Introduction
When it comes to assembling printed circuit boards (PCBs), there are two main methods used in the electronics manufacturing industry: through hole assembly and surface mount technology (SMT) assembly. Both techniques have their advantages and disadvantages, and the choice between them depends on various factors such as the complexity of the circuit, the size of the components, the production volume, and the cost. In this article, we will explore the key differences between through hole and SMT assembly to help you make an informed decision for your next PCB project.
What is Through Hole Assembly?
Through hole assembly, also known as through hole technology (THT), is the traditional method of mounting electronic components on a PCB. In this technique, the components have long leads that are inserted into drilled holes on the board and soldered to pads on the opposite side. The holes act as conduits for the electrical and mechanical connection between the component and the board.
Advantages of Through Hole Assembly
-
Mechanical strength: Through hole components are physically attached to the board with their leads, providing a strong and reliable mechanical connection that can withstand vibration, shock, and thermal stress.
-
Easy to repair: If a through hole component fails, it can be easily removed and replaced using a soldering iron, making repairs and modifications relatively simple.
-
Suitable for high-power applications: Through hole components can handle higher power and current than their SMT counterparts, making them ideal for power supply circuits and high-voltage applications.
Disadvantages of Through Hole Assembly
-
Larger footprint: Through hole components require drilled holes and larger pads on the board, resulting in a larger footprint compared to SMT components. This limits the density of the circuit and the miniaturization of the device.
-
Manual assembly: Through hole components are typically inserted and soldered manually, which is a time-consuming and labor-intensive process. This limits the production speed and increases the cost of assembly.
-
Limited component selection: Not all electronic components are available in through hole packages, especially the newer and more advanced ones. This limits the design options and the performance of the circuit.
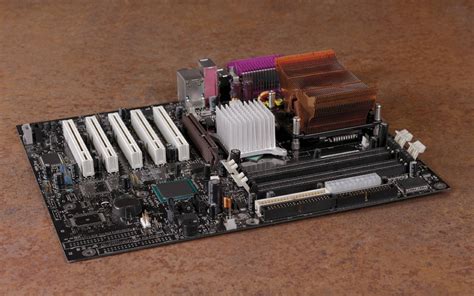
What is SMT Assembly?
Surface mount technology (SMT) assembly is a modern method of mounting electronic components directly onto the surface of a PCB without the need for drilled holes. In this technique, the components have small metal leads or terminals that are soldered to pads on the same side of the board. SMT components are smaller, lighter, and more compact than through hole components, enabling higher density and more complex circuits.
Advantages of SMT Assembly
-
Smaller footprint: SMT components are much smaller than through hole components, allowing for higher density and more compact circuits. This enables the miniaturization of electronic devices and the integration of more functionality into a smaller space.
-
Automated assembly: SMT components are designed for automated placement and soldering using pick-and-place machines and reflow ovens. This enables high-speed, high-volume production with consistent quality and lower labor costs.
-
Wider component selection: Most modern electronic components are available in SMT packages, providing a wider range of options for designers and enabling the use of the latest and most advanced technologies.
Disadvantages of SMT Assembly
-
Limited mechanical strength: SMT components are attached to the board only by the solder joints, which are not as strong as the through hole leads. This makes SMT circuits more susceptible to damage from mechanical stress and vibration.
-
Difficult to repair: SMT components are very small and closely spaced, making manual repair and rework challenging and requiring specialized tools and skills.
-
Thermal management: SMT components generate more heat than through hole components due to their smaller size and higher density. This requires careful thermal management and the use of heat sinks and Cooling Techniques to prevent overheating and failure.
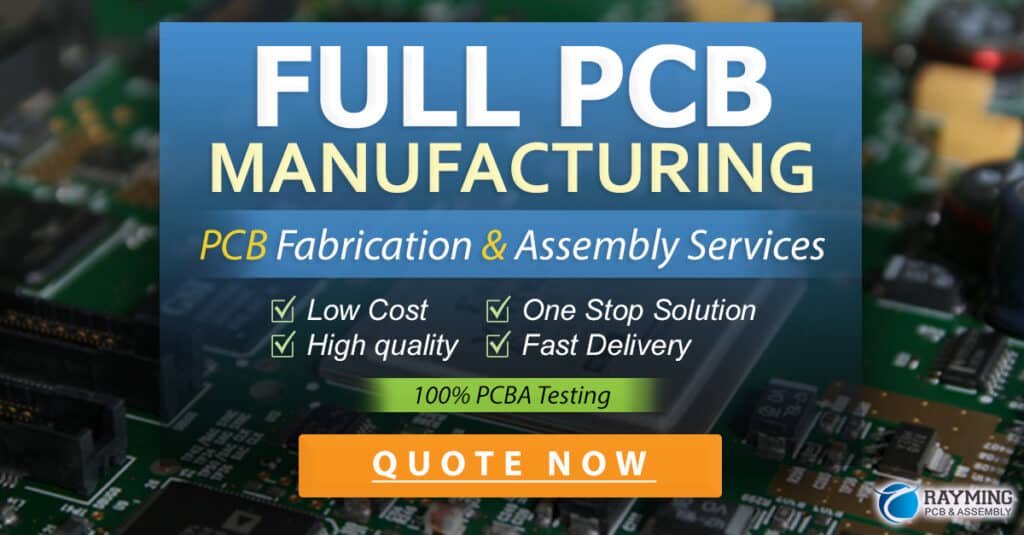
SMT vs Through-Hole: Key Differences
Factor | Through Hole Assembly | SMT Assembly |
---|---|---|
Component size | Larger, with long leads | Smaller, with short leads or terminals |
Board density | Lower, due to larger footprint and drilled holes | Higher, due to smaller footprint and no holes |
Assembly method | Manual insertion and soldering | Automated placement and soldering |
Production speed | Slower, due to manual assembly | Faster, due to automated assembly |
Labor cost | Higher, due to manual assembly | Lower, due to automated assembly |
Component selection | Limited, not all components available in through hole | Wider, most modern components available in SMT |
Mechanical strength | Stronger, due to physical attachment of leads | Weaker, due to solder joint attachment only |
Repairability | Easier, components can be removed and replaced manually | More difficult, requires specialized tools and skills |
Power handling | Higher, suitable for high-power applications | Lower, limited by smaller size and heat dissipation |
Thermal management | Easier, due to larger size and spacing of components | More challenging, due to higher density and heat generation |
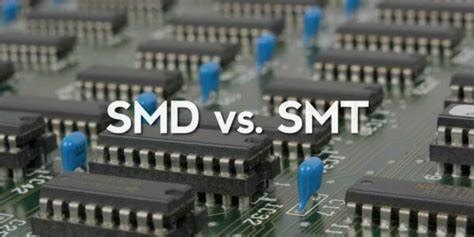
When to Use Through Hole Assembly
Through hole assembly is still used in certain applications where its advantages outweigh its disadvantages. Some scenarios where through hole assembly may be preferred include:
-
High-reliability applications: In critical applications where reliability is paramount, such as aerospace, military, and medical devices, through hole assembly provides a more robust and fail-safe connection between the components and the board.
-
High-power circuits: Power supply circuits and other high-voltage or high-current applications benefit from the higher power handling capability and thermal dissipation of through hole components.
-
Low-volume production: For small-scale or prototype production, through hole assembly may be more cost-effective than setting up an automated SMT assembly line.
-
Educational and hobby projects: Through hole components are easier to handle and solder manually, making them suitable for educational kits, hobby projects, and DIY electronics.
When to Use SMT Assembly
SMT assembly is the preferred method for most modern electronic products due to its advantages in size, speed, and cost. Some scenarios where SMT assembly is the better choice include:
-
High-volume production: For mass production of electronic devices, SMT assembly offers faster, more consistent, and more cost-effective manufacturing than through hole assembly.
-
Compact devices: Smartphones, wearables, and other miniaturized electronic products require the high density and small footprint of SMT components to fit more functionality into a smaller space.
-
High-performance circuits: Advanced electronic circuits, such as those found in computers, telecommunications equipment, and consumer electronics, benefit from the wider selection and higher performance of SMT components.
-
Cost-sensitive applications: For price-competitive products, the lower labor cost and higher automation of SMT assembly can provide significant cost savings over through hole assembly.
FAQ
1. Can through hole and SMT components be used together on the same PCB?
Yes, it is possible to use both through hole and SMT components on the same PCB in a hybrid assembly. This allows designers to take advantage of the strengths of each technology where appropriate. However, hybrid assembly requires careful planning and may increase the complexity and cost of the manufacturing process.
2. Are SMT components more expensive than through hole components?
In general, SMT components are less expensive than their through hole counterparts due to their smaller size, higher volume production, and greater availability. However, the cost of individual components can vary widely depending on the specific part, package, and supplier.
3. Can SMT components be soldered manually?
While SMT components are designed for automated assembly, they can be soldered manually using specialized tools and techniques, such as tweezers, magnifying lenses, and fine-tip soldering irons. However, manual soldering of SMT components is more challenging and time-consuming than through hole components due to their smaller size and closer spacing.
4. What is the smallest size of SMT components?
SMT components come in a wide range of sizes, from larger packages like SOICs and QFPs to smaller ones like 0402 and 0201 chip resistors and capacitors. The smallest commercially available SMT components are 01005 packages, which measure just 0.4mm x 0.2mm. However, these ultra-small components require advanced assembly equipment and are not commonly used in most applications.
5. Can through hole components be used for surface mounting?
Some through hole components can be adapted for surface mounting by bending their leads to fit the SMT pads on the board. This technique, known as “through hole technology with surface mount option” (THT-SMO), allows through hole components to be used in SMT assembly processes. However, this is not a common practice and is limited to certain types of components and applications.
Conclusion
In summary, through hole and SMT assembly are two distinct methods of mounting electronic components on a PCB, each with its own advantages and disadvantages. Through hole assembly offers greater mechanical strength, easier repairability, and higher power handling, while SMT assembly enables smaller size, faster production, and wider component selection. The choice between the two depends on the specific requirements and constraints of the application, such as reliability, density, cost, and volume. By understanding the key differences between through hole and SMT assembly, designers and manufacturers can make informed decisions and optimize their PCB assembly processes for the best results.
No responses yet