Introduction to PCB Surface Finishes
Printed Circuit Boards (PCBs) are an essential component of modern electronics. They provide a platform for mounting and interconnecting electronic components to create a functional circuit. One crucial aspect of PCB manufacturing is the surface finish, which protects the copper traces from oxidation and enhances the solderability of the board. Two popular surface finish options are Hot Air Solder Leveling (HASL) and Electroless Nickel Immersion Gold (ENIG). In this article, we will explore the ten key differences between HASL and ENIG plating methods.
What is HASL?
Hot Air Solder Leveling (HASL) is a traditional surface finish method that has been widely used in the PCB industry for decades. The process involves dipping the PCB into a molten solder bath, typically consisting of a tin-lead alloy. The excess solder is then blown off using hot air knives, leaving a thin, uniform layer of solder on the copper traces and pads. HASL provides excellent solderability and is relatively inexpensive compared to other surface finishes.
What is ENIG?
Electroless Nickel Immersion Gold (ENIG) is a more advanced surface finish technology that has gained popularity in recent years. The process begins with the deposition of a thin layer of nickel onto the copper traces and pads through an auto-catalytic chemical reaction. This nickel layer acts as a barrier, preventing the diffusion of copper into the subsequent gold layer. The PCB is then immersed in a gold solution, which deposits a thin layer of gold onto the nickel surface. ENIG offers excellent flatness, solderability, and durability, making it suitable for high-reliability applications.
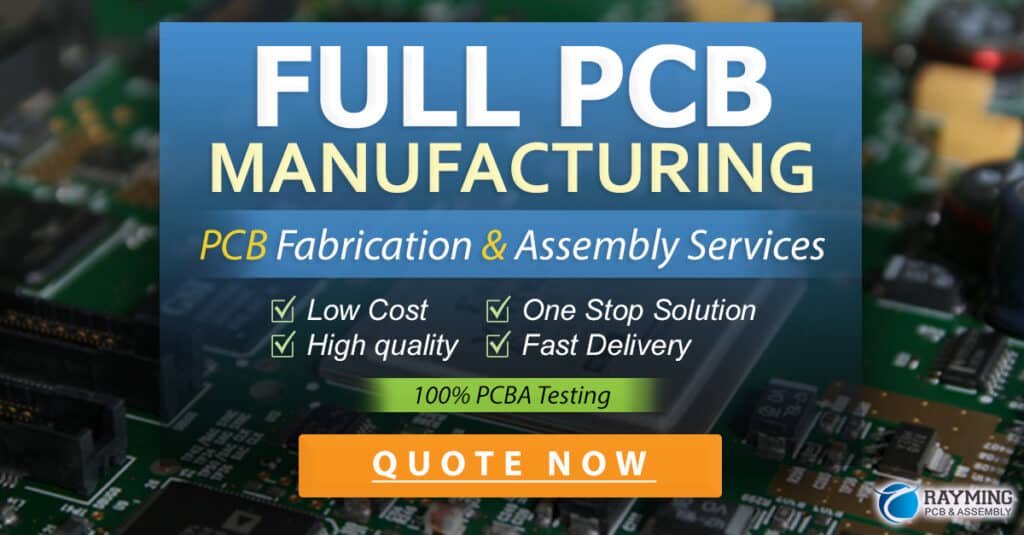
Difference 1: Flatness and Coplanarity
One of the most significant differences between HASL and ENIG is the flatness and coplanarity of the resulting surface.
HASL Flatness and Coplanarity
HASL tends to produce a slightly uneven surface due to the nature of the solder leveling process. The hot air knives used to remove excess solder can create a wavy or domed surface on the pads and traces. This unevenness can lead to issues with component placement and soldering, particularly for fine-pitch components and Ball Grid Arrays (BGAs).
ENIG Flatness and Coplanarity
In contrast, ENIG provides a much flatter and more coplanar surface. The thin layers of nickel and gold deposited during the ENIG process closely follow the contours of the copper traces and pads, resulting in a highly uniform surface. This flatness is crucial for the successful assembly of high-density and fine-pitch components, as it ensures proper contact between the component leads and the PCB pads.
Difference 2: Solderability
Both HASL and ENIG offer good solderability, but there are some differences in their performance.
HASL Solderability
HASL provides excellent solderability due to the presence of the solder layer on the surface. The solder bath used in the HASL process typically contains a tin-lead alloy, which has a lower melting point and better wetting properties compared to lead-free alloys. This makes HASL well-suited for traditional through-hole components and larger Surface Mount Technology (SMT) components.
ENIG Solderability
ENIG also offers good solderability, thanks to the presence of the gold layer. Gold is known for its excellent wetting properties and resistance to oxidation, which promotes good solder joint formation. However, the thin gold layer can dissolve quickly during the soldering process, exposing the underlying nickel. If the nickel layer is too thick or has been exposed to the environment for an extended period, it can oxidize and hinder solderability. Therefore, it is essential to control the thickness of the nickel and gold layers and to store ENIG boards properly to maintain their solderability.
Difference 3: Durability and Shelf Life
The durability and shelf life of HASL and ENIG boards can vary depending on the storage conditions and the quality of the surface finish.
HASL Durability and Shelf Life
HASL boards have a relatively long shelf life, as the solder layer protects the copper from oxidation. However, the solder surface can tarnish over time, especially if exposed to humidity or corrosive environments. Tarnished HASL surfaces may require additional cleaning or solder paste application before assembly.
ENIG Durability and Shelf Life
ENIG boards offer excellent durability and a longer shelf life compared to HASL. The gold layer provides superior protection against oxidation and corrosion, allowing ENIG boards to be stored for extended periods without significant degradation. However, the shelf life of ENIG can be affected by the quality of the nickel and gold layers. If the nickel layer is too thin or has defects, it may not provide adequate protection, leading to a shorter shelf life.
Difference 4: Cost
The cost of HASL and ENIG surface finishes can vary significantly, depending on the PCB manufacturer and the specific requirements of the project.
HASL Cost
HASL is generally the most cost-effective surface finish option, as it is a well-established process that uses relatively inexpensive materials. The solder used in the HASL process is typically a tin-lead alloy, which is cheaper than the nickel and gold used in ENIG. Additionally, the equipment and chemicals used for HASL are widely available and less expensive compared to those used for ENIG.
ENIG Cost
ENIG is typically more expensive than HASL due to the higher cost of the materials and the more complex processing steps involved. The nickel and gold used in the ENIG process are more expensive than the solder used in HASL. Furthermore, the auto-catalytic chemical reaction used to deposit the nickel layer requires specialized equipment and chemicals, which can add to the overall cost. However, the higher cost of ENIG may be justified for applications that require superior flatness, durability, or compatibility with lead-free assembly processes.
Difference 5: Suitability for Fine-Pitch Components
The suitability of HASL and ENIG for fine-pitch components depends on the flatness and coplanarity of the surface finish.
HASL and Fine-Pitch Components
HASL may not be the best choice for assembling fine-pitch components, such as small BGAs or chip-scale packages (CSPs). The uneven surface created by the hot air solder leveling process can lead to issues with component placement and soldering. The solder bumps on fine-pitch components may not make proper contact with the pads, resulting in poor solder joints or open circuits.
ENIG and Fine-Pitch Components
ENIG, on the other hand, is well-suited for assembling fine-pitch components due to its excellent flatness and coplanarity. The thin, uniform layers of nickel and gold closely follow the contours of the pads, ensuring proper contact between the component leads and the PCB surface. This flatness is crucial for the successful assembly of high-density and fine-pitch components, reducing the risk of soldering defects and improving the reliability of the final product.
Difference 6: Compatibility with Lead-Free Assembly
The compatibility of HASL and ENIG with lead-free assembly processes is an important consideration, as the electronics industry continues to shift towards lead-free manufacturing.
HASL and Lead-Free Assembly
Traditional HASL using a tin-lead solder alloy is not compatible with lead-free assembly processes. If a lead-free solder paste is used during assembly, there may be issues with solder joint formation and reliability due to the difference in melting points between the HASL surface and the lead-free solder paste. To address this issue, some PCB manufacturers offer lead-free HASL options, which use a tin-based solder alloy instead of tin-lead. However, lead-free HASL may not provide the same level of solderability and wetting as traditional tin-lead HASL.
ENIG and Lead-Free Assembly
ENIG is fully compatible with lead-free assembly processes, as the gold layer provides excellent solderability and wetting properties for lead-free solder alloys. The nickel layer acts as a barrier, preventing the diffusion of copper into the solder joint, which can lead to the formation of brittle intermetallic compounds. This compatibility with lead-free assembly makes ENIG a popular choice for manufacturers who need to comply with RoHS (Restriction of Hazardous Substances) regulations or other environmental standards.
Difference 7: Thermal Shock Resistance
The thermal shock resistance of HASL and ENIG is an important factor to consider for applications that involve exposure to extreme temperature changes.
HASL Thermal Shock Resistance
HASL boards have good thermal shock resistance due to the presence of the solder layer, which can absorb some of the mechanical stress caused by rapid temperature changes. The tin-lead solder alloy used in HASL has a relatively low melting point and good ductility, allowing it to expand and contract without cracking or delaminating from the copper surface. However, the thermal shock resistance of HASL may be affected by the quality of the solder leveling process and the presence of voids or defects in the solder layer.
ENIG Thermal Shock Resistance
ENIG boards also offer good thermal shock resistance, thanks to the presence of the nickel layer. Nickel has a coefficient of thermal expansion (CTE) that is closer to that of copper compared to gold, which helps to minimize the stress caused by temperature changes. The nickel layer also provides a strong mechanical bond between the copper and the gold layer, reducing the risk of delamination during thermal cycling. However, the thermal shock resistance of ENIG can be affected by the quality and thickness of the nickel and gold layers. If the nickel layer is too thin or has defects, it may not provide adequate protection against thermal stress.
Difference 8: Copper Exposure and Wire Bonding
The ability to expose copper pads and suitability for wire bonding are important considerations for certain applications, such as chip-on-board (COB) and hybrid circuits.
HASL Copper Exposure and Wire Bonding
HASL is not well-suited for applications that require exposed copper pads or wire bonding. The solder layer used in HASL covers the entire surface of the PCB, including the copper pads. Removing the solder to expose the copper can be challenging and may result in damage to the pads or traces. Additionally, the uneven surface of HASL can make it difficult to achieve reliable wire bonds, as the bonding tool may not make proper contact with the pads.
ENIG Copper Exposure and Wire Bonding
ENIG, on the other hand, allows for selective exposure of copper pads and is suitable for wire bonding applications. The nickel and gold layers can be selectively deposited on the PCB surface, leaving the copper pads exposed where necessary. This selective plating is typically achieved using a photolithographic process or a selective plating resist. The exposed copper pads can then be used for wire bonding or other interconnect methods. The flat and coplanar surface provided by ENIG also promotes reliable wire bonding, as the bonding tool can make consistent contact with the pads.
Difference 9: Visual Appearance
The visual appearance of HASL and ENIG boards can be quite different, which may be a consideration for certain applications or customer preferences.
HASL Visual Appearance
HASL boards have a distinctive matte appearance due to the presence of the solder layer. The solder surface may have a slightly wavy or dimpled texture, depending on the quality of the solder leveling process. The color of the solder can range from silver to slightly yellowish, depending on the composition of the solder alloy and the age of the board. Some customers may perceive the matte appearance of HASL as a sign of a lower-quality finish, even though it does not necessarily affect the functional performance of the board.
ENIG Visual Appearance
ENIG boards have a bright, reflective appearance due to the presence of the gold layer. The gold surface is typically very smooth and uniform, with a slightly yellowish color. The reflective appearance of ENIG can give the impression of a high-quality, premium finish, which may be desirable for certain applications or customers. However, the appearance of ENIG can change over time, as the gold layer may tarnish or discolor if exposed to certain environmental conditions or chemicals.
Difference 10: Reworkability
The ability to rework or repair assembled PCBs is an important consideration, especially for prototyping or low-volume production.
HASL Reworkability
HASL boards are generally easier to rework compared to ENIG boards. The solder layer on HASL can be easily melted using a soldering iron or hot air tool, allowing components to be removed and replaced without damaging the pads or traces. The solder can also be easily cleaned off the pads using solder wick or a desoldering pump, leaving a clean surface for new components to be soldered in place.
ENIG Reworkability
ENIG boards can be more challenging to rework, as the nickel and gold layers must be removed to expose the copper pads. This can be done using a chemical etching process or mechanical abrasion, but it requires more skill and specialized equipment compared to reworking HASL boards. Additionally, the thin gold layer on ENIG can be easily scratched or damaged during the rework process, which can affect the solderability and reliability of the repaired board. If the nickel layer is exposed during rework, it can oxidize quickly, making it difficult to achieve good solder joints.
Frequently Asked Questions (FAQ)
1. Can HASL be used for lead-free assembly?
Traditional HASL using a tin-lead solder alloy is not compatible with lead-free assembly. However, some PCB manufacturers offer lead-free HASL options that use a tin-based solder alloy instead. Lead-free HASL may not provide the same level of solderability and wetting as traditional tin-lead HASL.
2. Is ENIG more expensive than HASL?
Yes, ENIG is typically more expensive than HASL due to the higher cost of the materials (nickel and gold) and the more complex processing steps involved. However, the higher cost of ENIG may be justified for applications that require superior flatness, durability, or compatibility with lead-free assembly processes.
3. Which surface finish is better for fine-pitch components, HASL or ENIG?
ENIG is generally better suited for assembling fine-pitch components due to its excellent flatness and coplanarity. The thin, uniform layers of nickel and gold closely follow the contours of the pads, ensuring proper contact between the component leads and the PCB surface. HASL may not be the best choice for fine-pitch components, as the uneven surface created by the hot air solder leveling process can lead to issues with component placement and soldering.
4. Can ENIG be used for wire bonding applications?
Yes, ENIG is suitable for wire bonding applications. The nickel and gold layers can be selectively deposited on the PCB surface, leaving the copper pads exposed where necessary. The flat and coplanar surface provided by ENIG also promotes reliable wire bonding, as the bonding tool can make consistent contact with the pads.
5. Which surface finish is easier to rework, HASL or ENIG?
HASL boards are generally easier to rework compared to ENIG boards. The solder layer on HASL can be easily melted and cleaned off the pads using standard soldering tools and techniques. ENIG boards can be more challenging to rework, as the nickel and gold layers must be removed to expose the copper pads, which requires more skill and specialized equipment.
Comparison Table: HASL vs. ENIG
Characteristic | HASL | ENIG |
---|---|---|
Flatness and Coplanarity | Slightly uneven surface | Excellent flatness and coplanarity |
Solderability | Excellent, but limited to tin-lead solder | Good, compatible with lead-free solder |
Durability and Shelf Life | Good, but can tarnish over time | Excellent, longer shelf life |
Cost | Lower cost | Higher cost |
Suitability for Fine-Pitch Components | Limited by uneven surface | Excellent, due to flat surface |
Compatibility with Lead-Free Assembly | Not compatible, unless using lead-free HASL | Fully compatible |
Thermal Shock Resistance | Good, but affected by solder quality | Good, but affected by nickel and gold quality |
Copper Exposure and Wire Bonding | Not well-suited | Allows selective exposure, suitable for wire bonding |
Visual Appearance | Matte, slightly wavy | Bright, reflective, uniform |
Reworkability | Easier to rework | More challenging to rework |
Conclusion
In conclusion, HASL and ENIG are two popular surface finish options for PCBs, each with its own set of advantages and disadvantages. HASL is a cost-effective and widely used method that provides excellent solderability, but it may not be suitable for fine-pitch components or lead-free assembly processes. ENIG, on the other hand, offers superior flatness, durability, and compatibility with lead-free assembly, but it comes at a higher cost and may be more challenging to rework.
When choosing between HASL
No responses yet