Visual Inspection
Visual inspection is the most basic and commonly used method for checking soldering defects on PCBs. It involves examining the soldered joints and components on the PCB with the naked eye or using magnifying tools such as a magnifying glass or microscope. Here are some key things to look for during a visual inspection:
Solder Bridges
Solder bridges occur when excess solder connects two or more adjacent pads or traces that should not be connected. This can cause short circuits and lead to malfunctions or damage to the PCB. Look for any shiny, reflective connections between pads or traces that shouldn’t be there.
Cold Solder Joints
Cold solder joints occur when the solder does not melt and flow properly during the soldering process, resulting in a dull, grainy appearance. This can be caused by insufficient heat, improper cleaning, or contamination of the solder or surfaces. Cold solder joints can lead to poor electrical connections and reliability issues.
Insufficient Solder
Insufficient solder occurs when there is not enough solder to properly connect the component lead to the pad. This can result in a weak or intermittent connection that may fail over time. Look for solder joints that appear concave or have gaps between the lead and pad.
Excess Solder
Excess solder occurs when too much solder is applied to a joint, which can lead to solder bridges or obscure the view of the joint, making it difficult to inspect for other defects. Look for solder joints that appear bulbous or have solder spillover onto adjacent pads or traces.
Component Placement
Check that all components are properly placed and aligned on the PCB. Look for components that are skewed, off-center, or not flush with the board surface. Misaligned components can lead to poor solder connections and mechanical stress on the board.
Automated Optical Inspection (AOI)
Automated Optical Inspection (AOI) is a computer-based system that uses cameras and image processing software to automatically inspect PCBs for soldering defects. AOI systems can quickly scan the entire PCB and identify defects such as solder bridges, insufficient solder, and component placement issues. Some advantages of AOI include:
- High-speed inspection: AOI systems can inspect hundreds of PCBs per hour, much faster than manual inspection.
- Consistent and objective: AOI systems use predefined inspection criteria and are not subject to human error or fatigue.
- Data collection: AOI systems can collect data on defect types and locations, which can be used for process improvement and quality control.
However, AOI systems can be expensive to implement and may require specialized programming and maintenance. They also may not be able to detect certain types of defects, such as cold solder joints or hidden defects under components.
X-Ray Inspection
X-ray inspection is a non-destructive testing method that uses X-rays to create images of the internal structure of the PCB, including the solder joints and components. X-ray inspection can detect defects that are not visible on the surface, such as:
- Voids: Gaps or air pockets within the solder joint that can weaken the connection and lead to failure over time.
- Insufficient solder: Solder joints that appear normal on the surface but have insufficient solder underneath the component lead.
- Solder balls: Small balls of solder that can break off and cause short circuits or other issues.
X-ray inspection can be performed using 2D or 3D imaging techniques, depending on the level of detail required. However, X-ray equipment can be expensive and requires specialized training to operate and interpret the images.
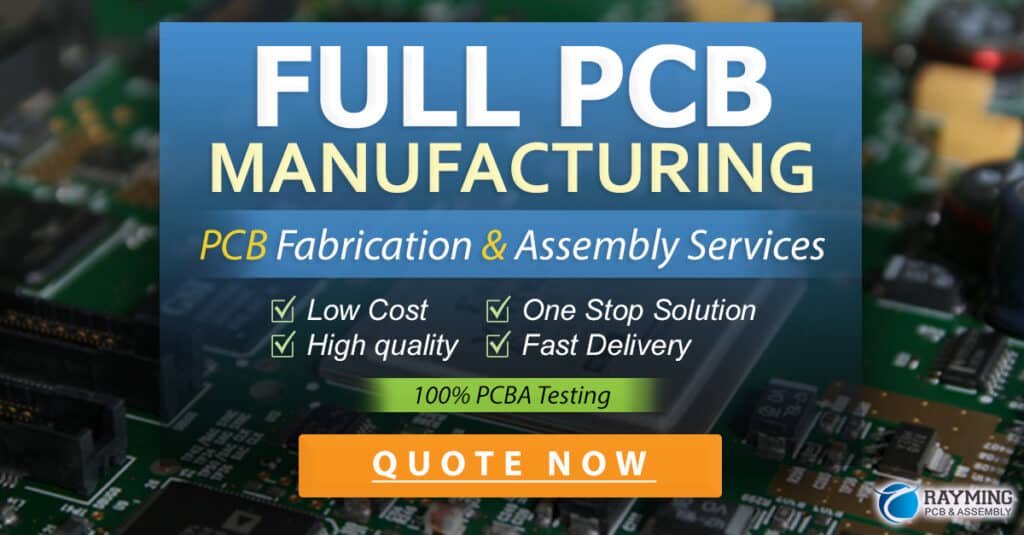
Electrical Testing
Electrical testing involves applying electrical signals to the PCB and measuring the response to verify that the board is functioning as intended. There are several types of electrical tests that can be used to detect soldering defects:
Continuity Testing
Continuity testing checks that there is a continuous electrical path between two points on the PCB. This can be used to detect open circuits caused by insufficient solder or broken connections. A multimeter or continuity tester is used to measure the resistance between two points, which should be close to zero for a good connection.
Insulation Resistance Testing
Insulation resistance testing checks the resistance between two points that should be electrically isolated, such as adjacent traces or pads. This can detect short circuits caused by solder bridges or other conductive defects. An insulation resistance tester applies a high voltage between the points and measures the resistance, which should be very high (typically in the megaohm range) for good insulation.
In-Circuit Testing (ICT)
In-Circuit Testing (ICT) involves using a specialized test fixture to make electrical contact with each node on the PCB and measure its electrical characteristics, such as resistance, capacitance, and voltage. ICT can detect a wide range of soldering defects, including open and short circuits, incorrect component values, and missing or misaligned components. However, ICT requires a custom test fixture for each PCB design and can be time-consuming and expensive to set up.
Thermal Imaging
Thermal imaging uses an infrared camera to create a heat map of the PCB during operation. This can detect soldering defects that generate excess heat, such as:
- High-resistance solder joints: Solder joints with high electrical resistance generate more heat than normal joints, which can be detected by thermal imaging.
- Overheating components: Components that are not properly soldered or are damaged can generate excess heat, which can be detected by thermal imaging.
Thermal imaging can be performed on a powered PCB in normal operation or during specialized thermal stress testing. However, thermal imaging equipment can be expensive and requires specialized training to interpret the images.
Microsectioning
Microsectioning is a destructive testing method that involves cutting a cross-section of the PCB and examining it under a microscope. This can provide detailed information on the internal structure of the solder joints, including:
- Intermetallic compound (IMC) formation: The formation of IMC layers between the solder and the component lead or pad is essential for a strong and reliable solder joint. Microsectioning can measure the thickness and quality of the IMC layers.
- Grain structure: The grain structure of the solder can affect its mechanical strength and reliability. Microsectioning can reveal the grain size, shape, and orientation of the solder.
- Voids and cracks: Microsectioning can detect internal voids, cracks, or other defects that may not be visible on the surface.
However, microsectioning is a destructive test that requires specialized equipment and sample preparation, and can only be performed on a small number of samples.
Solderability Testing
Solderability testing evaluates the ability of a component lead or PCB pad to be wetted by molten solder and form a reliable solder joint. Poor solderability can lead to weak or defective solder joints, even if the soldering process is performed correctly. Solderability can be affected by factors such as:
- Surface contamination: Oxidation, dirt, or other contaminants on the surface can prevent the solder from wetting and bonding properly.
- Surface roughness: A rough or uneven surface can prevent the solder from flowing and spreading evenly.
- Surface finish: Different surface finishes (such as HASL, OSP, or ENIG) can have different solderability characteristics.
Solderability testing typically involves dipping the component lead or PCB pad in a bath of molten solder and measuring the wetting angle, wetting time, and other parameters. There are several standard test methods for solderability testing, such as:
- Wetting balance test: Measures the wetting force and time as the component lead is dipped in and withdrawn from the solder bath.
- Globule test: Measures the size and shape of a solder globule formed on the end of the component lead after dipping.
- Edge dip test: Measures the wetting angle and distance as the edge of the PCB is dipped in the solder bath.
Solderability testing can be performed on individual components or PCBs before assembly to ensure that they are compatible with the soldering process and will form reliable solder joints.
Acoustic Microscopy
Acoustic microscopy is a non-destructive testing method that uses high-frequency sound waves to create images of the internal structure of the PCB, including the solder joints and components. Acoustic microscopy can detect defects such as:
- Delamination: Separation of the layers of the PCB or component package, which can lead to cracking or failure under stress.
- Voids: Gaps or air pockets within the solder joint or component package that can weaken the connection and lead to failure over time.
- Cracks: Fractures or breaks in the solder joint or component package that can cause electrical or mechanical failure.
Acoustic microscopy works by sending a focused beam of high-frequency sound waves into the PCB and measuring the reflections and scattering from the internal interfaces and defects. The reflected signals are processed to create a 2D or 3D image of the internal structure, with defects appearing as anomalies in the image.
Acoustic microscopy can be performed on both bare PCBs and assembled PCBs, and can image through optically opaque materials such as solder mask or component packaging. However, acoustic microscopy equipment can be expensive and requires specialized training to operate and interpret the images.
Dye Penetrant Testing
Dye penetrant testing is a non-destructive testing method that uses a colored dye to highlight surface defects on the PCB or component. The dye is applied to the surface and allowed to penetrate into any cracks, voids, or other defects. The excess dye is then removed and a developer solution is applied to draw the dye out of the defects, making them visible as colored indications on the surface.
Dye penetrant testing can detect surface defects such as:
- Cracks: Fractures or breaks in the solder joint or component lead that can cause electrical or mechanical failure.
- Porosity: Small holes or voids in the solder joint or component lead that can weaken the connection and lead to failure over time.
- Incomplete fusion: Lack of complete bonding between the solder and the component lead or PCB pad, which can lead to a weak or unreliable connection.
Dye penetrant testing is relatively simple and inexpensive to perform and can be used on a wide range of materials, including metals, ceramics, and plastics. However, it can only detect surface defects and may not be suitable for detecting internal defects or defects on complex or irregular surfaces.
Functional Testing
Functional testing involves testing the PCB under its intended operating conditions to verify that it functions as intended. This can include:
- Power-on testing: Applying power to the PCB and verifying that it starts up and operates correctly.
- Signal integrity testing: Measuring the quality and timing of the electrical signals on the PCB to ensure that they meet the required specifications.
- Environmental testing: Exposing the PCB to various environmental conditions (such as temperature, humidity, vibration, or shock) to verify that it can operate reliably under those conditions.
Functional testing can detect a wide range of soldering defects that may not be detectable by other methods, such as:
- Intermittent connections: Solder joints that make and break contact intermittently due to mechanical stress or thermal cycling.
- Signal integrity issues: Solder joints that distort or degrade the electrical signals passing through them, leading to errors or malfunctions.
- Environmental failures: Solder joints that fail or degrade under certain environmental conditions, such as high temperature or vibration.
Functional testing typically requires specialized test equipment and fixtures, and may need to be customized for each PCB design. It is often performed as part of the final acceptance testing of the PCB before it is shipped to the customer.
Frequently Asked Questions (FAQ)
What are the most common soldering defects on PCBs?
Some of the most common soldering defects on PCBs include:
- Solder bridges: Excess solder that connects adjacent pads or traces, causing a short circuit.
- Cold solder joints: Solder joints that have not been heated sufficiently, resulting in a weak or unreliable connection.
- Insufficient solder: Not enough solder applied to the joint, resulting in a weak or open connection.
- Excess solder: Too much solder applied to the joint, obscuring the view of the joint and potentially causing short circuits.
- Component misalignment: Components that are not properly positioned or oriented on the PCB, leading to poor solder connections or mechanical stress.
Can all soldering defects be detected by visual inspection?
No, not all soldering defects can be detected by visual inspection alone. Some defects, such as internal voids, cracks, or insufficient solder under the component, may not be visible on the surface. Other methods, such as X-ray inspection, acoustic microscopy, or electrical testing, may be needed to detect these types of defects.
What is the difference between destructive and non-destructive testing?
Destructive testing involves methods that permanently alter or damage the PCB or component being tested, such as microsectioning or solderability testing. Non-destructive testing involves methods that do not alter or damage the PCB or component, such as visual inspection, X-ray inspection, or electrical testing.
How can soldering defects be prevented?
Soldering defects can be prevented by following good soldering practices and process controls, such as:
- Using clean and properly prepared surfaces and components.
- Using the correct solder alloy and flux for the application.
- Controlling the temperature and time of the soldering process.
- Using appropriate soldering equipment and techniques for the component and PCB design.
- Implementing quality control measures, such as visual inspection, AOI, or electrical testing, to catch defects early in the process.
What are the consequences of soldering defects on PCBs?
Soldering defects on PCBs can have a range of consequences, depending on the type and severity of the defect, such as:
- Reduced reliability: Weak or intermittent solder connections can fail over time, leading to malfunctions or complete failure of the PCB.
- Reduced performance: Poor solder connections can degrade the electrical signals passing through them, leading to errors, noise, or other performance issues.
- Safety hazards: Short circuits or other electrical faults caused by soldering defects can pose a safety hazard, such as fire or electric shock.
- Increased costs: Rework or repair of soldering defects can be time-consuming and expensive, and may not always be possible or effective.
- Damage to reputation: Shipping products with soldering defects can damage a company’s reputation and lead to customer dissatisfaction and lost business.
Defect Type | Visual Inspection | AOI | X-Ray | Electrical Testing | Thermal Imaging | Microsectioning | Solderability Testing | Acoustic Microscopy | Dye Penetrant Testing | Functional Testing |
---|---|---|---|---|---|---|---|---|---|---|
Solder Bridges | Yes | Yes | No | Yes | No | No | No | No | No | Yes |
Cold Solder Joints | Yes | No | No | Yes | Yes | Yes | No | No | No | Yes |
Insufficient Solder | Yes | Yes | Yes | Yes | No | Yes | No | No | No | Yes |
Excess Solder | Yes | Yes | No | No | No | No | No | No | No | Yes |
Component Misalignment | Yes | Yes | No | No | No | No | No | No | No | Yes |
Voids | No | No | Yes | No | No | Yes | No | Yes | No | Yes |
Cracks | No | No | No | Yes | No | Yes | No | Yes | Yes | Yes |
Delamination | No | No | No | No | No | Yes | No | Yes | No | Yes |
Incomplete Fusion | No | No | No | Yes | No | Yes | Yes | No | Yes | Yes |
Signal Integrity Issues | No | No | No | Yes | No | No | No | No | No | Yes |
The table above summarizes the capabilities of each testing method for detecting different types of soldering defects on PCBs. It can be seen that no single method can detect all types of defects, and a combination of methods may be needed for comprehensive testing and quality control.
In conclusion, soldering defects on PCBs can have serious consequences for the reliability, performance, and safety of electronic products. Effective methods for checking and identifying these defects are essential for ensuring the quality and integrity of PCBs. The 10 methods discussed in this article – visual inspection, AOI, X-ray inspection, electrical testing, thermal imaging, microsectioning, solderability testing, acoustic microscopy, dye penetrant testing, and functional testing – provide a range of options for detecting different types of defects at different stages of the PCB manufacturing process. By implementing appropriate testing and quality control measures, manufacturers can minimize the
No responses yet