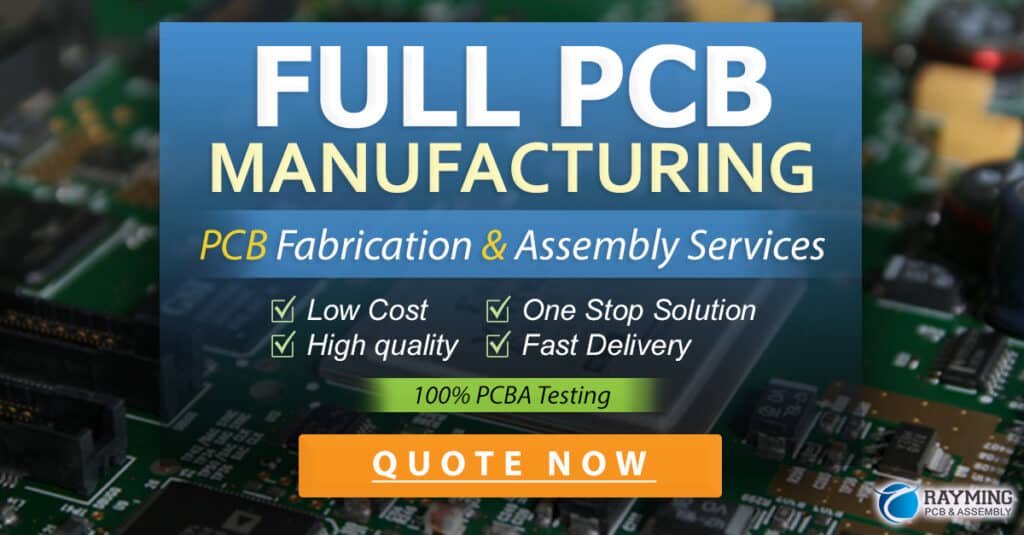
10 Layer PCB Manufacturing Process
To better understand the capabilities of a 10 layer PCB manufacturer, it is helpful to have a basic understanding of the manufacturing process. The following table outlines the key steps involved in producing a 10 layer PCB:
Step | Description |
---|---|
1. Design and Preparation | The PCB design is finalized, and the necessary files (Gerber, drill, and netlist) are prepared for manufacturing. |
2. Material Selection | The appropriate materials, such as the laminate and copper foils, are selected based on the design requirements. |
3. Inner Layer Printing | The inner layers are printed using photoresist and etched to create the desired circuit patterns. |
4. Layer Lamination | The inner layers are laminated together with insulating material and prepreg (pre-impregnated fiberglass). |
5. Drilling | Holes are drilled through the laminated board for vias and component mounting. |
6. Plating and Metallization | The drilled holes are plated with conductive material, and additional copper is added to the outer layers. |
7. Outer Layer Printing | The outer layers are printed using photoresist and etched to create the final circuit patterns. |
8. Solder Mask and Silkscreen | A solder mask is applied to protect the copper traces, and a silkscreen layer is added for component labeling. |
9. Surface Finish | The chosen surface finish (e.g., HASL, ENIG, or OSP) is applied to the PCB to protect the copper and enhance solderability. |
10. Electrical Testing | The completed PCB is electrically tested to ensure proper functionality and adherence to the design specifications. |
Frequently Asked Questions (FAQ)
- What is the minimum trace width and spacing for a 10 layer PCB?
-
The minimum trace width and spacing depend on the PCB manufacturer’s capabilities and the design requirements. Typically, a 10 layer PCB can accommodate trace widths as small as 3-4 mils (0.075-0.1 mm) and spacing of 3-4 mils.
-
Can a 10 layer PCB have blind and buried vias?
-
Yes, a 10 layer PCB can incorporate blind and buried vias. Blind vias connect an outer layer to an inner layer, while buried vias connect inner layers without reaching the outer layers. These via types can help optimize space and improve signal integrity.
-
What materials are commonly used for 10 layer PCBs?
-
The most common base material for 10 layer PCBs is FR-4, a flame-retardant fiberglass-reinforced epoxy laminate. For high-frequency or high-speed applications, speciality materials like Rogers or Isola laminates may be used.
-
How long does it typically take to manufacture a 10 layer PCB?
-
The turnaround time for a 10 layer PCB depends on the manufacturer and the complexity of the design. Prototype quantities may take 2-3 weeks, while larger production runs can take 4-6 weeks or more.
-
Are there any special considerations for designing a 10 layer PCB?
- When designing a 10 layer PCB, it is essential to consider signal integrity, impedance control, and thermal management. Work closely with your PCB manufacturer to ensure that your design is optimized for manufacturability and performance.
Conclusion
Choosing the right 10 layer PCB manufacturer is essential for the success of your electronics project. By considering factors such as technical capabilities, quality control, turnaround time, cost, and customer support, you can select a manufacturer that meets your specific needs. Understanding the manufacturing process and the special considerations for 10 layer PCBs can also help you make informed decisions and ensure a smooth collaboration with your chosen PCB manufacturer.
No responses yet