Introduction to 10-layer PCB Fabrication
In today’s world of advanced electronics, printed circuit boards (PCBs) have become increasingly complex, with a growing demand for high-density interconnects and superior performance. 10-layer PCB fabrication is a sophisticated process that enables the creation of highly complex and reliable PCBs for various applications, including aerospace, military, medical, and telecommunications.
This article will delve into the intricacies of 10-layer PCB fabrication, exploring the materials, design considerations, manufacturing processes, and quality control measures involved in creating these advanced circuit boards. By understanding the best practices and techniques employed in 10-layer PCB fabrication, you can ensure that your PCBs meet the highest standards of quality and reliability.
What is a 10-layer PCB?
A 10-layer PCB is a printed circuit board that consists of ten conductive layers, separated by insulating materials. These layers are strategically designed to route signals, power, and ground planes, allowing for high-density interconnects and improved signal integrity.
The typical structure of a 10-layer PCB is as follows:
Layer | Description |
---|---|
1 | Top layer (signal) |
2 | Ground plane |
3 | Signal layer |
4 | Power plane |
5 | Signal layer |
6 | Signal layer |
7 | Power plane |
8 | Signal layer |
9 | Ground plane |
10 | Bottom layer (signal) |
The use of multiple layers allows for a higher density of components and traces, enabling the creation of complex circuits in a compact form factor. This makes 10-layer PCBs ideal for applications that require high performance, reliability, and miniaturization.
Advantages of 10-layer PCB Fabrication
10-layer PCB fabrication offers several advantages over traditional PCB manufacturing methods:
-
High-density interconnects: With ten layers available for routing, designers can achieve a higher density of components and traces, enabling the creation of complex circuits in a smaller form factor.
-
Improved signal integrity: The strategic placement of power and ground planes helps to reduce electromagnetic interference (EMI) and crosstalk, ensuring better signal integrity and overall performance.
-
Enhanced thermal management: Multiple layers allow for better heat dissipation, as the copper planes can act as heat sinks, drawing heat away from components and preventing thermal issues.
-
Increased reliability: 10-layer PCBs are built using advanced manufacturing techniques and materials, resulting in a more robust and reliable final product.
-
Cost-effective for complex designs: While the initial cost of 10-layer PCB fabrication may be higher than simpler designs, it can be more cost-effective in the long run for complex projects that would otherwise require multiple boards or larger form factors.
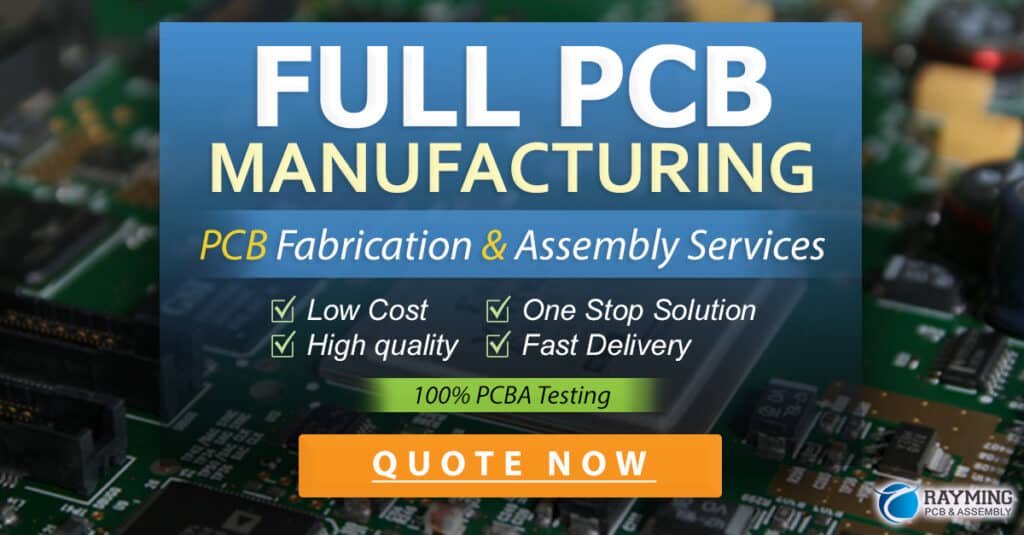
Design Considerations for 10-layer PCBs
Designing a 10-layer PCB requires careful consideration of several factors to ensure optimal performance and manufacturability. Some key design considerations include:
1. Layer Stack-up
The arrangement of signal, power, and ground layers in a 10-layer PCB is crucial for maintaining signal integrity and reducing EMI. A well-designed layer stack-up should:
- Alternate signal layers with power and ground planes to minimize crosstalk and EMI
- Use thicker dielectric materials between power and ground layers to increase capacitance and reduce power supply noise
- Place sensitive signals on inner layers, surrounded by ground planes, to provide shielding
2. Via Management
Vias are essential for connecting traces across different layers in a 10-layer PCB. However, they can also introduce signal integrity issues if not managed properly. To optimize via usage:
- Use blind and buried vias to minimize the number of through-hole vias and reduce signal path length
- Ensure proper via spacing and hole size to maintain signal integrity and manufacturability
- Employ via stitching techniques to create uninterrupted ground and power planes
3. Trace Width and Spacing
Controlling trace width and spacing is critical for maintaining signal integrity and preventing crosstalk in a 10-layer PCB. Designers should:
- Use appropriate trace widths based on the current requirements and impedance targets
- Maintain adequate spacing between traces to minimize crosstalk, especially on high-speed signal layers
- Follow manufacturer guidelines for minimum trace width and spacing to ensure manufacturability
4. Impedance Control
Maintaining consistent impedance throughout the PCB is essential for ensuring signal integrity and preventing reflections. To achieve proper impedance control:
- Use controlled-impedance design techniques, such as strip line or microstrip, for critical signal traces
- Specify the target impedance and tolerance for each signal layer
- Work closely with the PCB fabricator to ensure that the manufactured board meets the specified impedance requirements
Manufacturing Process for 10-layer PCBs
The manufacturing process for 10-layer PCBs involves several steps, each requiring precision and attention to detail. The main stages of 10-layer PCB fabrication include:
1. Material Selection
Choosing the right materials is crucial for ensuring the quality and reliability of a 10-layer PCB. The most common materials used in 10-layer PCB fabrication are:
- Copper foil: Used for the conductive layers, with thicknesses ranging from 0.5 oz to 2 oz per square foot
- Prepreg: A partially cured fiberglass material used as an insulating layer between the conductive layers
- Core: A fully cured fiberglass material used as a base for the outer layers and to provide structural stability
2. Inner Layer Processing
The inner layers of a 10-layer PCB are processed first, using the following steps:
- Cleaning: The copper foil is cleaned to remove any contaminants
- Dry film lamination: A photosensitive dry film is applied to the copper foil
- Exposure and development: The dry film is exposed to UV light through a photomask and then developed, creating the desired trace pattern
- Etching: The exposed copper is etched away, leaving only the desired traces
- Inspection: The inner layers are inspected for any defects or inconsistencies
3. Lamination
Once the inner layers are processed, they are laminated together with the prepreg and core materials using heat and pressure. This process bonds the layers together, creating a solid, multilayer structure.
4. Drilling and Plating
After lamination, the 10-layer PCB undergoes drilling and plating:
- Drilling: Holes are drilled through the PCB for vias and component leads
- Desmear: The drilled holes are cleaned to remove any debris and improve adhesion
- Electroless copper plating: A thin layer of copper is deposited onto the hole walls to provide a conductive surface
- Electrolytic copper plating: Additional copper is electroplated onto the hole walls to increase the thickness and improve conductivity
5. Outer Layer Processing
The outer layers of the 10-layer PCB are processed using steps similar to the inner layer processing, including dry film lamination, exposure, development, and etching.
6. Surface Finishing
To protect the exposed copper and improve solderability, a surface finish is applied to the 10-layer PCB. Common surface finishes include:
- HASL (Hot Air Solder Leveling): A tin-lead alloy is applied to the copper surfaces and then leveled using hot air
- ENIG (Electroless Nickel Immersion Gold): A layer of nickel is deposited onto the copper, followed by a thin layer of gold
- OSP (Organic Solderability Preservative): An organic compound is applied to the copper to prevent oxidation and maintain solderability
7. Solder Mask and Silkscreen
A solder mask is applied to the 10-layer PCB to protect the traces and prevent solder bridges during assembly. The solder mask is typically applied using a silkscreen process, which also allows for the addition of text and symbols for component placement and identification.
Quality Control and Testing
To ensure the highest quality and reliability, 10-layer PCBs undergo rigorous quality control and testing procedures. Some common quality control measures include:
- Visual inspection: The PCBs are visually inspected for any defects, such as scratches, dents, or discoloration
- Automated optical inspection (AOI): An automated system scans the PCBs for any missing or incorrect features, such as traces or vias
- Electrical testing: The PCBs are tested for continuity, resistance, and isolation to ensure proper electrical performance
- Microsectioning: A sample of the PCBs is cross-sectioned and examined under a microscope to verify the integrity of the internal layers and plating
- Thermal cycling: The PCBs are subjected to temperature variations to ensure they can withstand the expected operating conditions
- Impedance testing: The impedance of the controlled-impedance layers is measured to verify that they meet the specified requirements
By implementing these quality control measures, manufacturers can ensure that the 10-layer PCBs meet the highest standards of quality and reliability.
Choosing a 10-layer PCB Fabrication Partner
Selecting the right 10-layer PCB fabrication partner is essential for ensuring the success of your project. When evaluating potential partners, consider the following factors:
- Experience and expertise: Look for a manufacturer with a proven track record of successfully producing 10-layer PCBs for a variety of industries and applications
- State-of-the-art equipment: Ensure that the manufacturer has invested in the latest equipment and technology to produce high-quality 10-layer PCBs
- Quality certifications: Choose a manufacturer that holds relevant quality certifications, such as ISO 9001, AS9100, or IATF 16949, depending on your industry requirements
- Technical support: Select a partner that offers comprehensive technical support, from design assistance to troubleshooting, to help you navigate the complexities of 10-layer PCB fabrication
- Flexibility and scalability: Work with a manufacturer that can accommodate your specific requirements and scale production to meet your needs, from prototyping to high-volume production
By partnering with a reputable and experienced 10-layer PCB fabrication company, you can ensure that your PCBs are manufactured to the highest standards of quality and reliability.
Frequently Asked Questions (FAQ)
-
What is the typical turnaround time for 10-layer PCB fabrication?
The turnaround time for 10-layer PCB fabrication can vary depending on the complexity of the design, the manufacturer’s workload, and the specific requirements of the project. Typically, the lead time for 10-layer PCBs ranges from 2 to 4 weeks, but expedited services may be available for urgent projects. -
How much does 10-layer PCB fabrication cost?
The cost of 10-layer PCB fabrication depends on several factors, including the size of the board, the number of units ordered, the materials used, and the specific manufacturing requirements. In general, 10-layer PCBs are more expensive than simpler designs due to the increased complexity and the use of advanced manufacturing techniques. However, for complex projects, 10-layer PCBs can be more cost-effective in the long run compared to using multiple boards or larger form factors. -
What are the minimum trace width and spacing requirements for 10-layer PCBs?
The minimum trace width and spacing requirements for 10-layer PCBs can vary depending on the manufacturer’s capabilities and the specific design requirements. As a general guideline, the minimum trace width and spacing for 10-layer PCBs are typically around 0.003 inches (0.076 mm) to 0.005 inches (0.127 mm). However, it is essential to consult with your chosen manufacturer to determine their specific capabilities and guidelines. -
Can 10-layer PCBs be used for high-frequency applications?
Yes, 10-layer PCBs are well-suited for high-frequency applications, such as RF and microwave circuits. The use of multiple layers allows for the strategic placement of power and ground planes, which helps to reduce EMI and maintain signal integrity. Additionally, the ability to control impedance and use advanced materials, such as low-loss dielectrics, makes 10-layer PCBs an excellent choice for high-frequency applications. -
How can I ensure the manufacturability of my 10-layer PCB design?
To ensure the manufacturability of your 10-layer PCB design, it is essential to follow best practices and guidelines throughout the design process. This includes adhering to the manufacturer’s minimum trace width and spacing requirements, using appropriate via sizes and spacing, and properly managing the layer stack-up. It is also crucial to communicate with your chosen manufacturer early in the design process to discuss any specific requirements or constraints and to incorporate their feedback into your design. By working closely with your manufacturer and following industry best practices, you can help ensure the manufacturability and success of your 10-layer PCB project.
Conclusion
10-layer PCB fabrication is a complex and sophisticated process that enables the creation of high-density, high-performance printed circuit boards for a wide range of applications. By understanding the materials, design considerations, manufacturing processes, and quality control measures involved in 10-layer PCB fabrication, you can ensure that your PCBs meet the highest standards of quality and reliability.
When embarking on a 10-layer PCB project, it is essential to partner with an experienced and reputable manufacturer that can provide the expertise, state-of-the-art equipment, and technical support needed to bring your design to life. By working closely with your chosen manufacturer and following industry best practices, you can navigate the complexities of 10-layer PCB fabrication and achieve success in your advanced electronics projects.
No responses yet