What is HASL?
HASL, or Hot Air Solder Leveling, is a traditional surface finish method that involves dipping the PCB into a molten solder bath, typically consisting of a tin-lead alloy. The excess solder is then blown off using hot air knives, leaving a thin, uniform layer of solder on the exposed copper pads and through-holes. HASL has been widely used in the electronics industry for decades due to its cost-effectiveness and good solderability.
What is ENIG?
ENIG, or Electroless Nickel Immersion Gold, is a more advanced surface finish that has gained popularity in recent years. In this process, a thin layer of nickel is first deposited onto the exposed copper surfaces through an auto-catalytic chemical reaction. This nickel layer serves as a barrier, preventing copper migration and providing a uniform surface for subsequent gold deposition. A thin layer of gold is then deposited onto the nickel surface through an immersion process, protecting the nickel from oxidation and enhancing solderability.
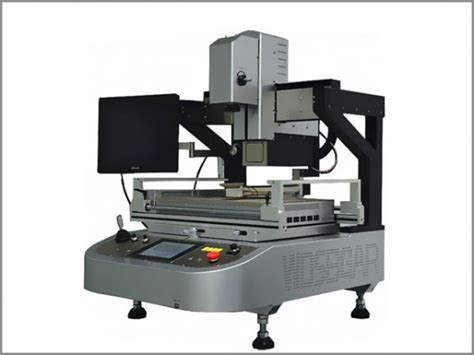
Difference 1: Surface Flatness
One of the most significant differences between HASL and ENIG lies in the surface flatness of the finished PCB.
Surface Finish | Surface Flatness |
---|---|
HASL | Less flat due to solder dipping and air leveling process |
ENIG | Excellent surface flatness, suitable for fine-pitch components |
HASL boards may exhibit slight variations in surface flatness due to the nature of the solder dipping and air leveling process. This can lead to challenges when assembling fine-pitch components or applying solder paste using stencils.
In contrast, ENIG boards offer excellent surface flatness, as the nickel and gold layers are deposited uniformly across the surface. This makes ENIG an ideal choice for applications requiring high-density component placement or precise solder paste application.
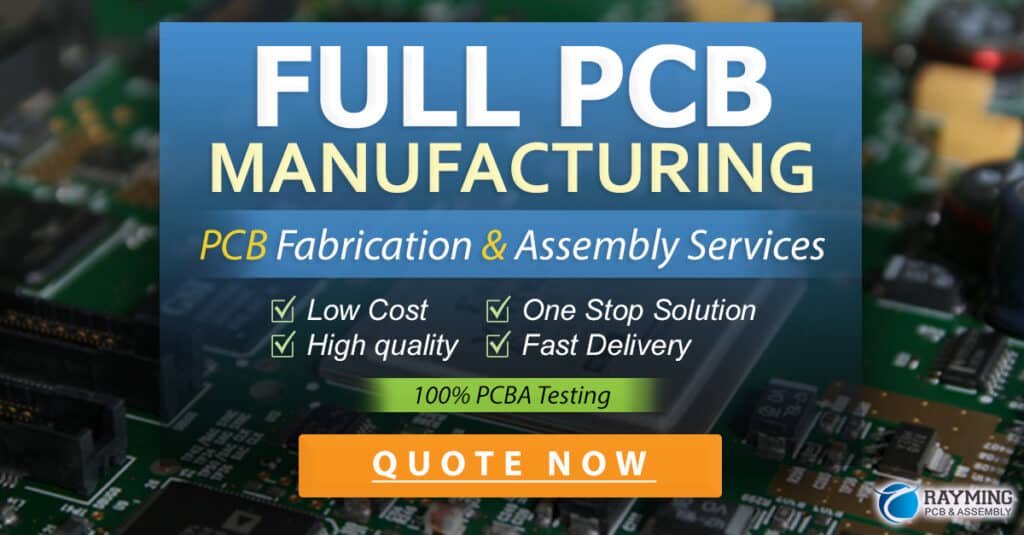
Difference 2: Shelf Life
The shelf life of PCBs is another important factor to consider when choosing between HASL and ENIG.
Surface Finish | Shelf Life |
---|---|
HASL | 12+ months |
ENIG | 6-12 months |
HASL boards typically have a longer shelf life, often exceeding 12 months, as the solder layer protects the copper from oxidation. This makes HASL a suitable choice for projects with longer storage requirements or those that may experience delays between manufacturing and assembly.
ENIG boards, on the other hand, have a shorter shelf life, usually ranging from 6 to 12 months. The thin gold layer can gradually diffuse into the nickel layer over time, leading to a decrease in solderability. It is essential to consider the expected storage duration and assembly timeline when opting for ENIG.
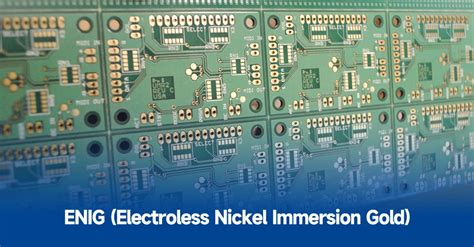
Difference 3: Solderability
Solderability refers to the ease with which solder can wet and bond to the surface of the PCB.
Surface Finish | Solderability |
---|---|
HASL | Excellent solderability due to the presence of solder on the surface |
ENIG | Good solderability, but may require higher soldering temperatures |
HASL boards exhibit excellent solderability, as the solder layer on the surface readily melts and bonds with the solder paste during the assembly process. This makes HASL a popular choice for through-hole components and hand soldering applications.
ENIG boards also offer good solderability, but the nickel and gold layers may require slightly higher soldering temperatures compared to HASL. The gold layer dissolves into the solder joint during the reflow process, while the nickel layer acts as a barrier to prevent copper migration.
Difference 4: Cost
Cost is often a deciding factor when selecting a surface finish for PCB manufacturing.
Surface Finish | Cost |
---|---|
HASL | Low cost, economical choice for many applications |
ENIG | Higher cost due to the use of nickel and gold |
HASL is generally the more cost-effective option, as it involves a simple solder dipping process and utilizes readily available materials. This makes HASL an attractive choice for budget-conscious projects or high-volume production runs.
ENIG, on the other hand, comes with a higher cost due to the use of nickel and gold in the plating process. The additional steps and materials involved contribute to the increased expense. However, the superior surface flatness, corrosion resistance, and compatibility with fine-pitch components often justify the added cost for high-end applications.
Difference 5: Solder Joint Appearance
The appearance of solder joints can vary between HASL and ENIG boards.
Surface Finish | Solder Joint Appearance |
---|---|
HASL | Shiny and slightly domed solder joints |
ENIG | Flat and matte solder joints |
HASL boards typically exhibit shiny and slightly domed solder joints due to the presence of the solder layer on the surface. This appearance is often associated with traditional PCB assembly and is easily recognizable.
ENIG boards, in contrast, produce flat and matte solder joints. The gold layer dissolves into the solder during the reflow process, resulting in a more uniform and aesthetically pleasing appearance. This can be advantageous for applications where the visual appeal of the solder joints is important.
Difference 6: Compatibility with Lead-Free Solder
The compatibility of surface finishes with lead-free solder is an important consideration, especially with the increasing adoption of RoHS (Restriction of Hazardous Substances) regulations.
Surface Finish | Compatibility with Lead-Free Solder |
---|---|
HASL | May require higher soldering temperatures and longer dwell times |
ENIG | Excellent compatibility with lead-free solder |
HASL boards may face challenges when used with lead-free solder, as lead-free alloys typically have higher melting points compared to traditional tin-lead solder. This can necessitate higher soldering temperatures and longer dwell times to achieve proper solder joint formation.
ENIG, on the other hand, exhibits excellent compatibility with lead-free solder. The nickel layer acts as a barrier, preventing the formation of brittle intermetallic compounds between the copper and the lead-free solder. This enhances the reliability and strength of the solder joints.
Difference 7: Thermal Shock Resistance
Thermal shock resistance refers to a PCB’s ability to withstand rapid temperature changes without damage.
Surface Finish | Thermal Shock Resistance |
---|---|
HASL | Good thermal shock resistance |
ENIG | Excellent thermal shock resistance due to the nickel layer |
HASL boards generally have good thermal shock resistance, as the solder layer can absorb some of the stresses induced by temperature fluctuations. However, the solder layer may be prone to cracking or delamination under extreme thermal cycling conditions.
ENIG boards offer excellent thermal shock resistance, thanks to the presence of the nickel layer. Nickel has a coefficient of thermal expansion (CTE) that is closer to that of the PCB substrate compared to solder. This helps to minimize the stresses caused by temperature changes, reducing the risk of pad lifting or solder joint failure.
Difference 8: Rework and Repair
Rework and repair are important considerations when choosing a surface finish, as they impact the ease of maintaining and modifying assembled PCBs.
Surface Finish | Rework and Repair |
---|---|
HASL | Easier to rework and repair due to the presence of solder on the surface |
ENIG | More challenging to rework and repair, may require specialized techniques |
HASL boards are generally easier to rework and repair, as the solder layer on the surface can be easily melted and resoldered. This allows for the replacement of components or the correction of assembly errors without significant difficulties.
ENIG boards, however, can be more challenging to rework and repair. The nickel and gold layers may require specialized techniques, such as using higher soldering temperatures or additional fluxes, to ensure proper solder joint formation during rework. Additionally, the thin gold layer can be easily damaged during the rework process, potentially compromising the surface finish integrity.
Difference 9: Suitability for Fine-Pitch Components
The ability to accommodate fine-pitch components is crucial for modern electronics with high-density designs.
Surface Finish | Suitability for Fine-Pitch Components |
---|---|
HASL | Limited suitability due to uneven surface and solder bridging concerns |
ENIG | Excellent suitability, enabling high-density component placement |
HASL boards may face limitations when it comes to assembling fine-pitch components. The uneven surface resulting from the solder dipping process can lead to challenges in achieving precise solder paste deposition and component placement. Additionally, the risk of solder bridging between closely spaced pads is higher with HASL.
ENIG, with its excellent surface flatness and uniform coating, is highly suitable for fine-pitch component assembly. The flat surface enables accurate solder paste printing and component placement, reducing the risk of solder bridging. This makes ENIG an ideal choice for high-density designs and applications requiring precise component alignment.
Difference 10: Environmental Impact
Environmental considerations have become increasingly important in the electronics industry, driving the need for eco-friendly manufacturing processes.
Surface Finish | Environmental Impact |
---|---|
HASL | Potential environmental concerns due to the use of lead in the solder bath |
ENIG | More environmentally friendly, compliant with RoHS regulations |
HASL, particularly when using a tin-lead solder bath, may raise environmental concerns due to the presence of lead. Lead is a hazardous substance that can have negative impacts on human health and the environment. As a result, many countries have implemented regulations, such as RoHS, to restrict the use of lead in electronics manufacturing.
ENIG, on the other hand, is considered a more environmentally friendly option. The nickel and gold plating process does not involve the use of lead, making ENIG compliant with RoHS regulations. Additionally, the elimination of the solder bath in the ENIG process reduces the generation of hazardous waste and minimizes the environmental footprint of PCB manufacturing.
FAQ
-
Q: Can HASL be used for high-density PCB designs?
A: While HASL can be used for high-density designs, it may face challenges due to the uneven surface and the risk of solder bridging. ENIG is generally preferred for high-density PCBs with fine-pitch components. -
Q: Is ENIG suitable for applications requiring frequent rework?
A: ENIG can be more challenging to rework compared to HASL, as the nickel and gold layers may require specialized techniques and higher soldering temperatures. Frequent rework on ENIG boards may compromise the surface finish integrity over time. -
Q: How does the shelf life of HASL and ENIG boards affect the assembly process?
A: HASL boards have a longer shelf life, making them suitable for projects with longer storage requirements or potential delays between manufacturing and assembly. ENIG boards have a shorter shelf life, so it is important to consider the expected storage duration and assembly timeline when choosing this surface finish. -
Q: Are there any specific handling precautions for ENIG boards?
A: ENIG boards should be handled with care to avoid scratching or damaging the gold surface. Proper storage conditions, such as controlled humidity and temperature, are important to maintain the surface finish quality and prevent oxidation. -
Q: Can HASL be used for lead-free assembly processes?
A: HASL can be used for lead-free assembly, but it may require higher soldering temperatures and longer dwell times compared to traditional tin-lead solder. It is important to optimize the soldering process parameters to ensure proper solder joint formation when using lead-free solder with HASL.
Conclusion
Choosing between HASL and ENIG surface finishes for your PCB project involves considering various factors, including surface flatness, shelf life, solderability, cost, and environmental impact. HASL offers cost-effectiveness, excellent solderability, and longer shelf life, making it suitable for many general-purpose applications. ENIG, on the other hand, provides superior surface flatness, compatibility with fine-pitch components, and better environmental compliance, making it ideal for high-density designs and lead-free assembly processes.
By understanding the key differences between HASL and ENIG, you can make an informed decision based on your specific project requirements, budget, and manufacturing constraints. Consulting with your PCB manufacturer and assembly partner can further help you determine the most suitable surface finish for your application, ensuring the reliability and performance of your final product.
No responses yet